Back to Valves>Gate valves
Knife Gate Valve Manufacturer
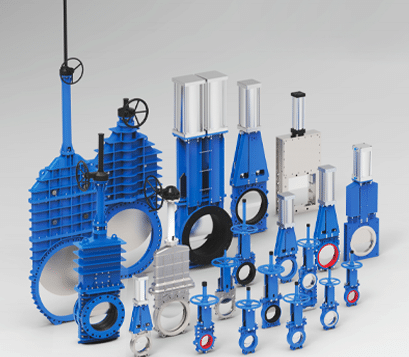
Knife gate valve is a type of valve designed with a knife-shaped gate for cutting off flow.
Unlike traditional gate valves, the gate in a knife gate valve is capable of cutting through particles, fibers, and solid impurities present in the medium and the knife gate valve can be self-cleaning . This makes it suitable for applications such as coal washing, mining, steel, slurry, pulp, and other processes where impurities need to be cut without compromising the seal of the pipeline.
Additionally, knife gate valves have a compact design, offering advantages of smaller size, lower flow resistance, lighter weight, material savings, and minimal installation space requirements compared to traditional gate valves.
As a leading China-based knife gate valve supplier, Judberd boasts a dedicated R&D team capable of designing the most suitable knife gate valve tailored to your specific needs.
Below are some of our existing knife gate valve styles. Feel free to inquire
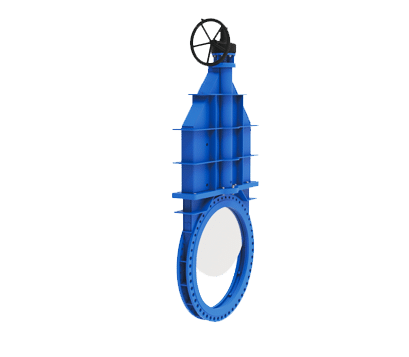
Unidirectional seal NRS bonneted knife gate valve
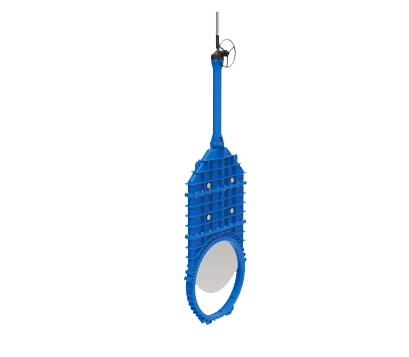
Unidirectional High-Pressure Knife Gate Valve with No Middle Filling, Fully Closed
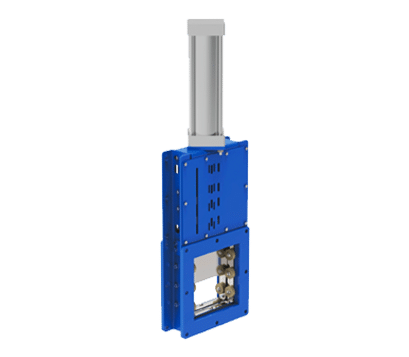
Unidirectional sealing full enclosed square knife gate valve
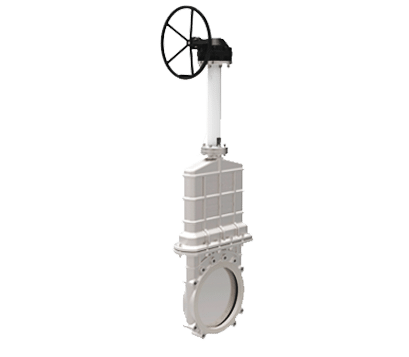
Unidirectional High-Pressure Knife Gate Valve with Middle Filling, Fully Closed
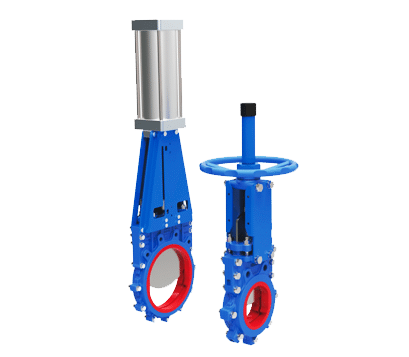
Bi-directional Seal Split-type Wear-resistant Knife Gate Valve
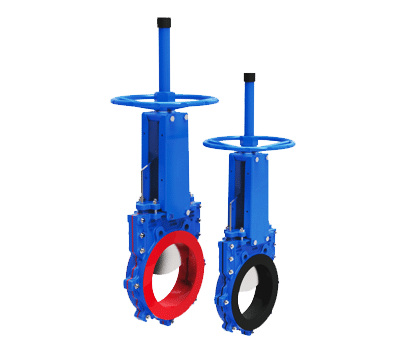
Bi-directional Seal Split-type Rubber lined Knife Gate Valve
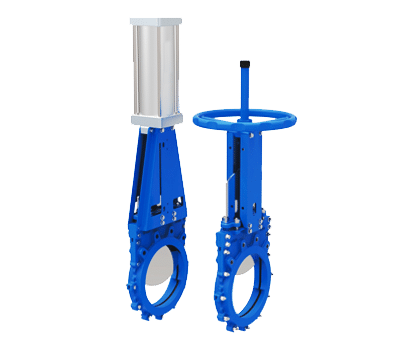
Bi-directional Seal Split-type high pressure Knife Gate Valve
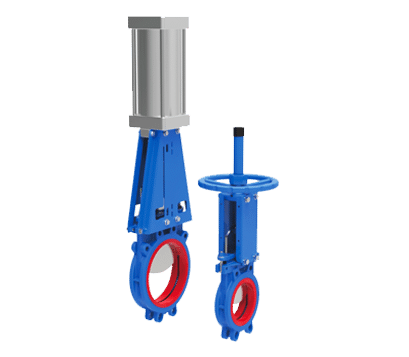
Bi directional sealing wear-resistant knife gate valve for mine
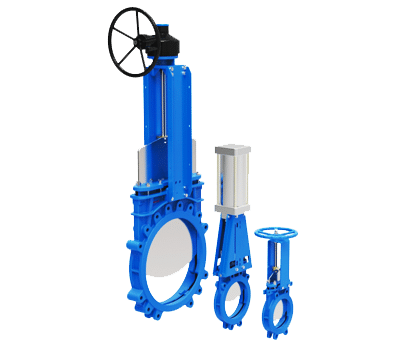
Bi directional sealing knife gate valve
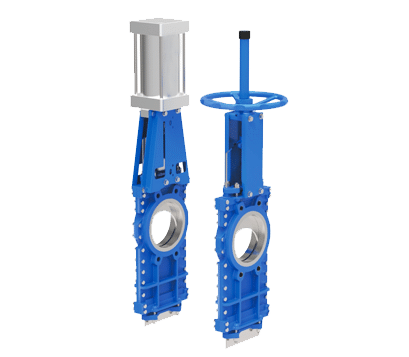
Bi Directional Sealing Through Going Knife Gate Valve
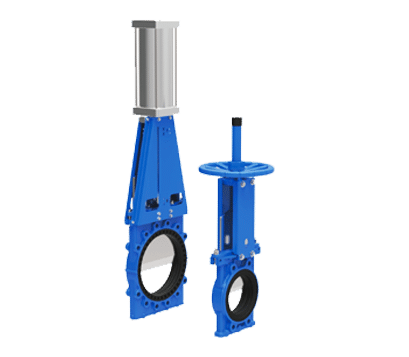
Bi Directional Self Sealing Knife Gate Valve

Bi Directional Knife Gate Valve
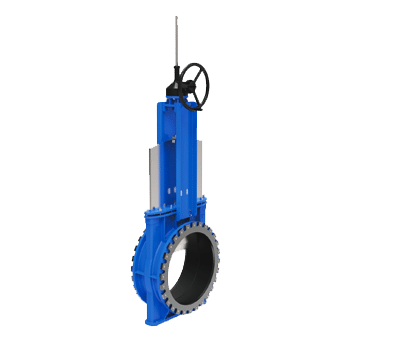
Bi Directional Self Sealing Lug Slurry Knife Gate Valve
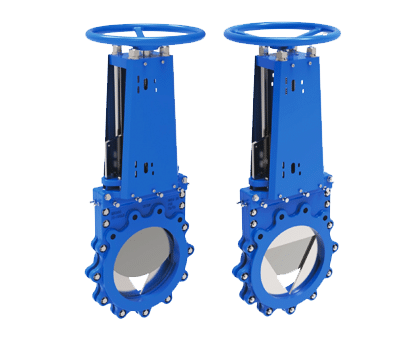
Isogate v port bi directional knife gate valve
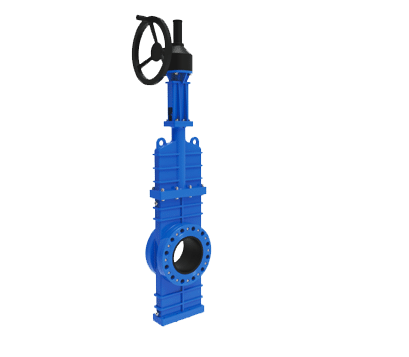
Resilient Seated Bidirectional High Pressure Bonneted Flanged Knife Gate Valve for Abrasive Application
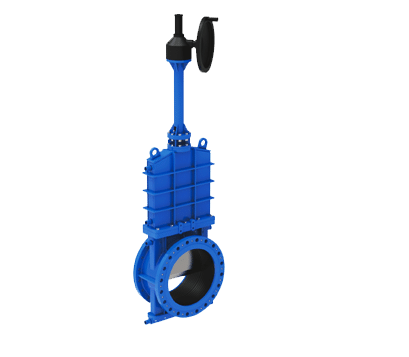
Resilient Seated Bidirectional High Pressure Bonneted Flanged Gear Operated Rising Stem Knife Gate Valve for Abrasive Application
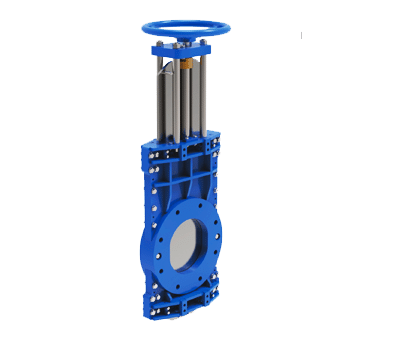
Bi Directional Sealing Through Going Manual Wafer Knife Gate Valve
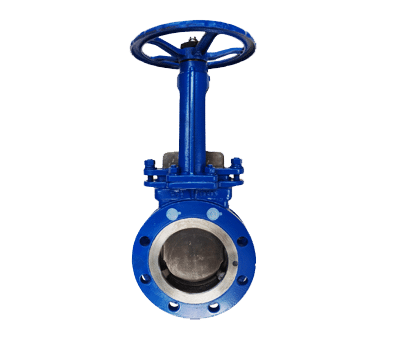
OS&Y Unidirectional Soft Seal Carbon Steel Knife Gate Valve
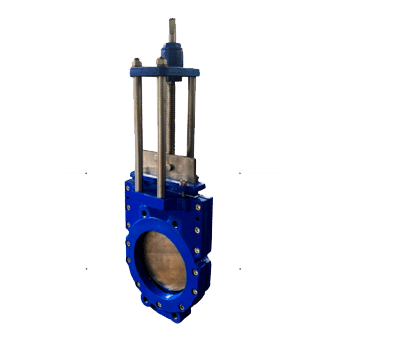
NRS/OS&Y Bidirectional Knife Gate Valve for Water
Knife Gate Valve Parts
A Knife Gate Valve is a common type of valve used for controlling the flow of fluids or powders. It has a relatively simple structure and consists of several main components:
- Valve Body: Typically a metal or alloy plate with fluid passages, made from various materials to suit different working conditions and media.
- Gate: This is the crucial component of the knife gate valve. It resembles a flat blade that can slide vertically within the fluid passage to open or close the valve. Gates are usually made of metal or polymer, with some featuring liners to prevent corrosion and wear.
- Actuator: Used to control the opening and closing of the gate. It can be a manual handwheel, lever, or electric/pneumatic actuator, depending on the application and requirements.
- Sealing Mechanism: Ensures a tight seal between the gate and the valve seat to prevent fluid leakage. Sealing is typically achieved through the compression between the gate and the valve seat.
The working principle of a knife gate valve involves moving the gate to control fluid flow. When the gate moves downward and tightly seals against the valve seat, the valve is in the closed position, blocking fluid passage. Conversely, when the gate moves upward and away from the seat, the valve is in the open position, allowing fluid to pass through.
Knife gate valves are commonly used in applications that require rapid shut-off of fluid flow, especially when dealing with materials like dust, sewage, slurry, and more. They find widespread use in industries such as wastewater treatment, dredging, mining, and chemical processing. Due to their simple structure and reliable shut-off capabilities, knife gate valves are also employed as emergency shut-off valves in certain situations.
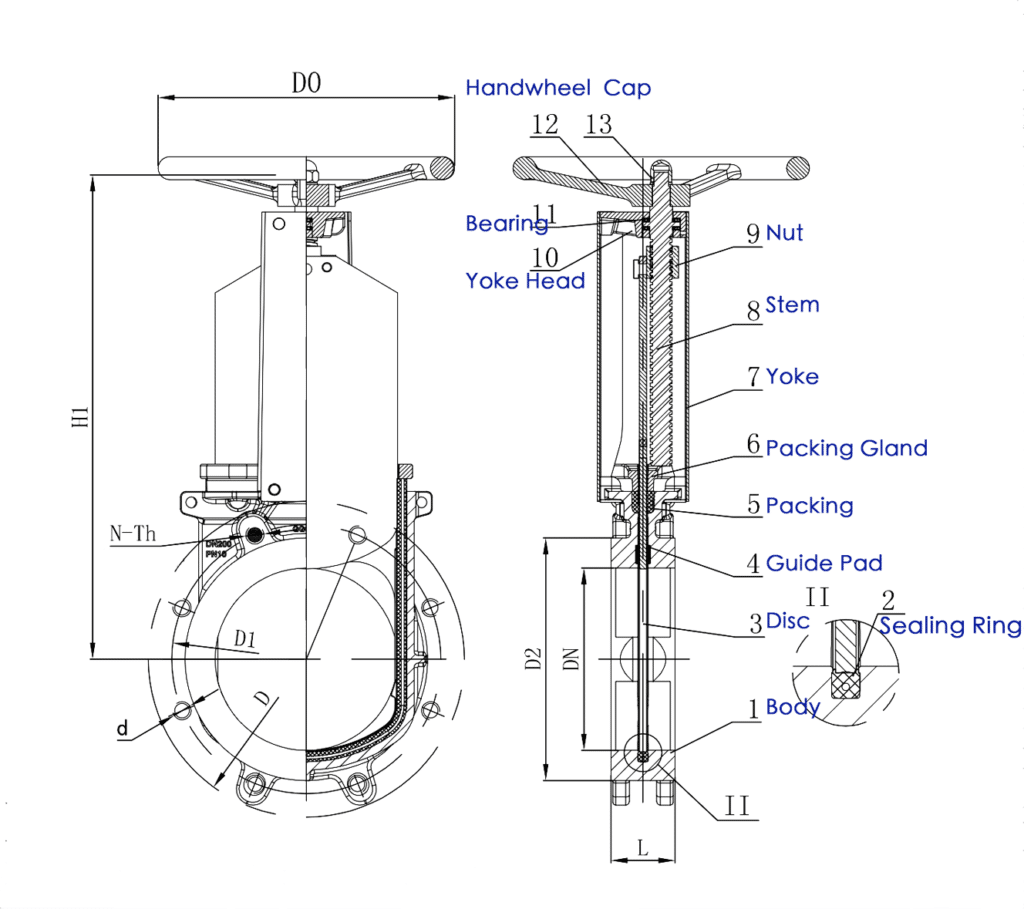
Knife Gate Valve Material
The common materials for the body and bonnet of knife gate valves are:
- Cast iron
- Carbon steel
- Stainless steel
- Brass
- PVC
Among these, cast iron and carbon steel are the most common.
The valve disc and stem are typically made of stainless steel, while the seals can be NBR, EPDM, PTFE, FKM, Graphite, or metal.
Reference the right diagram for clarity
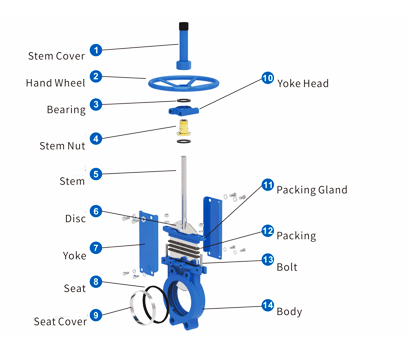
Knife Gate Valve Sealing
Knife gate valve sealing include resilient seated and metal seated ,Bidirectional and unidirectional
Resilient seated vs metal seated knife gate valve
Metal seated knife gate valves achieve sealing between metal surfaces. Both the sealing ball and seat of hard-sealed knife gate valves are made of metal materials, requiring high precision in manufacturing and having a higher level of technical difficulty. They are typically used in high-pressure applications of 35 MPa or higher. On the other hand, resilient seated knife gate valves achieve sealing between metal and non-metal surfaces. The precision of the sealing surfaces does not need to be very high, making it relatively easy to implement.
Metal seated knife gate valves can be used in high-temperature and high-pressure conditions, while soft-sealed ones cannot. Metal seated valves are suitable for corrosive media, whereas soft-sealed ones are not suitable for media that can corrode the sealing materials.
Therefore, when deciding between metal seated or resilient seated knife gate valves, factors such as the process, medium, temperature, pressure, and other conditions should be taken into account. Generally, metal seated knife gate valves are chosen when the sealing medium contains solid particles, granules, has a pressure greater than 35 MPa, a temperature higher than 200 degrees Celsius, or when the medium can corrode the sealing surfaces of resilient seated knife gate valves.
Bidirectional vs unidirectional knife gate valve
A unidirectional sealing knife gate valve is one where the gate of the valve, when closed, must face the direction of the medium flow. The medium flows in only one direction, and there should be an arrow on the valve body indicating the direction of medium flow. When installing, attention should be paid to the direction of medium flow.
A bidirectional sealing knife gate valve is one where the gate can face either towards or away from the direction of medium flow, and there is no need to consider the direction of medium flow during installation. There are no arrows on the valve body indicating the direction of medium flow.
The stem of a bidirectional sealing knife gate valve experiences greater force compared to the stem of a unidirectional sealing knife gate valve. For knife gate valves with the same diameter and pressure rating, the stem diameter of a bidirectional sealing knife gate valve is larger than that of a unidirectional sealing knife gate valve
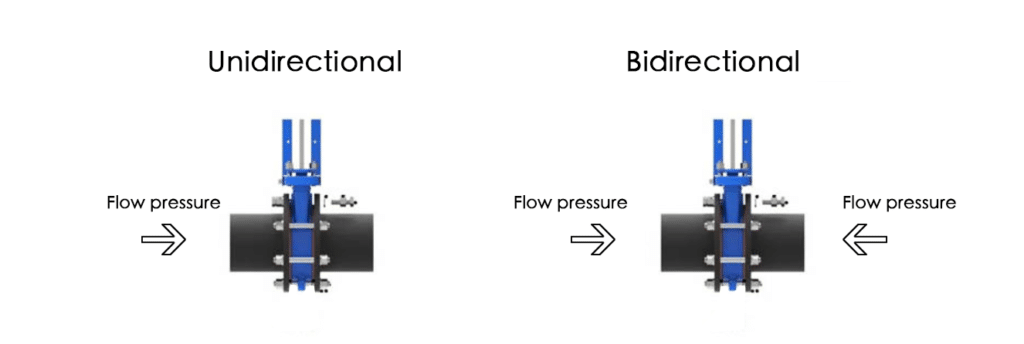
Knife Gate Valve Operation
The operating methods of knife gate valves can be categorized as follows:
- Manual Operation: Manual operation is the most common method for operating knife gate valves. It involves manually rotating or pushing/pulling the valve stem using devices like handles, gears, or threaded rods to open or close the valve disc. Manual operation is suitable for small knife gate valves or situations requiring manual control.
- Electric actuated : Electric operation uses an electric actuator to control the opening and closing of knife gate valves. An electric actuator typically comprises an electric motor, reducer, and control system. It controls the movement of the valve stem by rotating the electric motor in response to electrical signals. Electric operation is suitable for situations requiring remote or automated control.
- Pneumatic actuated: Pneumatic operation employs a pneumatic actuator to control the opening and closing of knife gate valves. A pneumatic actuator usually consists of a cylinder, pneumatic control valve, and a source of compressed air. It controls the actuator’s operation by regulating the opening and closing of the pneumatic control valve with compressed air pressure, thereby moving the valve stem to open or close the valve disc. Pneumatic operation is suitable for situations requiring remote or automated control and demanding higher power output.
It’s essential to note that the choice of the operating method for knife gate valves may vary based on specific application needs and system requirements. For instance, in certain specialized industrial applications, knife gate valves may integrate with other control devices, such as pneumatic actuators or turbine operators, to achieve more precise control or fulfill complex operational requirements.
When selecting the operating method, factors such as safety, level of automation, control precision, cost, and reliability should be considered based on the actual circumstances. Ensure that the chosen operating method aligns with the system requirements and process needs.
Knife Gate Valve Connection
Welded Connection:
When the nominal diameter is relatively large, and temperatures are elevated, the valve body is typically connected by welding with a beveled end. Strict requirements are placed on the welded joints, necessitating the use of highly skilled welding techniques to complete this work.
Flange Connection:
Valves with flange connections are relatively easy to install and disassemble, making them quite common.
Threaded Connection:
Threaded connections are primarily used for valves with nominal sizes smaller than 50 millimeters
Knife Gate Valve Working Principle
The working principle of a knife gate valve can be briefly described as follows:
By rotating the blade, it achieves the function of opening and closing the valve. In the closed position, the blade is inside the valve body, creating a blockage that prevents the flow of the medium. In the open position, the blade rotates away from the valve body, allowing the medium to flow freely.
The opening and closing function of a knife gate valve primarily relies on the following key components:
- Blade:The blade is one of the critical components of the knife gate valve, determining the valve’s open and closed state. Blades are typically made of sturdy metal materials with corrosion resistance and high-temperature resistance. When the blade rotates to the closed position, it tightly fits against the valve seat, ensuring a good sealing performance.
- Valve Body:The valve body is the supporting and fixed component of the knife gate valve, providing the motion track for the blade. Valve bodies are usually made of materials like cast iron, carbon steel, or stainless steel, providing sufficient strength and rigidity. The blade connects to the valve body’s bearings and guiding devices to achieve rotational movement.
- Handle or Actuator :The handle or actuator is the operating component of the knife gate valve used to control the opening and closing of the blade. The handle is typically located on one side of the valve body and, through the actuator connected to the blade, enables manual ,electric or pneumatic opening and closing operations. The actuator can be a handwheel, an electric motor, or a hydraulic device, depending on the specific application requirements.
knife gate valve Advantages and Disadvantages
Advantages:
- Knife gate valves have a simple structure, allowing for quick valve opening and closing, with the ability to effectively control and shut off the flow of the medium.
- They offer good sealing performance, with sealing gaskets made of metal or elastic materials to prevent medium leakage effectively.
- These valves exhibit excellent wear resistance, as their sealing surfaces are made of hard materials, suitable for high-speed flow, high viscosity, and media with particles.
- They are compact, lightweight, easy to install, and maintain, with straightforward operation.
Disadvantages:
- Knife gate valves can produce some impact noise and vibrations during operation, potentially affecting pipelines and equipment. produce some impact noise and vibrations during operation,
- Opening and closing a knife gate valve require relatively large force and space, necessitating consideration of structural and spatial constraints in pipelines and equipment.
- Their fluid characteristics are not optimal, making them susceptible to medium blockages and leaks.
In summary, knife gate valves offer advantages such as simplicity, good sealing, and wear resistance, but they also have drawbacks like impact during operation and space constraints. Therefore, when selecting a knife gate valve, it’s important to consider its characteristics, the working environment, and pipeline conditions to make a rational choice and use it effectively.
How to choose right knife gate valve?
Knife gate valves can accommodate changes in the medium but require different measures and considerations depending on the specific medium and operating conditions. Here are some suggestions on how knife gate valves can adapt to changes in the medium:
- Material Selection: Choose appropriate valve materials based on the properties of the medium. Different media may have varying material requirements; for instance, corrosive media may require corrosion-resistant materials, while high-temperature media may necessitate high-temperature alloy materials.
- Regular Inspection and Maintenance: For knife gate valves handling different media, regular inspection and maintenance are crucial. This includes cleaning the valve internals, checking the condition of seals, ensuring the normal operation of components, and establishing maintenance schedules based on the medium’s characteristics and usage frequency.
- Seat and Blade Material Selection: In applications involving solid particles or abrasive media, select seat and blade materials with high wear resistance to extend the valve’s lifespan.
- Consider Sealing Performance: Sealing performance requirements may vary for different media. For leak-prone media, choose knife gate valves with excellent sealing performance and ensure the seals are in good condition.
- Flow Control: Flow control may be essential for certain media, especially liquids. In such cases, consider the flow regulation capability of the knife gate valve and potentially incorporate additional flow control devices.
- Medium Temperature and Pressure: Different media may have varying temperature and pressure requirements. Ensure that the valve’s materials and design are suitable for the working temperature and pressure range of the medium.
- Follow Manufacturer Recommendations: Manufacturers typically provide guidance on the suitability and maintenance of knife gate valves for different media. Always adhere to the manufacturer‘s guidelines and recommendations to ensure safe valve operation with different media.
In conclusion, knife gate valves can adapt to changes in the medium, but it’s essential to consider the characteristics and requirements of the specific medium during selection, installation, and maintenance. Take appropriate preventive and maintenance measures based on the specific application and medium to ensure the performance and reliability of knife gate valves.
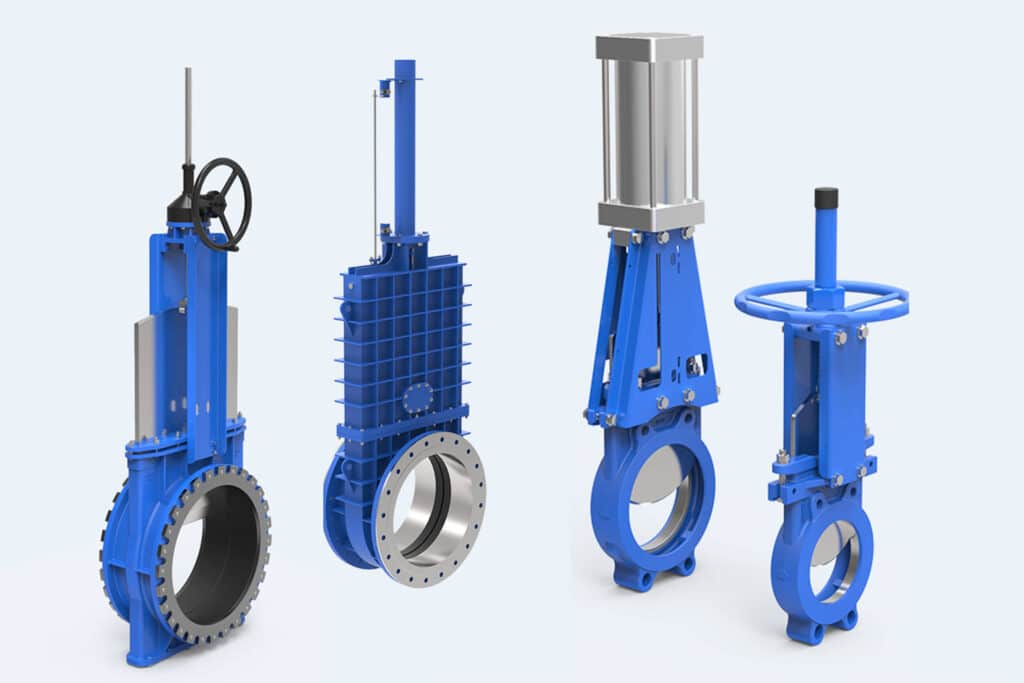
Knife Gate Valve Use
Knife gate valves find extensive applications in various specialized industries, including:
- Wastewater Treatment Industry: Knife gate valves are commonly used in sewage treatment plants to control the flow and processing of wastewater, including units like sedimentation tanks, filters, and reaction tanks.
- Paper and Pulp Industry: They are employed in paper and pulp production to regulate the flow and processing of media, as well as in pulp transport.
- Mining and Ore Processing: In mining and ore processing, knife gate valves are used to control the flow of ore and ore slurry containing solid particles.
- Power Plants: Knife gate valves are used in power plants to control water flow, especially in thermal power plants and hydroelectric power plants.
- Chemical Industry: They are used in chemical production to control the flow of various chemical media, including liquids, gases, and solids.
- Food and Beverage Industry: Knife gate valves are used in food and beverage processing to control the flow of raw materials and processing media.
- Steel Manufacturing: In the steel manufacturing process, they are used to control the flow of liquids in processes like blast furnaces, steelmaking furnaces, and other equipment.
- Shipbuilding: In shipbuilding and ship maintenance, knife gate valves are used to control water flow within ship compartments.
- Marine Engineering: They play a role in controlling the flow of seawater in marine engineering applications, such as seawater treatment and maintenance of offshore platforms.
- Oil and Gas Industry: Knife gate valves are used in the oil and gas industry for controlling the flow of media during extraction, transportation, and processing.
- Specialized Equipment Manufacturing: Some specialized equipment manufacturing industries, such as nuclear equipment and aerospace, also use knife gate valves for fluid control.
In summary, knife gate valves play a crucial role in specialized industries where controlling the flow of media is essential. Their design makes them suitable for handling various types of media, including solid particles, high temperatures, high pressures, and corrosive substances. Therefore, in these industries, knife gate valves are indispensable fluid control devices.
Knife Gate Valve Installation
- Before installation, inspect the valve chamber, sealing surfaces, and other parts; ensure there are no contaminants or particles adhering.
- Tighten all bolt connections evenly.
- Ensure that the packing is properly compressed, ensuring both sealing and smooth operation of the gate.
- Prior to valve installation, verify the valve model, connection dimensions, and pay attention to the flow direction of the medium to ensure compliance with valve requirements.
- Provide necessary space for valve actuation during valve installation.
- Follow the wiring diagram for the connection of the actuator.
- Regularly maintain knife gate valves and avoid any random impacts or compressions to prevent compromising the sealing.
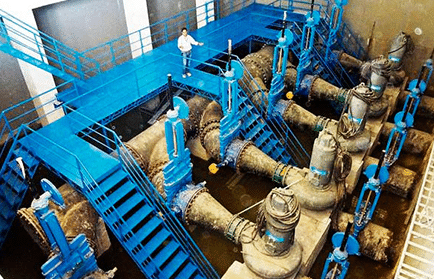