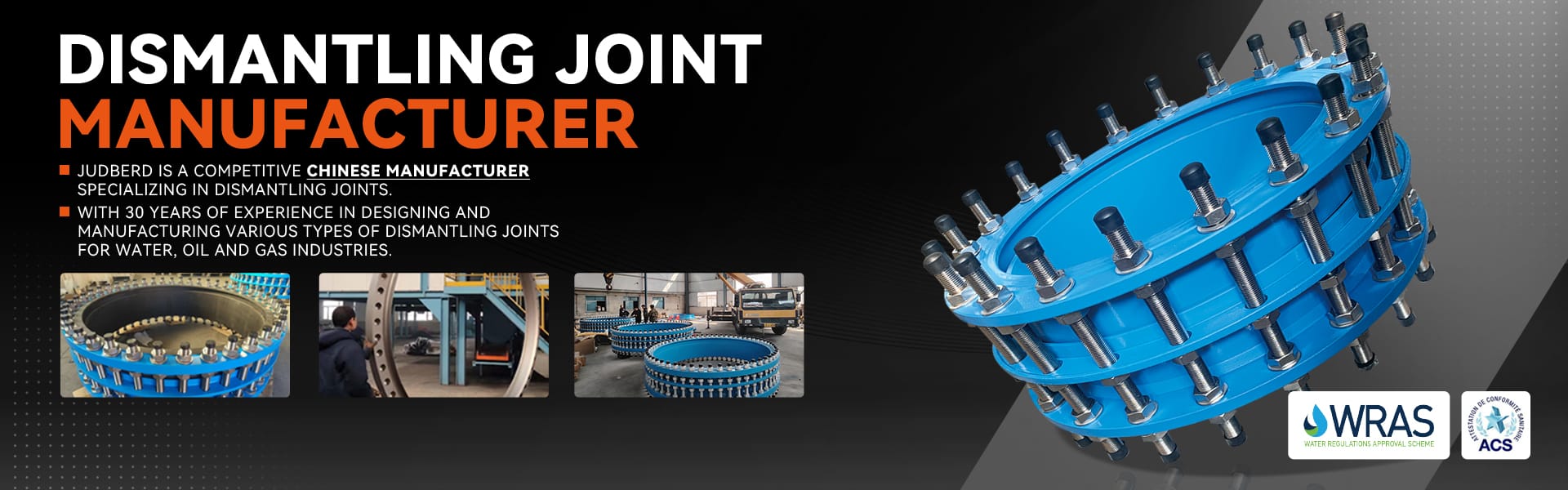
Dismantling Joint
Dismantling joint is a pivotal double-flanged fitting in pipe systems that supplies critical longitudinal adjustment and restraint.
It allows for speedy disconnections for maintenance or replacement of components like valves, pumps, and instruments, also permits precise pipe and equipment alignment by providing essential longitudinal adjustments and ensures stability by restraining longitudinal movements.
Judberd is competitive manufacturer for dismantling joint in china, our dismantling joint include below types
For Firefighting System
Heavy Duty Material Ductile Iron Standard EN545/AWWA C219/AS/NZS2280 Pressure PN10/PN16/PN25/PN35/
Class125/Class150/Class300
Series No. DJ009
Heavy Duty Material carbon steel Standard EN545/AWWA C209/AS/NZS2280
Pressure from PN10 to PN100, from class 125 to class 600
Series No. DJ007
Heavy Duty Material stainless steel Standard EN545/AWWA C209/AS/NZS2280
Pressure from PN10 to PN100, from class 125 to class 600
Series No. DJ008
Light Duty Material Ductile Iron Standard EN545/AWWA C209/AS/NZS2280
Pressure from PN10 to PN25, from class 125 to class 150
Series No. DJ011
Heavy Duty Material Ductile Iron Standard EN545 Pressure PN10/PN16/PN25
Series No. DJ001
Heavy Duty Material Ductile Iron Standard AWWA C219 Pressure ANSI Class150
Series No. DJ002
Heavy Duty Material Ductile Iron Standard AS/NZS2280 Pressure PN16 PN35
Series No. DJ003
Heavy Duty Material Ductile Iron Standard EN545 Pressure PN10/PN16/PN25
Series No. DJ006
Light Duty Material Ductile Iron Standard EN545/AWWA C209/AS/NZS2280
Small size design(from DN50 to DN600)
Series No. DJ004
Light Duty Material Ductile Iron Standard EN545/AWWA C209/AS/NZS2280
Big size design(from DN700 to DN2000)
Series No. DJ005
Light Duty Material Ductile Iron Standard EN545/AWWA C209/AS/NZS2280
Small size design(from DN50 to DN600)
Series No. DJ010
VIDEO
Pressure Test for DN1400 PN16 Dismantling Joint
Nylon 11 Coated Dismantling Joint
Dismantling Joint 3D Drawing
FBE coating adhesion test for dismantling joint , pull-off test
DN2600 PN25 dismantling joint
Dismantling joint In FBE Coating Workshop
Thickness inspection for Dismantling joint
AWWA C209 dismantling joint
Light weight dismantling joint
Stainless Steel Dismantling Joint
For neutral fluids such as water, oil, or gas at ambient temperature, a regular FBE coating is suitable. For corrosive or high-temperature substances, special surface treatments are required. For seawater, the interior can be lined with Ebonite and the exterior should be coated with corrosion-resistant paint or with Epoxy Glass Flake Coating inside and outside. For highly acidic liquids, corrosion-resistant nylon 11 is the best choice. For liquids above 100°C, a high temperature resistant epoxy powder must be used,For Impurity-rich pipeline, abrasion-resistant polyurethane inside lining should be used.
If the working pressure rating of your pipeline is ≤ 25bar, a ductile iron dismantling joint is the best choice due to its wide applicability, corrosion resistance, and competitive price. However, if the working pressure rating is ≥ 40bar, you need to choose a steel dismantling joint to withstand high pressure. The material of the steel can be carbon steel, stainless steel, or other alloy steel.
In North American countries such as the United States, Canada, and Mexico, AWWA209 standard dismantling joints are used. In Australia, New Zealand, and Fiji, AS/NZS2280 standard dismantling joints are used. The rest of the countries use dismantling joints according to the EN545 standard. Some new projects in Saudi Arabia also started using American standard dismantling joints recently.
Regardless of the standard, design, material, or surface coating for dismantling joints, Judberd can provide the right dismantling joint based on our 30 years of R&D experience. Both OEM and ODM are welcome.
Professional R&D Team
Our professional design team can provide recommendations for suitable products based on customers' local standards. Additionally, if customers have specific requirements regarding dismantling joint dimension, material, surface treatment, or other factors, we are capable of accommodating those needs
Suitable for high temperature and corrosive material
Our dismantling joint is designed to meet the requirements of special fluids or gases, including high temperatures, corrosiveness, and more. With our extensive experience, we are committed to satisfying our customers' needs.
Good Quality
We are dedicated to consistently producing high-quality dismantling joints. To ensure optimal performance, we meticulously machine nearly every surface of our dismantling joints.We supply our dismantling joint for many famous brands.
Competitive Price
We utilize various production processes to manufacture dismantling joints in different sizes. Additionally, our dedicated machining center allows us to have better cost control compared to our competitors, enabling us to offer more competitive prices.
All type certificated
We hold certifications such as GSK, WRAS, ACS, DVGW, NSF, and more, ensuring that we meet the specific requirements of customers in various markets
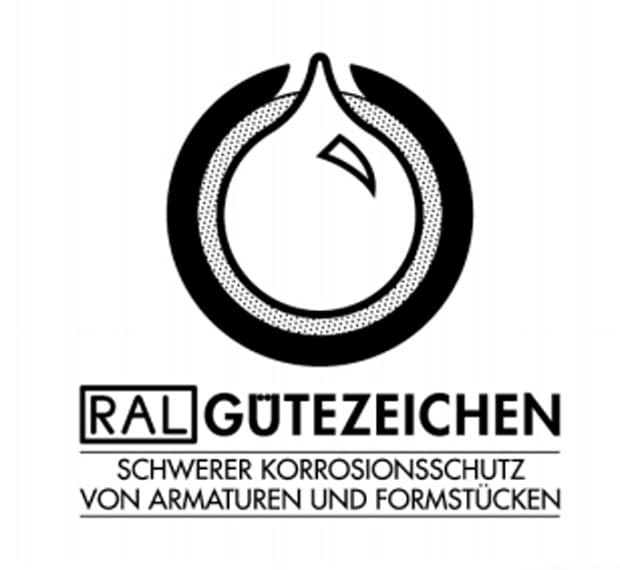
All type standard
Our dismantling joint can be according to EN545,AWWA C209 ,AS/NZS 2280 or other specified standards.Please note different market need different standard dismantling joint, wrong standard dismantling joint have different flange dimension which will cause no way to connect with each other.
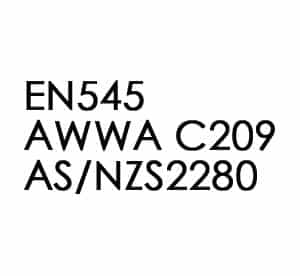
Judberd Advantage
Although we are committed to providing high-quality dismantling joints, For small-sized dismantling joints, we use vertical molding lines for casting and have dedicated machining pattern and machining centers for dismantling joints. Therefore, compared to other suppliers, we can offer more competitive prices.
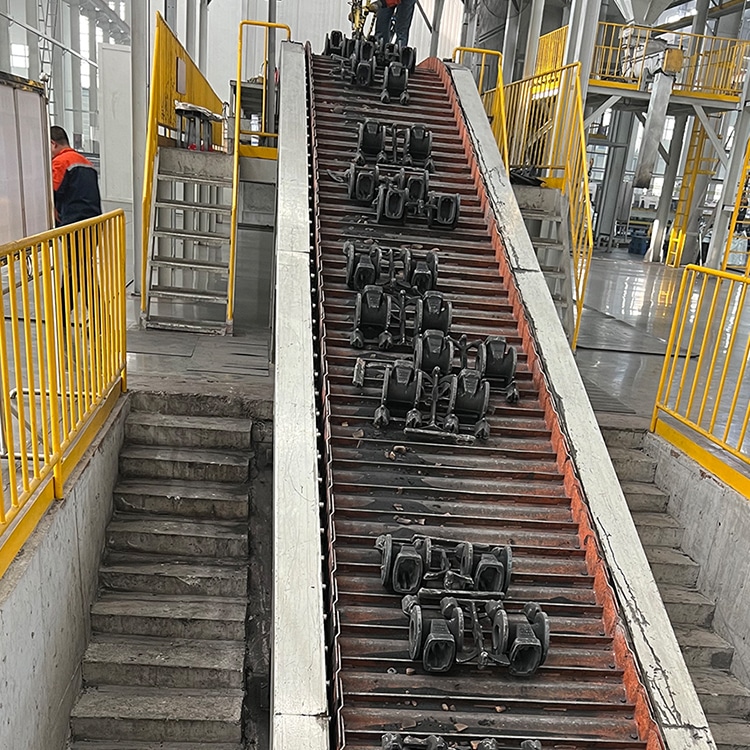
Judberd small size dismantling joint castings are produced by the DISA molding line
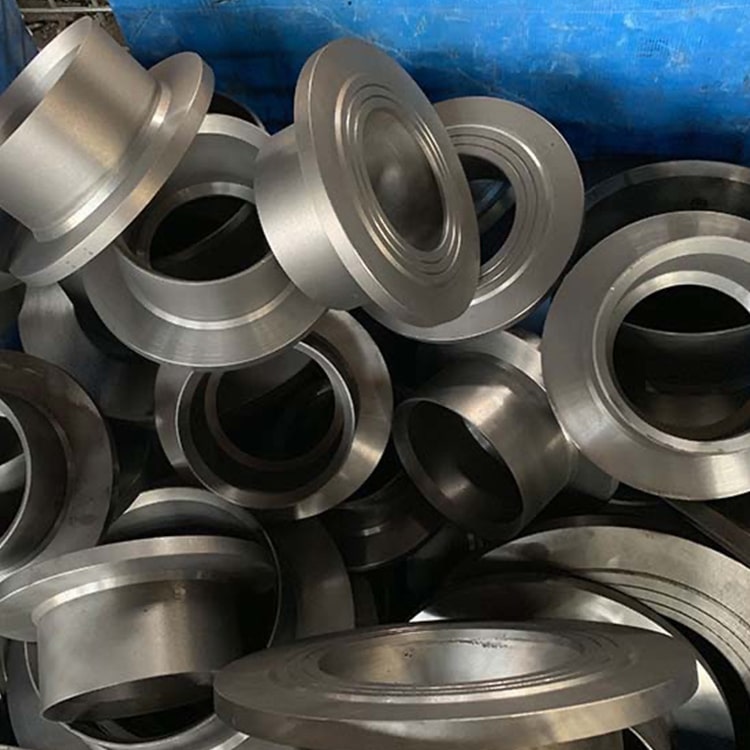
We machine almost 100% of the body surface, We supply many casting body without coating to famous brands

Good coating quality ,WRAS,ACS,DVGW,NSF certificate is available
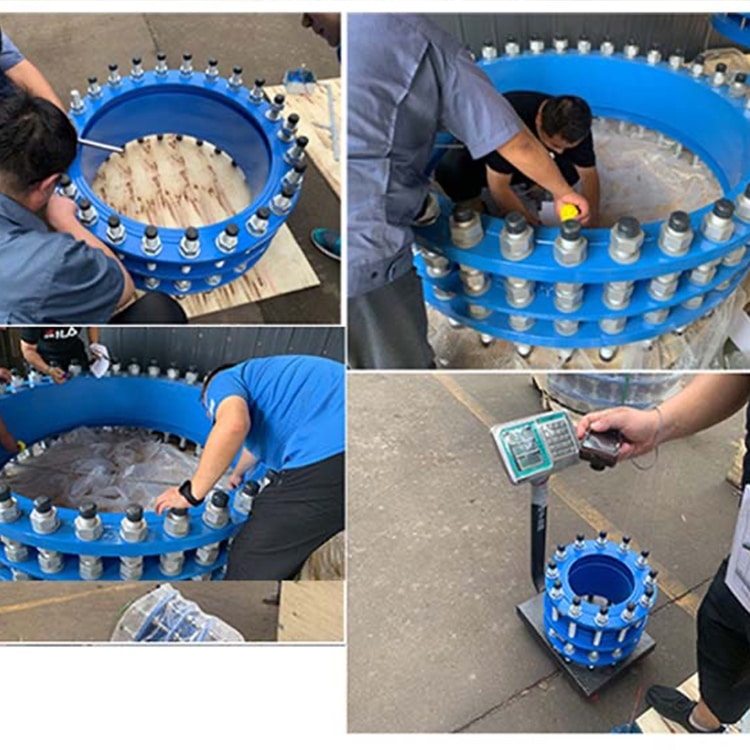
Any inspection is welcome
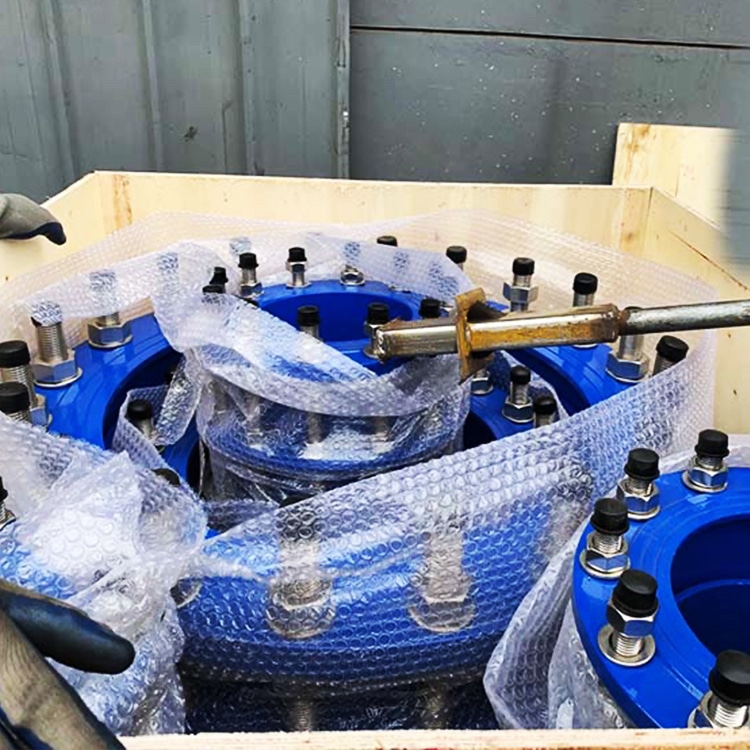
Check if the stainless steel bolts are magnetic
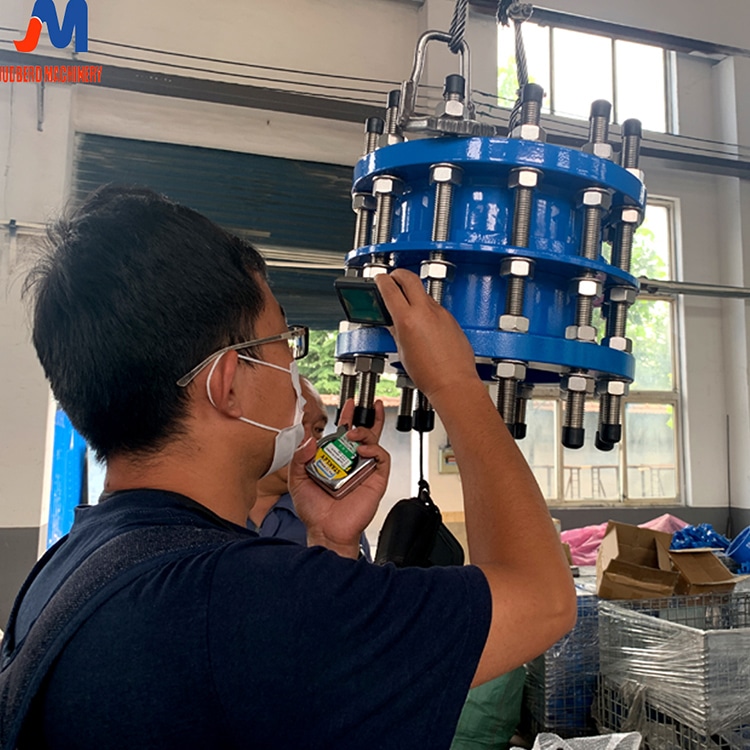
Third party inspection is also welcome
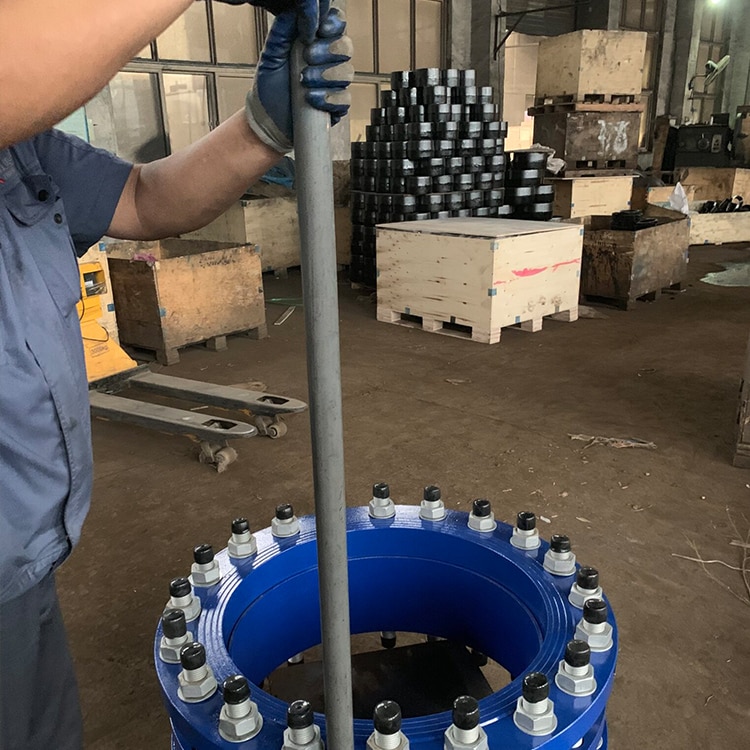
coating adhesion testing is done
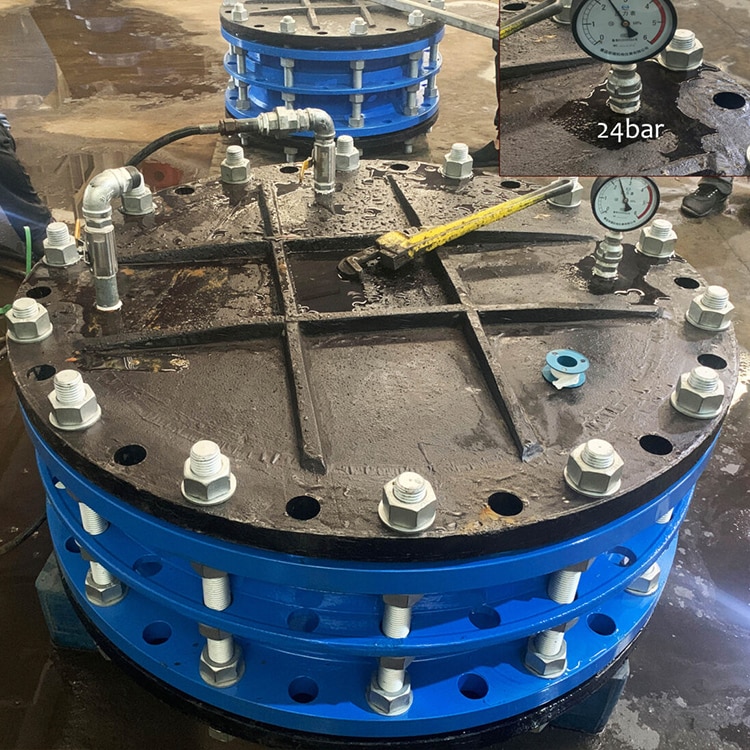
Pressure test for dismantling joint according to EN12266
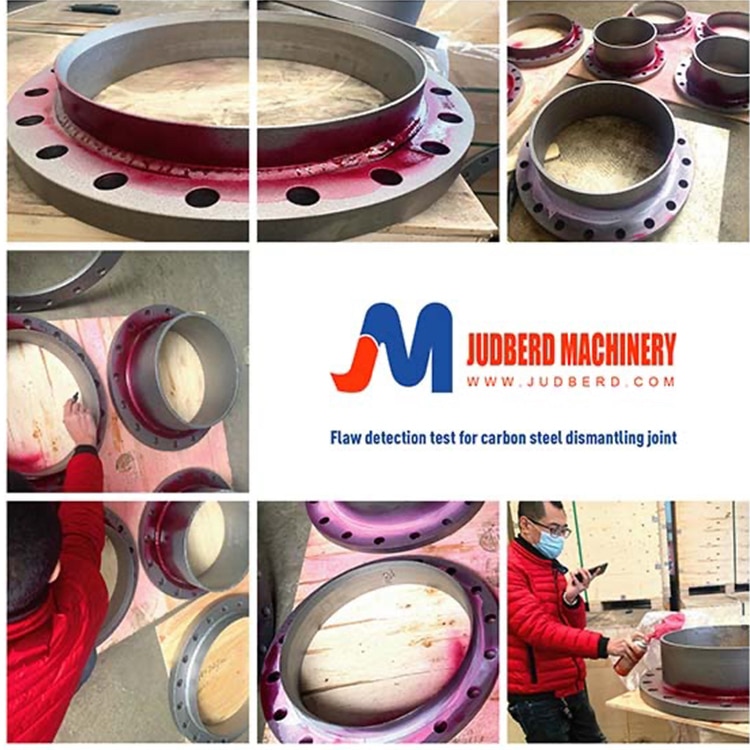
Strictly inspect the weld quality of the steel dismantling joint
Production Process
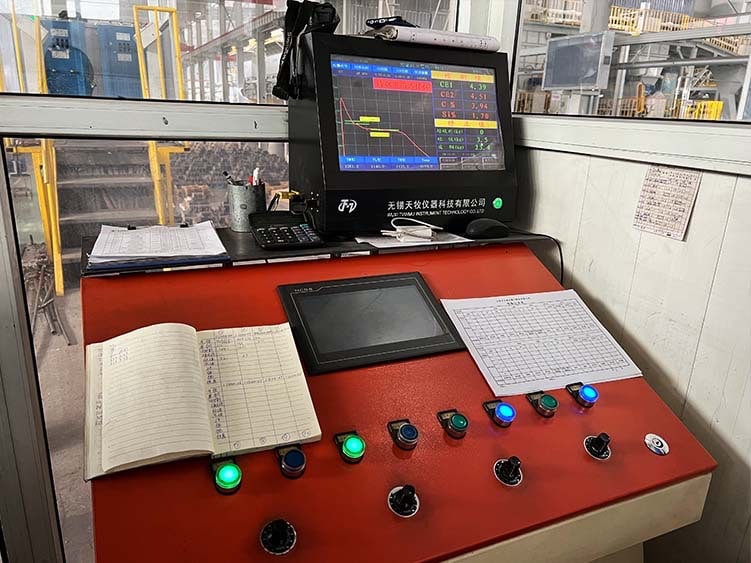
1, Inspection for material
We have a furnace front analyzer to monitor the chemical composition, and simultaneously perform chemical composition, mechanical property, and spheroidization rate testing on a ladle of molten iron at both the furnace beginning and last. This ensures that the quality of the molten iron meets the required standards.
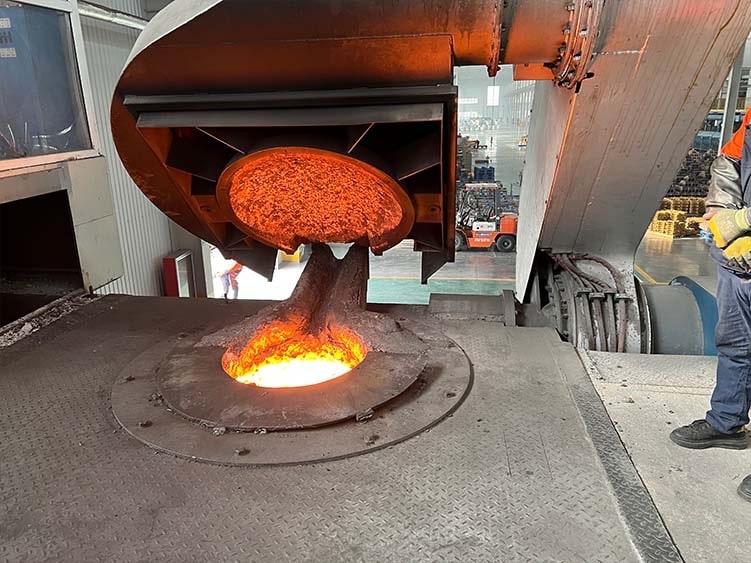
2,Casting
We have replaced the previous coal-fired furnace with an electric furnace for smelting molten iron, ensuring that our production meets environmental requirements
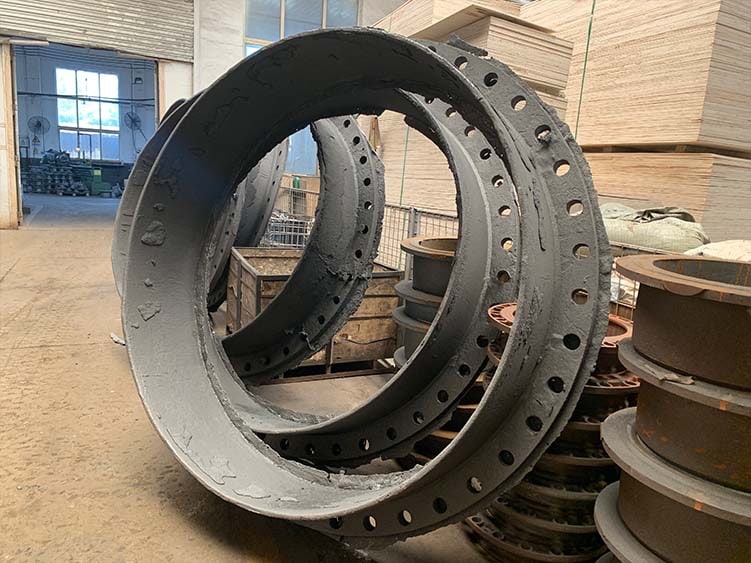
3,Casting Inspection
After casting , we need to check the casting to see if any casting defects are exist.For those with casting defects, the engineer will judge whether the casting should be discarded or can be repaired.
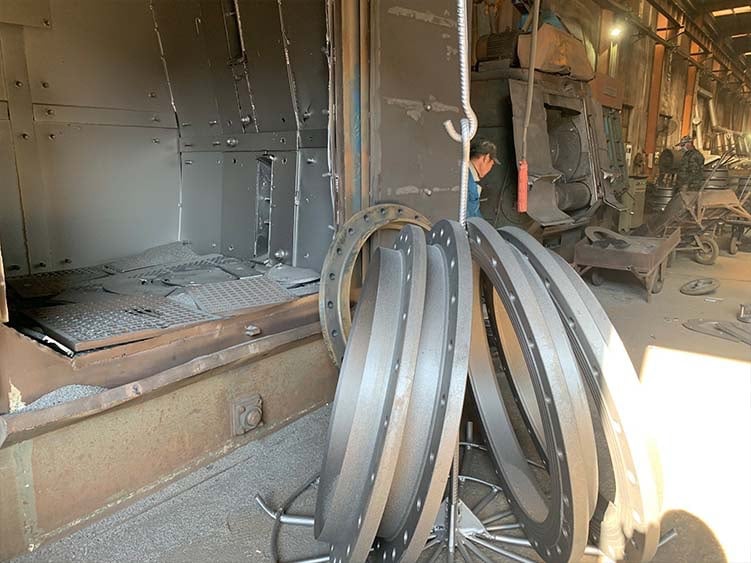
4,Polishing &Shot blasting
We need to grind the dismantling joint body surface to remove excess parts, so that the casting meets the dimensional requirements of the product. And the surface becomes smooth.Then the casting needs to be shot blasted before machining to remove dust and impurities from the surface, please note 2nd sand blasting is needed after machining to remove rust from the surface of the casting, dust and poor adhesion of the surface due to grinding etc, in preparation for FBE coating
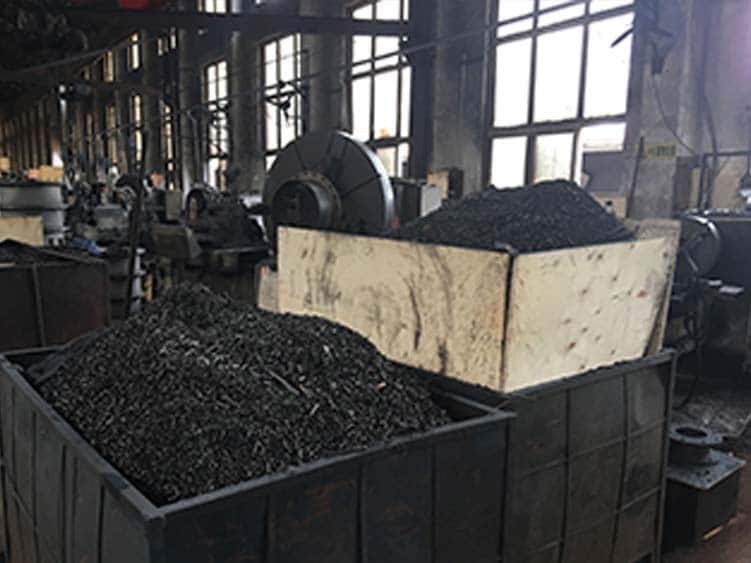
5,Machining
The dismantling joint are machined according to customer requirements. Judberd produces dismantling joint with 100% machined surfaces, except for the middle gland, so that the surface of the product is very smooth.
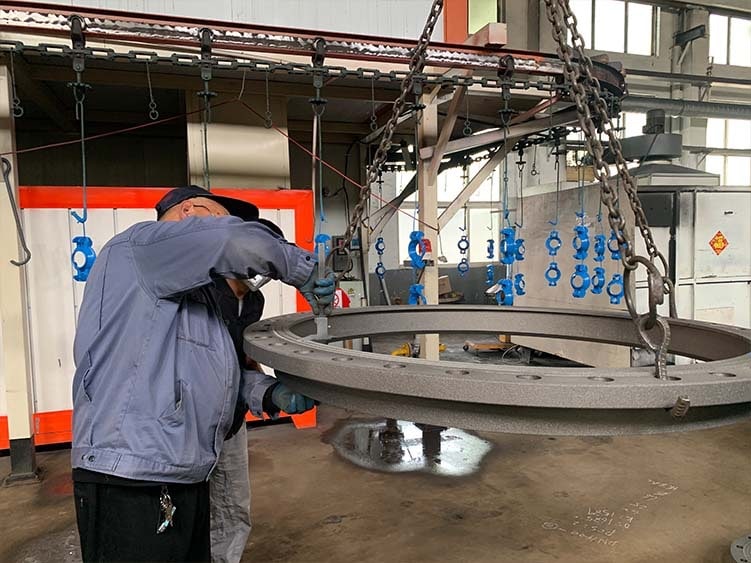
6,Dimension Inspection
After machining,Dimension inspection is necessary to assure everything dimension is right.
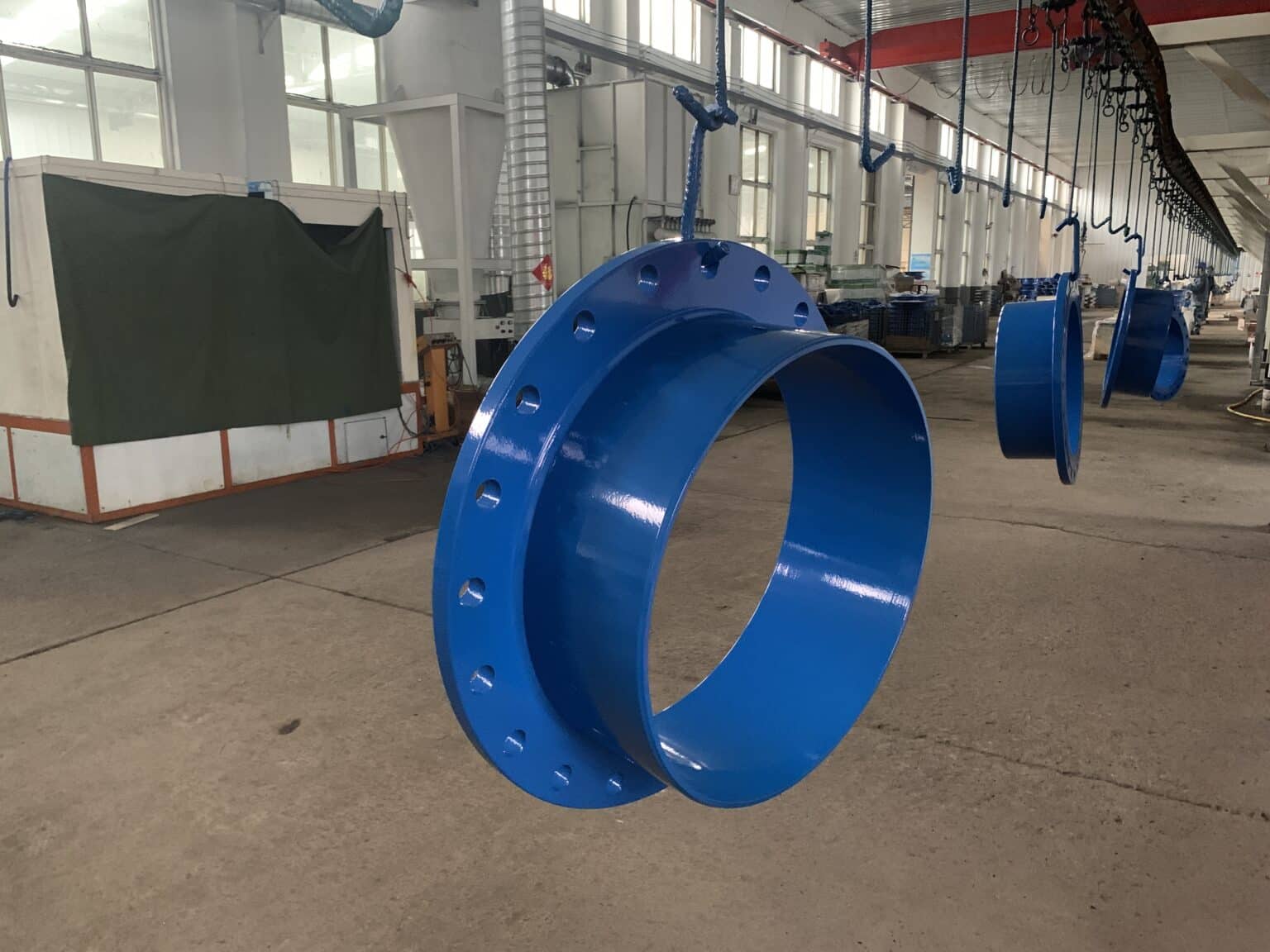
7,FBE Coating
Make FBE coating, nylon coating or other customer-specific coatings for dismantling joint surface
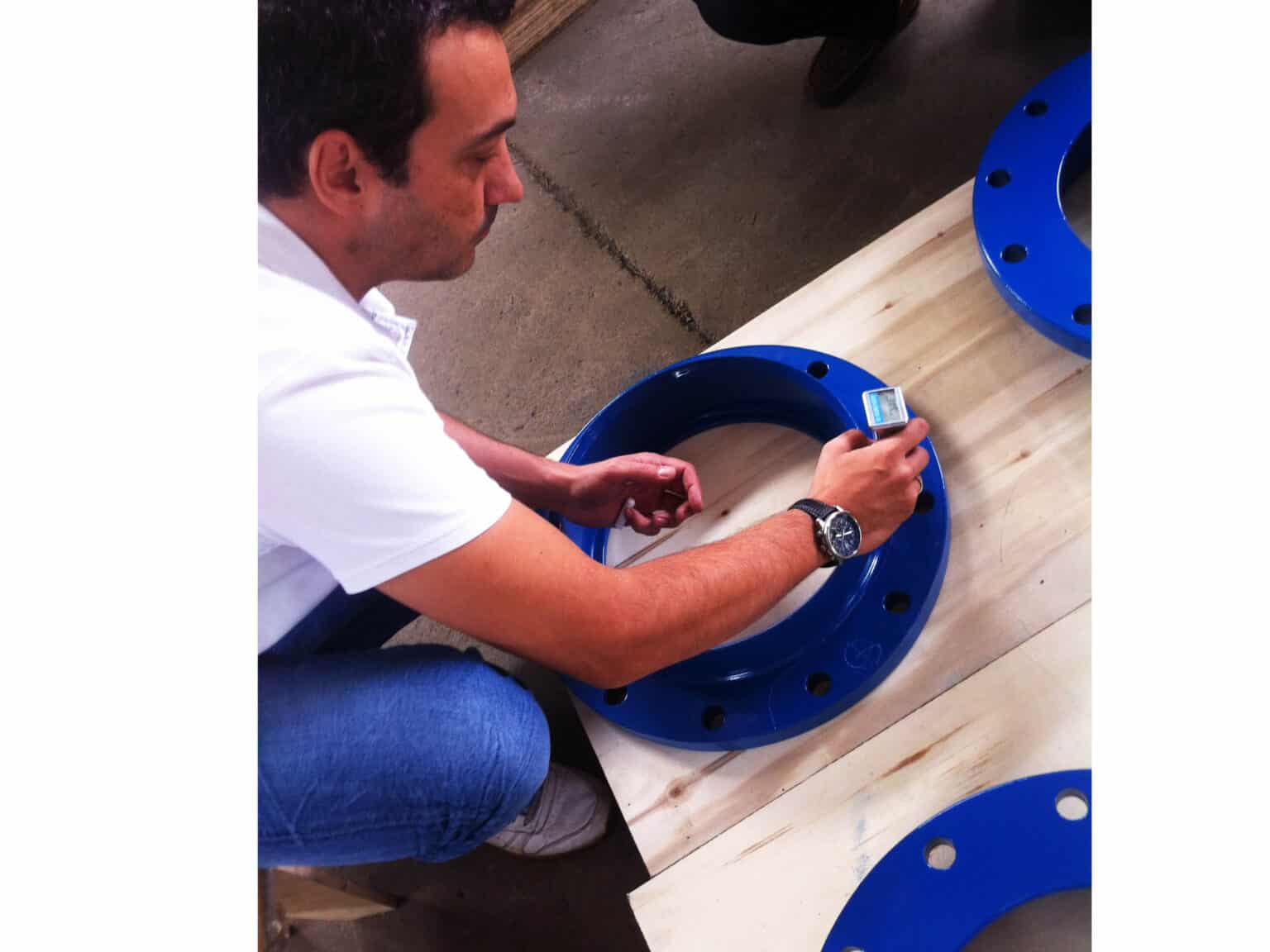
8,FBE Coating inspection
FBE coating inspection include coating appearance inspection, color difference inspection,thickness inspection,powder adhesion,coating performance etc inspection.
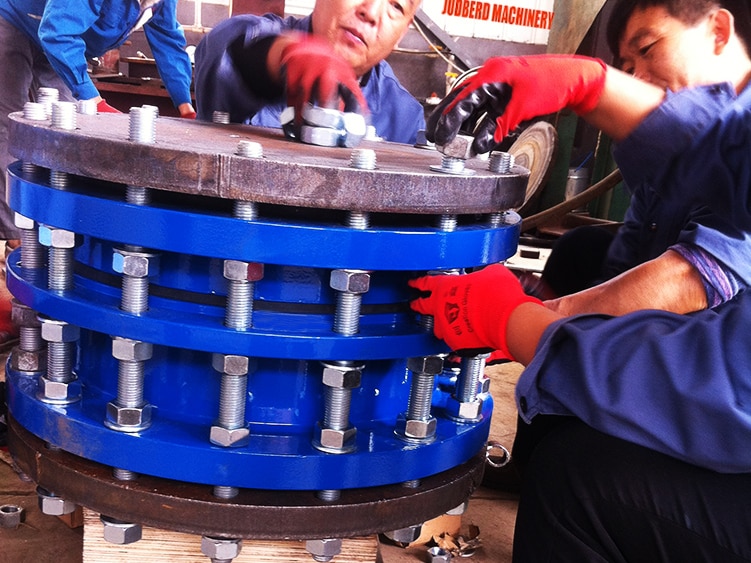
9,Assembling
Assemble gasket ,bolt and nuts .We use special fixtures to ensure that the reserved length of the bolts during installation is appropriate and as consistent as possible, allowing for direct installation without the need for secondary adjustments.
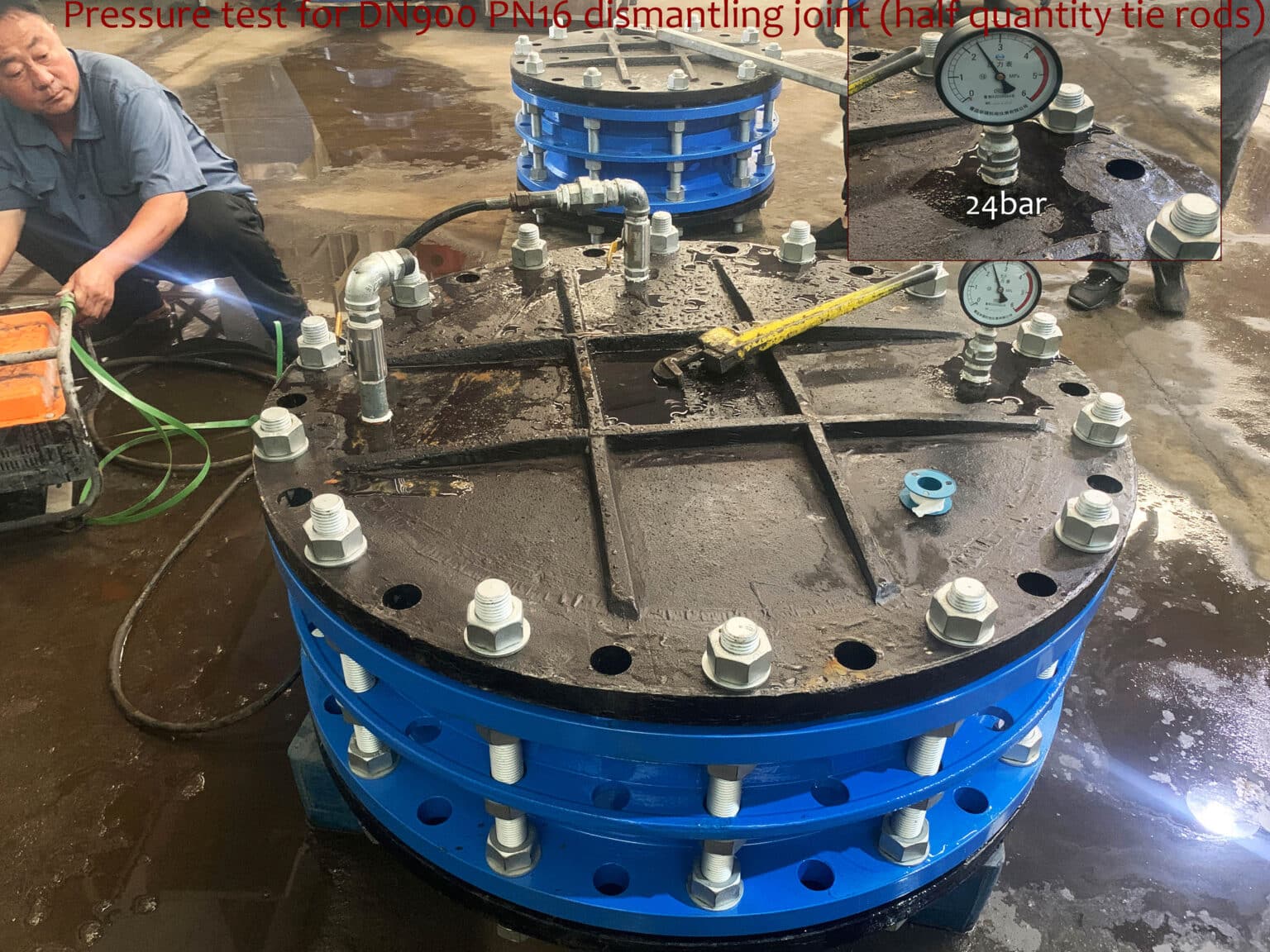
10,Pressure,Visual etc inspection
Test pressure should be 1.5 times of the working pressure with a holding time of 30s.Pressure test video and report is available

11,Packing
There many different packing way, we can use poly wood box, crate, or metal case etc to pack dismantling joint.We can also use moisture-proof plastic bags with desiccants for packaging

12,Despatchment
We can despatch our dismantling joint by sea, by train or by air, if you need us despatch by train, you need to tell us before packing to pack the goods according to train despatchment rule :”Cannot lean forward or backward, cannot lean left or right”
Dismantling Joint Parts
A dismantling joint consists of 3 parts, 1 is flange spigot, 2 is flange adaptor, 3 is tie rods, where 2 flange adaptor consists of gland (Fig No.2), gasket (Fig No.4) and flange adaptor body (Fig No.3), 3 tie rods consists of bolts, nuts and washers.
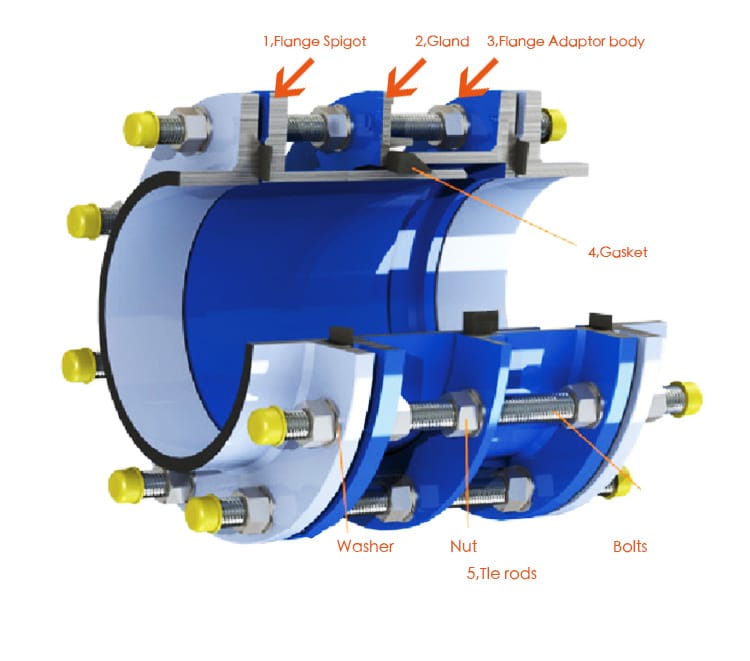
Dismantling Joint Parts
Dismantling Joint working Principle
The dismantling joint can be different lengths when flange spigot moves inside the flange adaptor. When the flange spigot move into the flange adaptor, it shortens in length, allowing the removal of valves, pumps, metering devices, filters, pipe branches and other items. When the flange spigot comes out of the flange adaptor, the connected items can be installed.
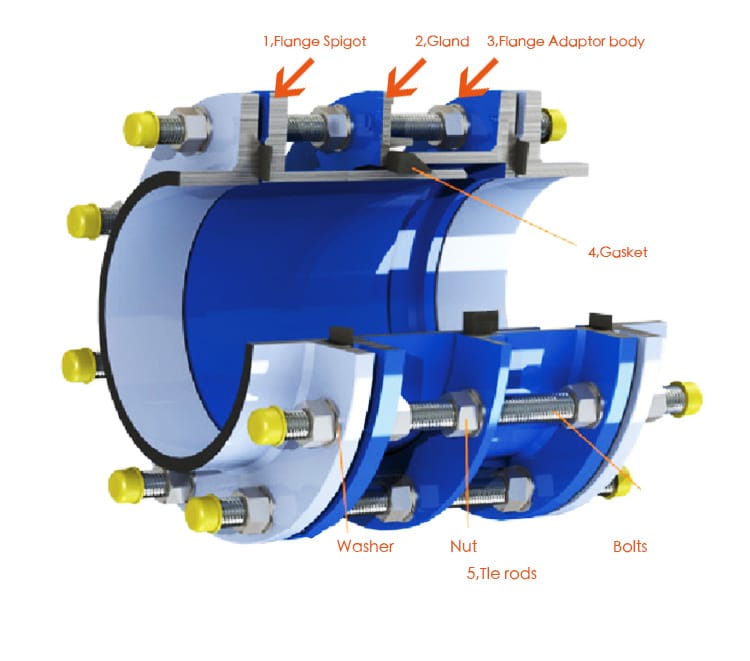
Dismantling Joint working Principle
Dismantling Joint Use
Dismantling joints are widely used in multiple industries and sectors, especially in piping systems that require frequent maintenance and high reliability.
Water Treatment and Supply Systems: In municipal water supply and wastewater treatment plants to connect and maintain valves, pumps, and flow meters to ensure continuous water supply and stable operation of the system.
Oil and Gas Industry: In long-distance transportation pipelines, refineries, and chemical plants to connect and disconnect critical equipment to facilitate regular inspections and repairs, suitable for high-temperature and high-pressure environments.
Power and Energy Industry: In heating and cooling water systems in thermal power plants and nuclear power plants at critical connection points to ensure the safety and efficient operation of the system.
HVAC Systems: In heating and air conditioning systems to connect hot and cold water pipes to facilitate maintenance and replacement of critical equipment to ensure the efficient operation of the system.
Food and Beverage Industry: In production lines and sanitary piping systems to connect and maintain critical equipment such as filters and pumps to ensure the hygiene and efficiency of the production process.
Offshore and Shipbuilding Engineering: In the piping systems of ships and offshore platforms to connect and maintain critical nodes to ensure the reliability and safety of the system.
Dismantling joints improve the efficiency of installation and maintenance of piping systems, ensuring the efficient operation and safety of the system.
Dismantling joints can be used to connect pipes of various materials, such as DI pipe, steel pipe, HDPE pipe,GRP pipe etc, as long as the flange at the end of the pipe can be connected to the flange at the end of the dismantling joint, ensuring a good seal between the two flanges.
But Sometimes we need to connect dismantling joint with valves or other pipe instrument which have non common flanges, then special length bolts should be assembled to be enough for the flange connection between dismantling joint flanges and other parts flanges.
Because dismantling joint has a telescopic function, it is generally connected with vulnerable and important parts on pipelines such as valves, water meters, and pumps that require regular maintenance or replacement, so that they can be repaired or replaced regularly. Dismantling joint is a common and indispensable product on the pipeline.
With increasing demands for the convenience of pipeline maintenance in engineering projects, more and more dismantling joints are being used. Dismantling joints with better functionality are becoming increasingly popular.Now some supplier designed dismantling joint with butterfly valve together to simplified structure and also proved that the dismantling joint is very important for valves.
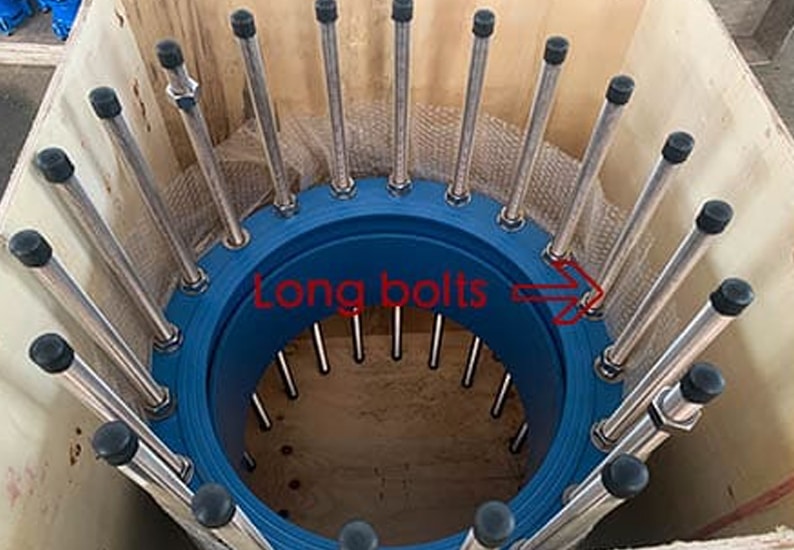
Dismantling Joint with Long Bolts for Special flange connection
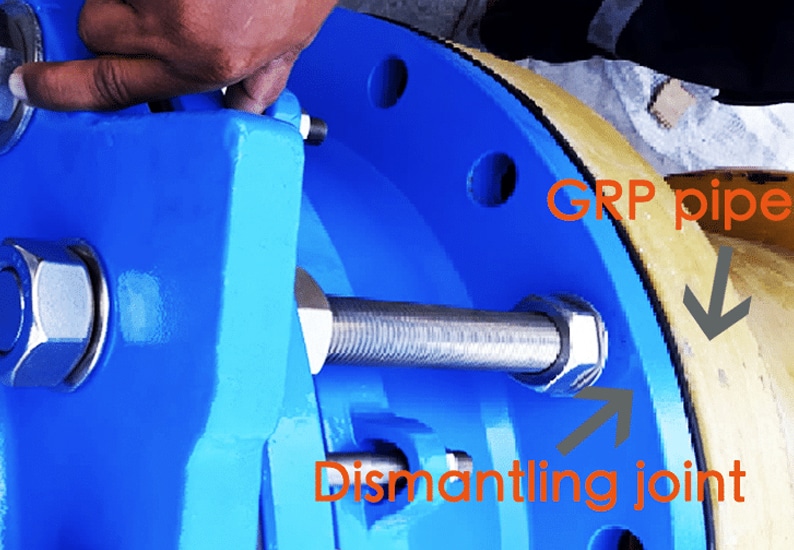
Dismantling joint connect with GRP pipe
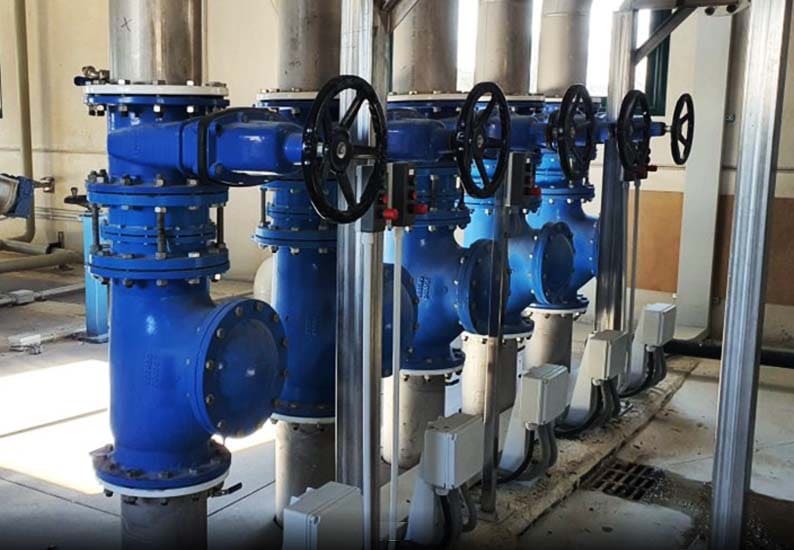
Dismantling joint assembled for gate valve and ball check valve
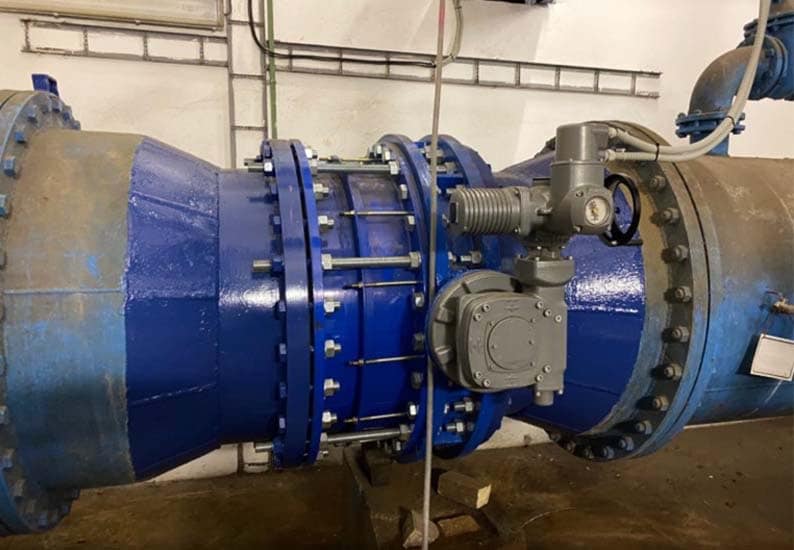
Dismantling joint for butterfly valve
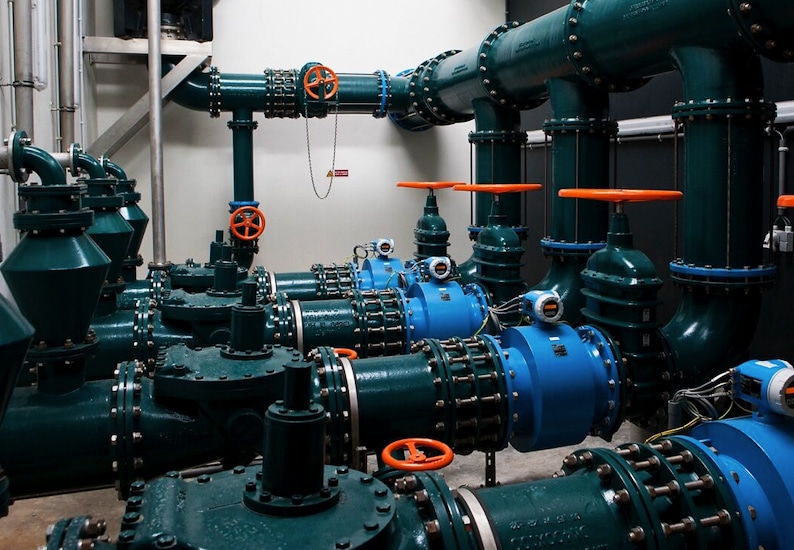
Dismantling joint for flow meter
Dismantling Joint Installation
For the two common types of dismantling joints, heavy duty and light duty, we have detailed the steps for installation. You can follow the installation steps below to correctly install the dismantling joint.
Dismantling Joint Types
Dismantling joints are divided into rigid dismantling joints (also known as thrust dismantling joints) and flexible dismantling joints (also known as non-thrust dismantling joints).
Rigid dismantling joint is rigid connection, long bolts through the entire dismantling joint and tighten up to mate flanges from other pipeline parts, so rigid dismantling joint can transfer the axial thrust of the pipeline, cannot deflect. Rigid dismantling joint cannot be used for conditions requiring angular deflection.
Flexible dismantling joint is a flexible connection, no long bolts through the entire dismantling joint, the dismantling joint cannot withstand axial thrust, can deflect. because it cannot withstand axial thrust, so it cannot be used for pipelines that are prone to axial thrust, such as thermal expansion and contraction, severe ground settlement, etc., and cannot be used for aboveground installation to prevent axial thrust from causing sealing failure.
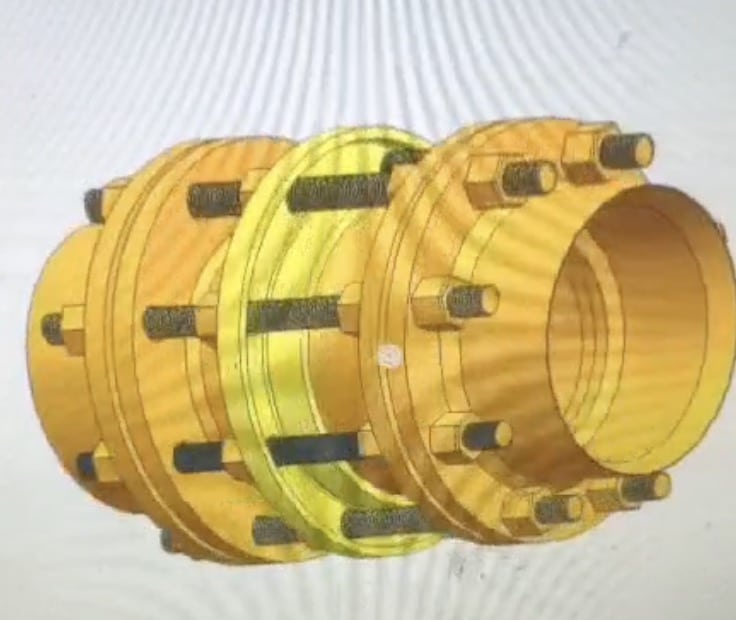
Rigid dismantling joint
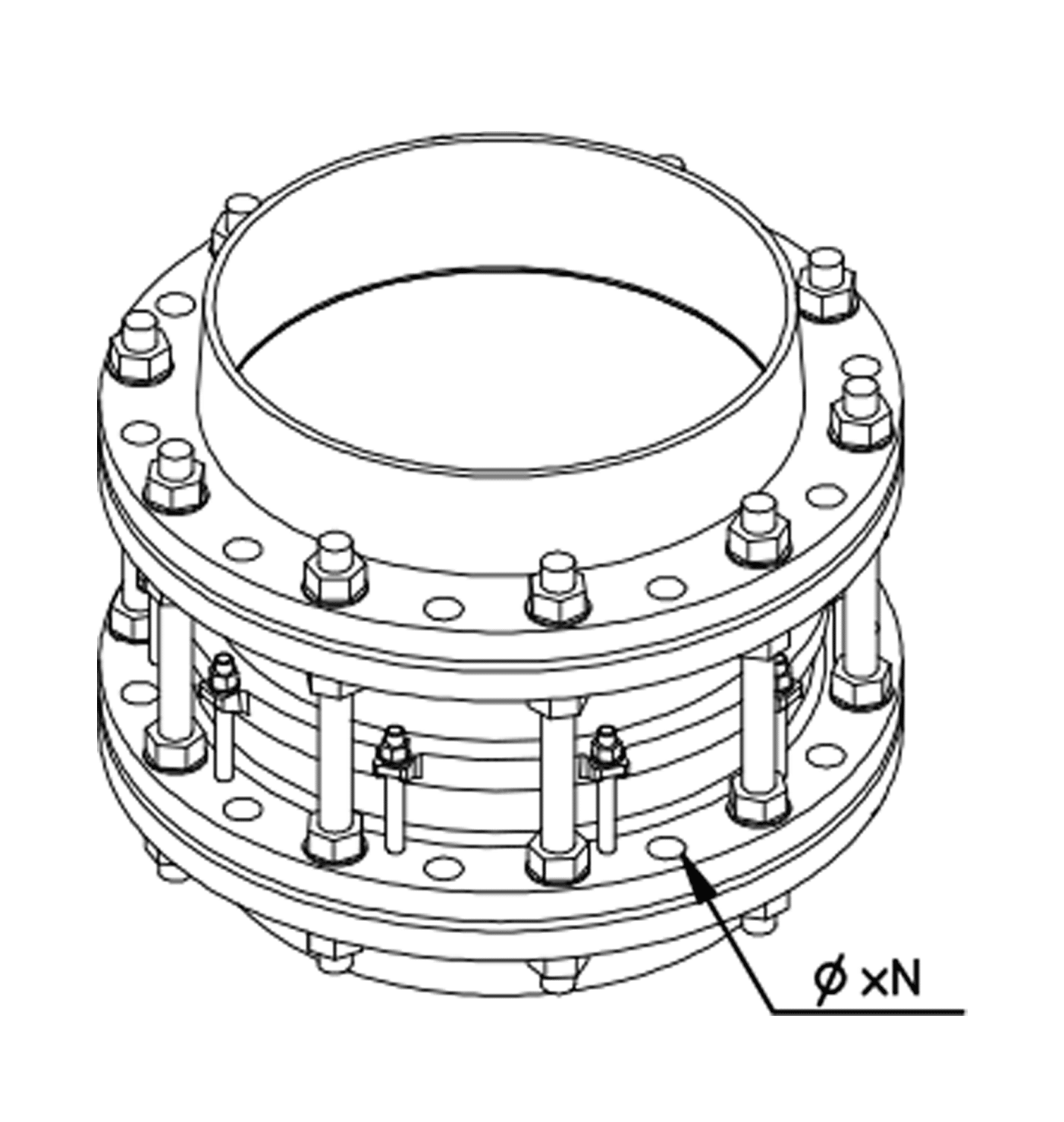
Rigid dismantling joint
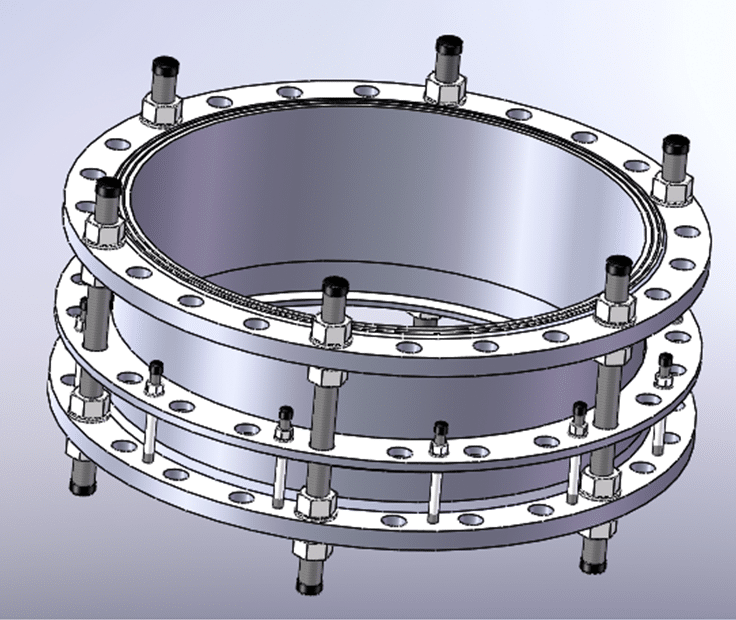
Rigid dismantling joint
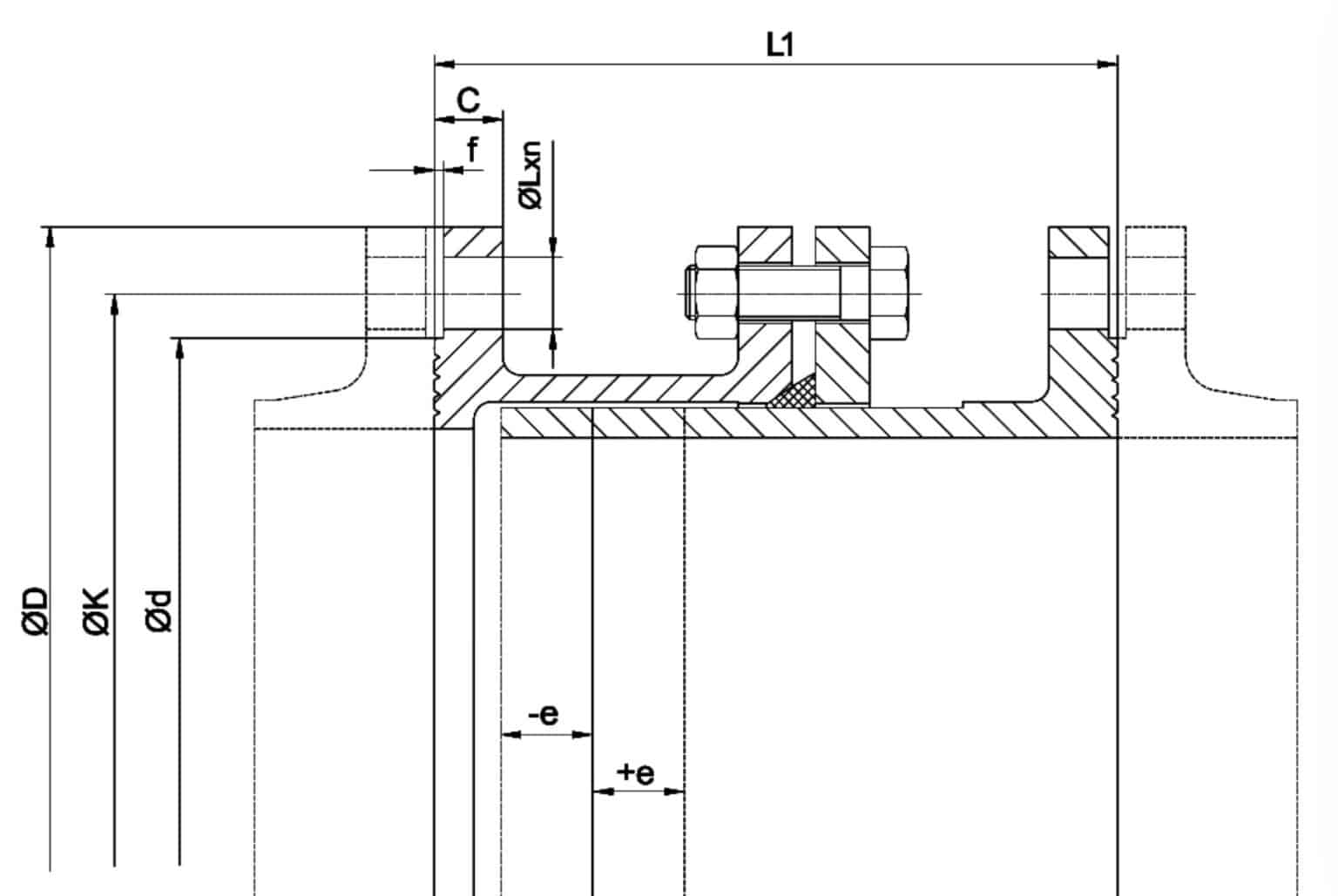
Flexible dismantling joint
Dismantling Joint Dimension and Drawing
The common dismantling joint size range is from DN50 to DN3000 (nominal diameter).
DIMENSION
Length (L) Dismantling joint length mean nominal length, minimum length, and maximum length. Generally speaking, the adjustable length range of dismantling joint is 50mm. Unless it is an extra-large size or there are special requirements for the pipe installation, the adjustable length range of 50mm is workable. Maximum length = nominal length + adjustable length range/2, minimum length = nominal length – adjustable length range/2
Flange dimensions (outside diameter (D), thickness, flange hole center distance, number of flange holes, and hole diameter) Match the flange standard of the pipe system. For example, if the flange standard of the pipe system to be connected is EN1092-2 PN16, then the standard of the dismantling joint flange should also be EN1092-2 PN16, unless the customer has special requirements. The outside diameter and thickness of the flange can be changed, but the connection and sealing function must be ensured.
DRAWING
Judberd can design dismantling joint according to customer requirements, As long as customers provide specific requirements, we can offer professionally functional dismantling joints. Below are the drawings we have designed for our customers, for your reference.
Dismantling Joint Material
Body (flange spigot, gland and flange adaptor body)
1,Ductile Iron,Suitable for systems with a working pressure less than or equal to PN25, generally used for piping systems such as water supply, drainage, fire protection, industrial water supply, and other systems with not very high pressures.
2,Carbon Steel,Suitable for high-pressure and high-temperature systems, providing higher strength and durability. Suitable for systems such as petroleum and gas.
3,Stainless Steel, Used for corrosive medium and systems requiring high sanitary standards, such as the food, beverage, and pharmaceutical industries.
Sealing Gasket
EPDM (Ethylene Propylene Diene Monomer Rubber) Commonly used in general water treatment and water supply systems.
NBR (Nitrile Butadiene Rubber) Mainly used to transport petroleum-based media such as oil, fuel, and lubricating oil.
Fluororubber (FKM) Suitable for high-temperature and corrosive media.
PTFE (Polytetrafluoroethylene) Used in the chemical industry and systems with high purity requirements.
Tie rods
Carbon Steel Material
Galvanized Carbon Steel Corrosion Resistance: low, suitable for low corrosion environments.Salt Spray Test Standard: According to ISO 9227, usually 48-96 hours.
Hot-Dip Galvanized Steel Corrosion Resistance: High, suitable for moderate to severe corrosion environments.Salt Spray Test Standard: According to ISO 1461, usually above 480 hours.
Dacromet coated carbon steel Corrosion Resistance: Very high, suitable for extreme corrosion environments.
Salt Spray Test Standard: According to ASTM B117, usually around 500-1000 hours or more.
Sheraplex coated carbon steel has very high rust protection, providing long-term protection in harsh environments.
Salt Spray Test Duration: According to relevant standards, the salt spray test can usually reach 1000 hours or even longer (ASTM B117 standard).
Stainless Steel Material
SS304: Suitable for light corrosion environments, lower cost
SS316: Suitable for harsh corrosive environments, especially environments with chloride ions such as marine environments, chemical and pharmaceutical equipment, higher cost, but provides higher corrosion resistance.
Dismantling Joint Standards
EN 545(Flange standard is ISO 7005-1/EN 1092)
AWWA C219(Flange standard is ANSI/ASME B16.5/B16.47)
AS/NZS2280(Flange standard is AS 4087)
RFQ
Why dismantling joint leaking?
If you have a leak with your dismantling joint, check the following to find the cause:
Installation Issues:
Insufficient Fastening: Bolts and nuts are not tightened according to the specified torque, resulting in loose joints.
Installation Deviation: The pipeline is not aligned during installation, resulting in uneven stress at the joints.
Aging or Damage of Seals:
Aging of Seals: Sealing materials (such as rubber gaskets) lose elasticity over time, leading to decreased sealing performance.
Seal Damage: Seals are damaged during installation or disassembly.
Pipe Vibration and Stress:
Pipe Vibration: Long-term vibration causes loosening at the joints and seal failure.
Thermal Expansion and Contraction: Temperature changes cause the pipe to expand and contract, increasing stress at the joints and causing the seals to fail.
Material Issues:
Improper Material Selection: Joint materials or seals are not suitable for the medium or working environment.
Material Defects: The dismantling joint itself has material defects or manufacturing defects.
Corrosion:
Internal Corrosion: The conveyed medium is corrosive, causing internal corrosion of the joints.
External Corrosion: External factors such as moisture or chemicals cause external corrosion of the joints.
Improper Operation:
Over-tightening: Over-tightening the bolts can cause the joints to deform or damage the seals.
Failure to Follow Procedures: Failure to follow the procedures for installation and maintenance.
Environmental Factors:
Temperature and Humidity Changes: Extreme changes in temperature and humidity can affect the sealing performance of the joints.
Chemical Environment: Exposure to harmful chemicals can accelerate the aging and damage of seals and joints.
To prevent leakage, it is recommended to strictly follow the specified procedures during installation and maintenance, choose the appropriate materials, and regularly inspect and replace aging seals.
Difference Between DI dismantling joint and Steel dismantling joint
There are some significant differences between ductile iron and steel dismantling joints in terms of material characteristics, performance, and applications. Here are some key differences:
Quality stability
DI dismantling joints are produced by moulds, so once the sample is qualified, the quality of the casting is basically not a problem, but MS dismantling joints are welded with carbon steel flanges and carbon steel plates, so the level of the welders and the welding process directly affect the quality of the dismantling joint. Therefore, the inspection of MS dismantling joints should focus on the inspection of the welding seam to prevent leakage of liquid due to welding quality.
Material Characteristics
Ductile Iron Dismantling Joints:
Material: Made of ductile iron, which is characterized by high strength and ductility.
Microstructure: The graphite in ductile iron is spherical, which enhances the material’s mechanical properties.
Corrosion Resistance: after coating/paint,It has good corrosion resistance and is suitable for harsh environments.
Steel Dismantling Joints:
Material: Made of carbon steel or alloy steel.
Microstructure: The microstructure of steel depends on its composition and heat treatment process, and it typically has high strength and ductility.
Corrosion Resistance: Steel requires surface treatments (such as galvanizing, painting ,coating etc.) to enhance its corrosion resistance, especially in corrosive environments.
Mechanical Properties
Strength and Ductility:
Ductile Iron Dismantling Joints: Ductile iron has high tensile strength and impact toughness and can absorb significant impact forces.
Steel Dismantling Joints: Steel is typically harder than ductile iron and has higher tensile and yield strengths, but in some cases, it may not have the same level of ductility as ductile iron.
Applications
Ductile Iron Dismantling Joints:
Application Environment: Suitable for applications such as water pipelines, sewage pipelines, and other environments that require corrosion resistance and high strength.
Typical Applications: Municipal engineering, water supply systems, industrial pipelines, etc.
Steel Dismantling Joints:
Application Environment: Suitable for applications that require high strength and pressure resistance, especially in environments that require wear resistance and high temperatures.
Typical Applications: Petrochemical industry, natural gas transportation, boiler pipelines, high-pressure pipelines, etc.
Maintenance and Lifespan
Ductile Iron Dismantling Joints:
Maintenance: Generally requires less maintenance and mainly involves checking the sealing and corrosion protection status.
Lifespan: Long lifespan, particularly in corrosive environments where they perform excellently.
Steel Dismantling Joints:
Maintenance: Require regular inspection and maintenance, particularly in corrosive environments where surface treatments and protective measures are necessary.
Lifespan: Long lifespan, but additional protective measures are needed in corrosive environments to extend the service life.
In summary, ductile iron and steel dismantling joints both have their advantages and disadvantages, and the choice between them should be made based on the specific application environment and requirements. Ductile iron is suitable for applications that require high corrosion resistance, while steel is more suitable for high-strength and high-pressure applications.
Difference Between Dismantling Joint and Expansion Joint
Dismantling joints and expansion joints are two common types of joints used in pipeline systems, but they serve different functions and are used in different situations. Here are the main differences between them:
Dismantling Joint:
Function:
Mainly used for the installation and disassembly of pipeline systems, allowing for the installation and maintenance of valves, pumps, instruments, etc.
Provides some length adjustment to allow for minor adjustments to the pipeline during installation or disassembly.The length of dismantling joint needs to be adjusted manually.
Structure:
Typically consists of two flanges, a pipe section with adjustable length, bolts and sealing gasket.
Designed to allow for some axial movement but does not provide significant angular or lateral displacement compensation.
Application:
Used in pipeline systems that require frequent maintenance, inspection, or equipment replacement, such as water treatment, water supply, sewage treatment, etc.
Key Features:
Provides convenient disassembly and assembly functions.
Allows for a certain range of length adjustment but does not provide compensation for expansion or contraction.
Expansion Joint:
Function:
Mainly used to absorb the expansion and contraction of pipelines due to temperature changes, ground settlement, or other reasons.
Provides compensation for axial, lateral, and angular displacement to protect pipeline systems from the effects of thermal expansion and contraction or other displacements.
Structure:
Common types include bellows expansion joints, rubber expansion joints, and slip expansion joints.
Bellows expansion joints are composed of metal bellows and flanges or welded ends, while rubber expansion joints consist of a rubber body and reinforcement layers.
Application:
Widely used in various industrial pipeline systems such as heating pipelines, steam pipelines, chemical pipelines, power equipment, etc., where systems need to accommodate temperature changes and displacements.
Key Features:
Absorbs the expansion and contraction of pipeline systems to reduce the impact of stress and displacement on the pipeline.
Provides multi-directional displacement compensation, including axial, lateral, and angular.
Summary:
Dismantling Joint:
Mainly used for the installation and disassembly of pipeline systems to facilitate the maintenance and replacement of equipment.
Provides some length adjustment but is not used to compensate for expansion and contraction.
Expansion Joint:
Mainly used to absorb the expansion and contraction of pipelines due to temperature changes, etc.
Provides multi-directional displacement compensation to protect the pipeline system from stress and displacement.
The two have different functions in pipeline systems, and the appropriate type of joint should be selected based on specific requirements.
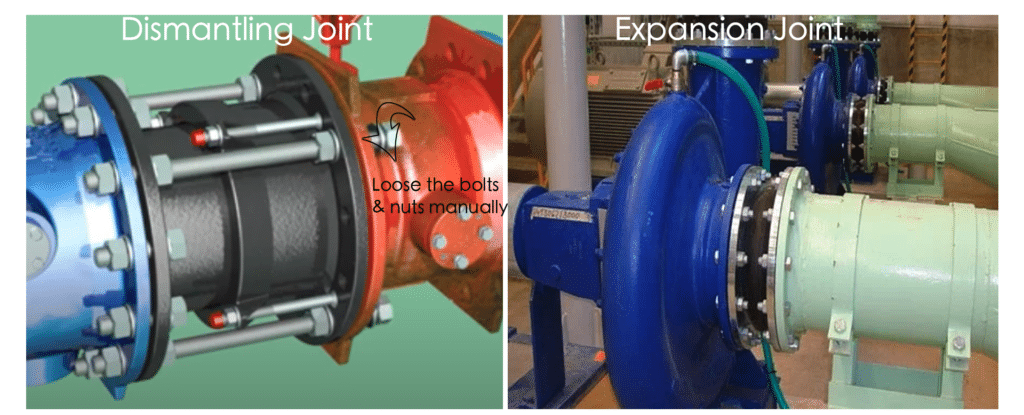
Photos are from google,for instruction only
Difference Between Dismantling Joint and Flange Adapter
Dismantling joints and flange adaptors serve distinct purposes in piping systems. Dismantling joints provide longitudinal adjustment and restraint, facilitating installation and maintenance, making them ideal for systems needing frequent adjustments. Flange adaptors offer a simple, fixed connection between plain-ended pipes and flanged components(like valves, meters etc), suitable for stable, less dynamic applications.
Some user want to know if they can use flange adaptor to replace dismantling joint. but please note the following differences between them
1,The dismantling joint with flange ends and long tie rods go through the whole body , can transfer the axial thrust from the pipe to the entire pipeline.Flange adaptor is one flange end and one flexible socket ends. it is a flexible joint, need to bear the axial thrust in the pipeline.
2,Dismantling joint is rigid connection, no deflection is allowed,flange adaptor is a flexible connection that allows a deflection angle at the socket ends .
As a professional manufacturer of dismantling joint and flange adaptor, we recommend not to use flange adaptor instead of dismantling joint because they are designed for their specific function.