Steel Flange
Steel flange is a ring or plate made of steel, used to connect pipes, valves, pumps, or other equipment in a pipeline system. It helps you make a strong, leak-proof connection, so you can easily put things together, take them apart, and fix them. People usually bolt flanges together and put gaskets between them to make sure they don’t leak.
Judberd is china manufacturer for many different types of steel flanges, Include but not limit to below types.
Production Process
1,Raw material inspection 2,Cutting the material 3,Forging the rough 4,Normalizing 5,Inspection rough 6,Machining 7,Inspection dimension 8,Drilling 9,Drilling quality inspection 10,Marking 11, surface coating 12, package
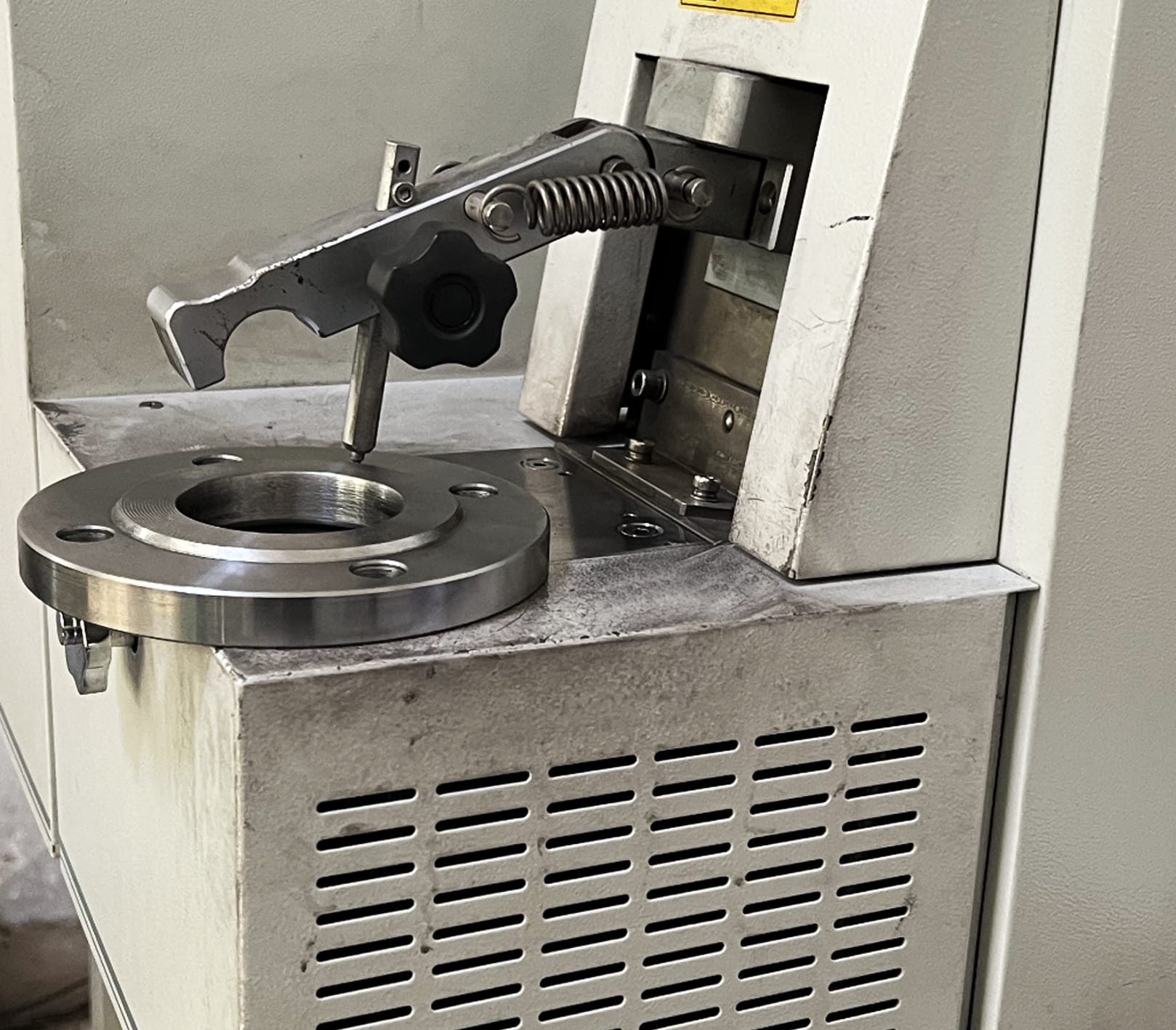
Chemical Composition Testing
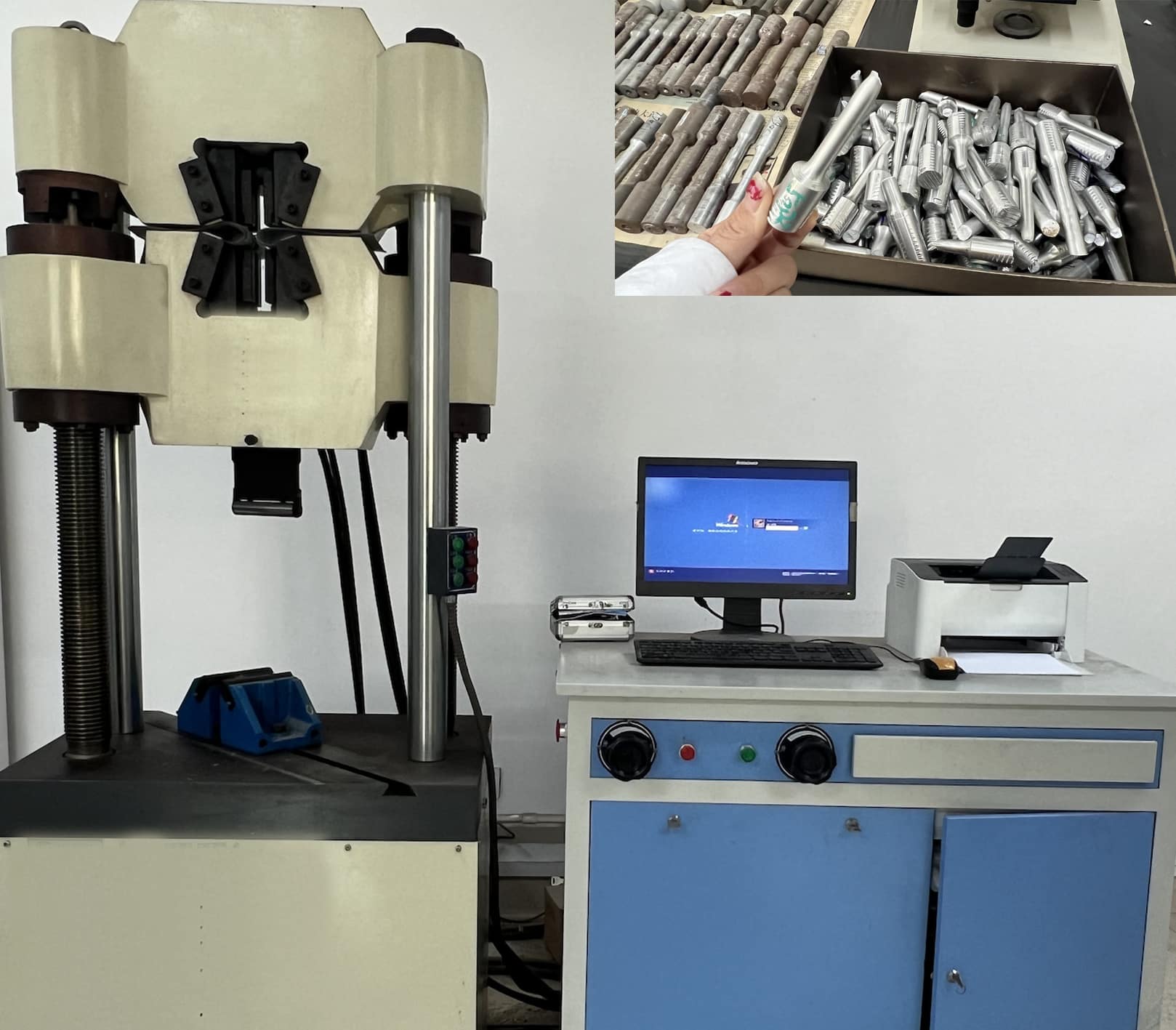
Inspection for Tensile Strength, Yield Strength, Elongation After Fracture, Reduction of Area
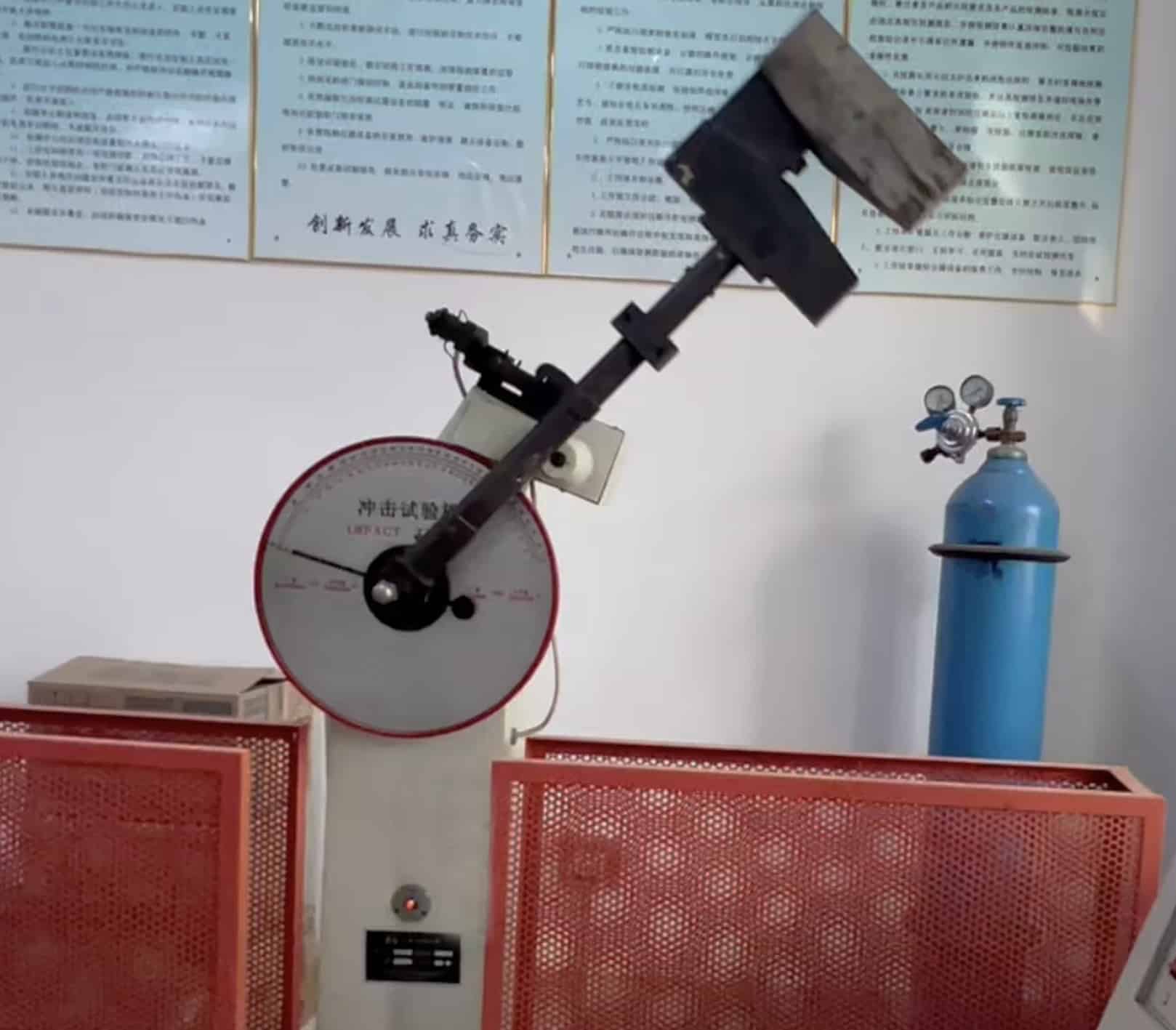
Impact Test
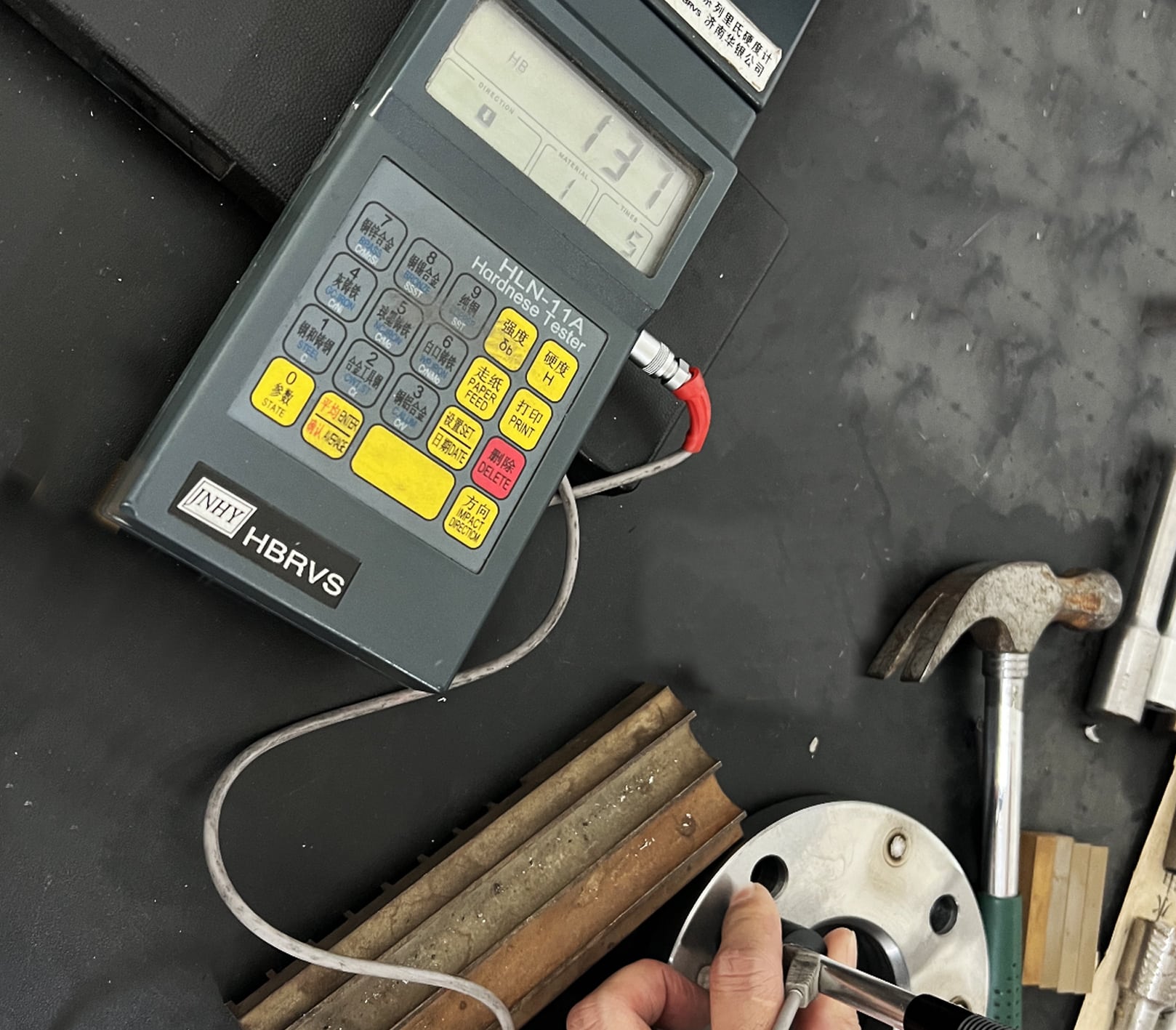
Hardness Inspection
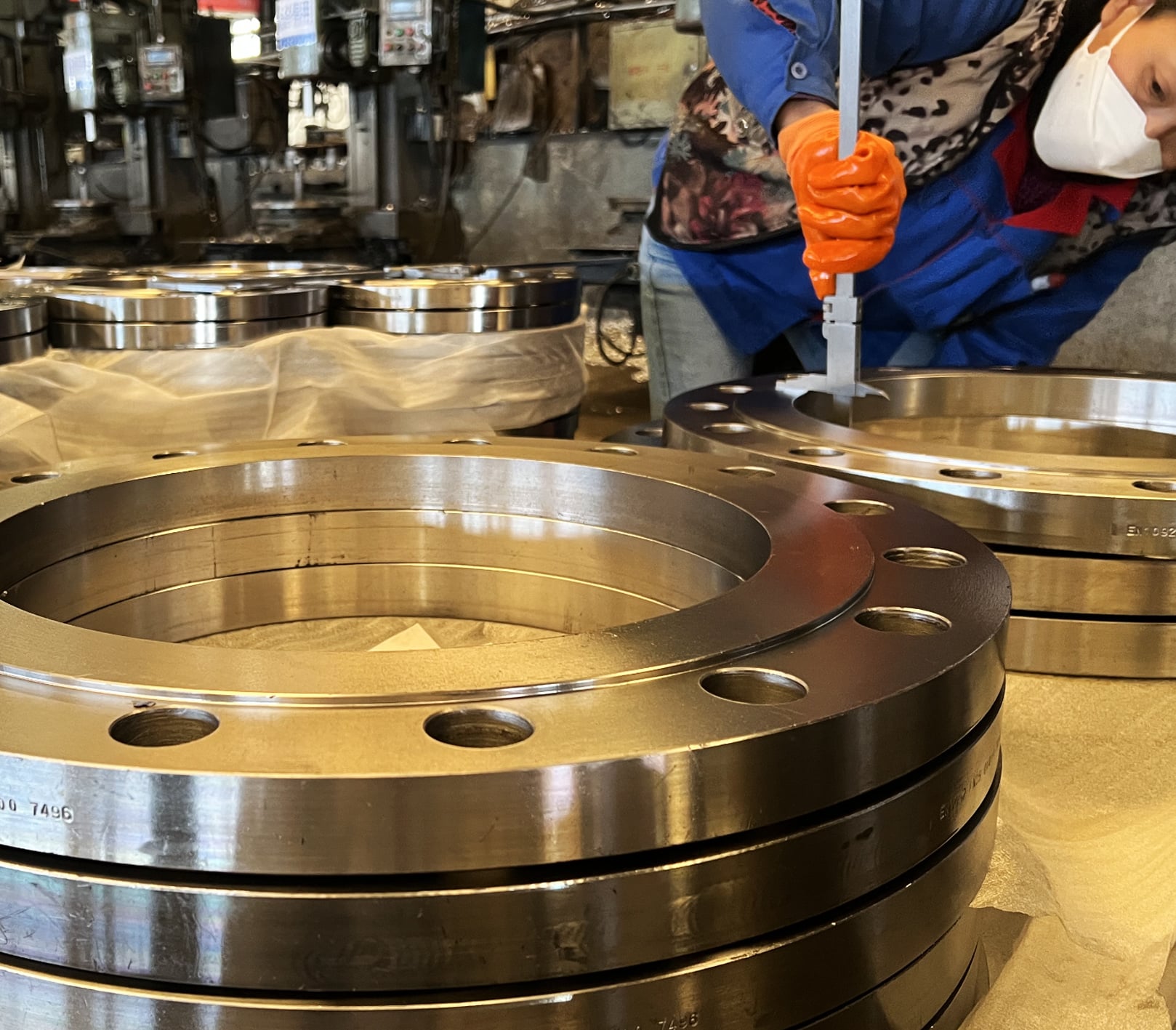
Dimension Inspection
Types
Steel flange include Weld Neck Flange (WN),Slip-On Flange (SO),Blind Flange (BL),Socket Weld Flange (SW),Threaded Flange (TH),Lap Joint Flange (LJ),Orifice Flange etc.
The three most common steel flanges are:
Weld Neck Flange (WN):This flange is used in high-pressure and high-temperature pipeline systems because it is strong and durable.
Slip-On Flange (SO):This flange is used in medium and low-pressure water, oil, and gas pipeline systems because it is easy to install and costs less.
Blind Flange (BL):This flange is used to seal the end of a pipeline or block the flow of fluid in various pipeline systems.
These three flanges are the most versatile because they can be used for many different things and in many different ways.
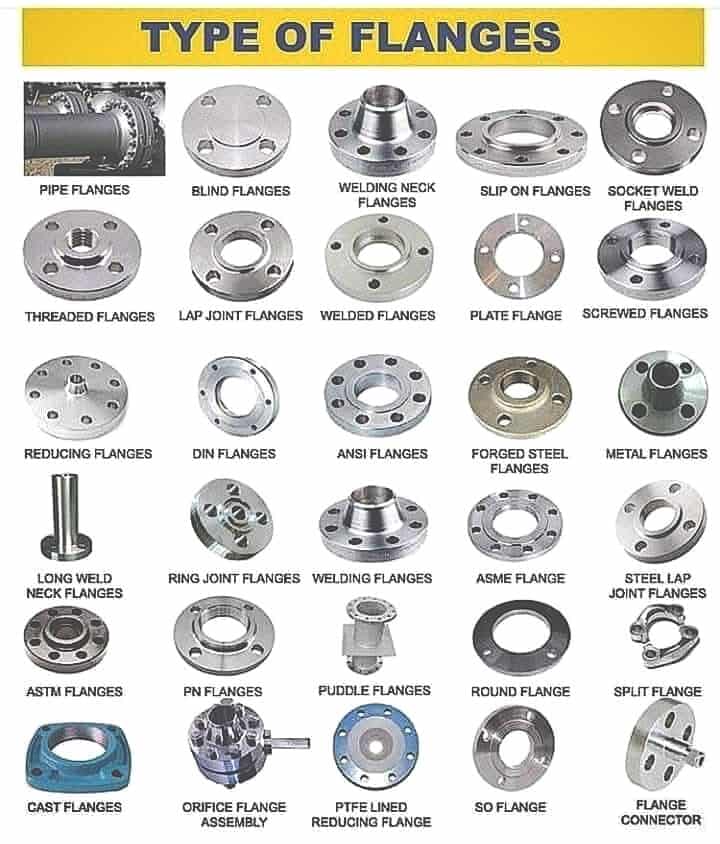
Flange Material and Their difference
Carbon Steel (CS) :Made from iron and carbon, carbon steel is strong and durable.It is the most cost-effective material for general use.It can corrode when exposed to moisture or chemicals.Common Types:Q235B and ASTM A105 (standard for carbon steel flanges).Used in low to medium-pressure pipelines, such as water, gas, and oil pipelines.Typically used in non-corrosive or mildly corrosive environments.
Stainless Steel (SS):Contains chromium, making it resistant to corrosion, staining, and rust.It is strong, durable, and can handle heat.It is more expensive than carbon steel.Common Types:SS304, SS316, SS316L, etc.Used in pipelines that deal with corrosive or high-temperature environments, such as marine, chemical, and food industries.Good for oil and gas pipelines, especially those that deal with aggressive media like seawater or chemicals.
Alloy Steel:Made from a combination of carbon steel and other elements like nickel, chromium, and molybdenum.It is stronger, tougher, and can resist corrosion and high temperatures.It is generally more expensive than carbon steel.Common Types:ASTM A182 (for forged alloy steel flanges).Used in high-pressure and high-temperature pipelines, such as power plants, refineries, and petrochemical industries.Good for aggressive environments where you need strength and resistance to thermal expansion.
Ductile Iron (DI):A form of cast iron that is stronger and more flexible because of its graphite content.It is good at resisting wear, fatigue, and shock loading.It is less expensive than stainless steel and alloy steel but more expensive than carbon steel.Common Types:GGG40,GGG50,ASTM A536 (for ductile iron flanges).Used in water and sewage systems, as well as fire protection pipelines.Preferred in applications where you need high wear resistance, such as waste treatment plants.
Copper Alloy (Brass or Bronze):Highly resistant to corrosion, especially in seawater.It has excellent electrical and thermal conductivity.It is more expensive than carbon steel.Common Types:ASTM B62 (for bronze flanges).Typically used in specialized applications, such as marine pipelines, heat exchangers, and industrial cooling systems where you need corrosion resistance.
Summary of Differences:
Carbon Steel: Cheap and used in low to medium pressure systems, can corrode.
Stainless Steel: Resistant to corrosion, used in high-temperature and corrosive environments, more expensive.
Alloy Steel: Stronger and can resist heat and pressure, used in high-demand industrial systems.
Ductile Iron: Stronger than regular cast iron, used in water and sewage systems, resists wear.
Copper Alloy: Excellent corrosion resistance, used in specialized marine and heat exchange systems.
You choose the material based on the environment you are putting it in, considering pressure, temperature, and corrosion resistance.
Flange Pressure
The pressure that steel flanges can withstand is closely related to their material, size, design specifications, and operating environment. Here are the key factors that affect the pressure-bearing capacity of steel flanges and the relationship between size and pressure:
1, Key Factors Affecting Flange Pressure-Bearing Capacity
Flange Material:Different materials have different pressure resistance. Common materials include carbon steel, stainless steel, and alloy steel,Carbon Steel Suitable for low to medium pressure applications.Stainless Steel Offers higher pressure resistance and better corrosion resistance, ideal for harsh environments.Alloy Steel: Designed for high-temperature, high-pressure, and specialized medium conditions.
Pressure Rating:The pressure-bearing capacity of a flange is typically classified by standards such as ANSI/ASME B16.5 into ratings like 150, 300, 600, 900, 1500, and 2500 pounds. Higher pressure ratings correspond to greater pressure capacity.
Temperature and Medium:Higher temperatures reduce a flange’s pressure capacity. Certain media, such as corrosive gases or liquids, can also impact flange performance.
2, Relationship Between Flange Size and Pressure-Bearing Capacity
The impact of flange size (e.g., diameter, thickness, and bolt hole count) on pressure-bearing capacity is reflected in the following aspects:
Flange Diameter:A larger sealing surface diameter (the gasket contact area) allows for more uniform pressure distribution, enhancing overall pressure capacity.However, excessively large diameters increase the stress area, raising the risk of deformation.
Flange Thickness:Thickness is a key determinant of pressure capacity. Greater thickness improves resistance to bending and shear stress.
Number and Size of Bolt Holes:More and larger bolt holes help distribute stress more effectively, improving sealing performance and pressure capacity.
Flange Sealing Surface Type:Common sealing surfaces include flat face, raised face, and ring joint face (RTJ). Ring joint faces are ideal for high-pressure applications due to their superior sealing reliability.You can find the difference between flat face and raised face as below
Flat face flange VS Raised face flange
3. Methods for Calculating the Relationship Between Size and Pressure
The relationship between flange size and pressure can be determined using design standards or empirical formulas, such as the pressure-temperature rating curves provided in ASME B16.5. Key parameters for calculation include:
Inner Diameter (D): Defines the flow area and determines the required flow and flange size.
Wall Thickness (t): Minimum thickness is determined by material strength and working pressure.
Operating Pressure (P): Defines the maximum pressure for designing flange parameters.
Empirical Formula:
t=2⋅(S⋅E−P)P⋅D
Where:t: Flange thickness,P: Operating pressure,D: Flange inner diameter,S: Allowable stress of the material,E: Weld efficiency (if welding is present)
4. Practical Applications of Size and Pressure
Small Diameter Flanges (e.g., DN50 and below): Typically designed with thin walls, suitable for low or medium-pressure pipeline systems.
Medium to Large Diameter Flanges (e.g., DN200 and above): To withstand high pressures, these flanges require increased thickness, more bolt holes, and high-strength materials.
Examples:
ANSI Class 150 flanges are generally suitable for pressures up to 1.6 MPa (approximately 16 bar) at 25°C.
ANSI Class 600 flanges can withstand pressures of around 10 MPa (approximately 100 bar) at 25°C.
Conclusion
The pressure capacity of a flange is determined by its material, pressure rating, and operating conditions. Flange size (e.g., thickness, diameter, and bolt holes) is designed to meet specific pressure requirements. Engineering practices rely on standard guidelines and calculation formulas to select appropriate sizes and materials, ensuring safe operation under specified conditions.
International Design Standards for Steel Flanges
ANSI/ASME B16.5
Country/Region: USA, globally recognized
Applications: Oil & gas, petrochemicals, water pipelines
Covers pressure ratings Class 150 to 2500 for pipe flanges and flanged fittings.
EN 1092-1
Country/Region: Europe
Applications: Water supply, chemical industries, general engineering
European standard for steel flanges, widely used in EU countries.
JIS B2220
Country/Region: Japan
Applications: Industrial pipelines, shipbuilding, manufacturing
Japanese flange standard with pressure classes from 5K to 63K.
DIN Standards (e.g., DIN 2501)
Country/Region: Germany, Europe
Applications: Waterworks, machinery, chemical plants
Predecessor of EN 1092-1, still used in older European systems.
BS 4504
Country/Region: United Kingdom
Applications: Water and gas pipelines, industrial equipment
British standard for flanges, now replaced by EN 1092-1 but still in use.
GOST 12820-80
Country/Region: Russia, CIS countries
Applications: Oil & gas, energy, industrial pipelines
Russian standard for steel flanges with various pressure and temperature ranges.
ISO 7005-1
Country/Region: International
Applications: General industries, export products
Provides a unified global flange standard compatible with EN and ASME.
AS 2129
Country/Region: Australia, New Zealand
Applications: Water systems, mining, engineering projects
Australian flange standard with multiple pressure classifications.
GB/T 9112-2010
Country/Region: China
Applications: Domestic pipelines, industrial equipment
Chinese national standard for steel flanges, covering various pressure ratings.
Summary of Applications
Oil & Gas: ANSI/ASME B16.5, GOST 12820-80
Water Supply: EN 1092-1, BS 4504, AS 2129
Industrial Pipelines: JIS B2220, DIN, GB/T 9112-2010
Export Markets: ISO 7005-1 for compatibility across multiple regions.
Installation
Below are step-by-step instructions for installing each type of carbon steel flange.
Weld Neck Flange (WN)
Tools Required: Welding machine, pipe cutter, measuring tape, alignment tools, and personal protective equipment (PPE).
Steps:
Prepare the Pipe:Cut the pipe end squarely using a pipe cutter.Bevel the pipe end to the correct angle (usually 37.5°) for butt welding.Clean the pipe end to remove any dirt, grease, or paint.
Align the Flange:Slide the Weld Neck Flange onto the pipe until it touches the bevelled edge.Use alignment tools to ensure the flange is centered and square to the pipe.
Tack Weld:Perform a tack weld at four equidistant points around the pipe-flange connection to hold it in place.
Full Weld:Weld the flange to the pipe using the specified welding method (typically arc welding).Weld around the full circumference of the pipe-flange joint.
Inspect the Weld:Inspect the weld for uniformity and absence of defects like cracks or voids.
Finalize Installation:Allow the weld to cool, and proceed with system assembly by bolting the flange to its mating component.
2. Slip-On Flange (SO)
Tools Required: Welding machine, pipe cutter, measuring tape, and alignment tools.
Steps:
Prepare the Pipe:Cut the pipe end squarely.Clean the pipe end to remove contaminants.
Position the Flange:Slide the Slip-On Flange onto the pipe. Ensure the pipe extends slightly beyond the flange face (typically 3-5 mm).
Align the Flange:Center the flange on the pipe and align it using tools or visual inspection.
Tack Weld:Tack weld the pipe to the inner and outer flange faces.
Full Weld:Weld the pipe to the inner bore of the flange and around the outer flange face.
Ensure full penetration of the weld for a secure connection.
Inspect the Weld:Check for uniform welds and absence of leaks.
3. Blind Flange (BL)
Tools Required: Bolts, nuts, gasket, torque wrench, and alignment tools.
Steps:
Prepare the Pipe or System:Clean the pipe flange face and ensure it is free from dirt and debris.
Install the Gasket:Place the gasket centrally on the mating flange face.
Position the Blind Flange:Align the Blind Flange with the mating flange.
Insert Bolts:Insert bolts through the flange holes and secure with nuts.
Tighten Bolts:Use a torque wrench to tighten bolts in a crisscross pattern to ensure even pressure.
Final Inspection:Check for proper sealing and ensure no leaks during testing.
4. Socket Weld Flange (SW)
Tools Required: Welding machine, measuring tape, and alignment tools.
Steps:
Prepare the Pipe:Cut the pipe end squarely.Clean the pipe end.
Insert the Pipe into the Flange:Push the pipe into the flange socket until it bottoms out.
Pull the pipe back by about 1.6 mm (1/16 inch) to allow for thermal expansion.
Tack Weld:Tack weld the pipe to the flange.
Full Weld:Apply a fillet weld around the pipe-flange connection.
Inspect the Weld:Ensure the weld is uniform and leak-free.
5. Threaded Flange (TH)Tools Required: Pipe wrench, sealing tape, or thread sealant.
Steps:
Prepare the Pipe:Ensure the pipe has threads matching the flange.Clean the threads on both the pipe and flange.
Apply Sealant:Wrap the pipe threads with sealing tape or apply thread sealant to prevent leaks.
Thread the Flange:Screw the flange onto the pipe by hand.Tighten the flange with a pipe wrench, ensuring it is secure but not overtightened.
6. Lap Joint Flange (LJ)
Tools Required: Stub end, bolts, nuts, gasket, and alignment tools.
Steps:
Prepare the Pipe and Stub End:Weld the stub end to the pipe.
Position the Flange:Slide the Lap Joint Flange onto the pipe before attaching the stub end.
Align the Flange and Stub End:Position the flange over the stub end, aligning the bolt holes.
Insert Gasket and Bolts:Place the gasket between the stub end and the mating flange.Insert bolts and tighten evenly in a crisscross pattern.
7. Orifice Flange
Tools Required: Orifice plate, gasket, bolts, nuts, torque wrench, and alignment tools.
Steps:
Prepare the Pipe:Clean the mating flange surfaces.
Install the Orifice Plate:Position the orifice plate between the Orifice Flanges, ensuring the flow direction is correct (marked on the plate).
Position the Gaskets:Place gaskets on both sides of the orifice plate.
Align the Flanges:Align the flanges and ensure the bolt holes match.
Insert Bolts and Tighten:Insert bolts and tighten them using a torque wrench in a crisscross pattern.
Final Check:
Ensure proper sealing and check for leaks during testing.
General Tips for All Flanges
Always wear appropriate PPE during installation.
Use calibrated tools to ensure accurate assembly.
Follow pressure and temperature ratings specified for the flange.
Conduct pressure tests after installation to verify system integrity.
Common Failures and Maintenance Methods
1. Weld Neck Flange (WN)
Common Failures:
Cracks in the weld joint.
Leakage due to improper welding or thermal stress.
Corrosion at the neck or weld area.
Maintenance:
Inspect weld joints regularly for cracks or defects.
Apply corrosion-resistant coatings or paints.
Use non-destructive testing (e.g., ultrasonic) to assess weld integrity.
2. Slip-On Flange (SO)
Common Failures:
Leakage from the inner or outer weld area.
Misalignment during installation.
Corrosion at the weld or flange face.
Maintenance:
Check alignment and sealing during installation.
Re-weld if cracks or leaks are detected.
Clean and reapply protective coatings to prevent corrosion.
3. Blind Flange (BL)
Common Failures:
Gasket failure causing leaks.
Deformation of the flange due to high pressure.
Corrosion on the sealing face.
Maintenance:
Inspect the gasket and replace it periodically.
Ensure the bolts are evenly tightened.
Clean and re-polish the sealing face if corrosion is detected.
4. Socket Weld Flange (SW)
Common Failures:
Cracks in the fillet weld.
Leakage due to improper welding.
Corrosion inside the socket or weld area.
Maintenance:
Perform visual and non-destructive weld inspections.
Ensure the pipe is correctly positioned before welding.
Clean the inner socket and apply anti-corrosion coatings.
5. Threaded Flange (TH)
Common Failures:
Thread wear or damage causing leaks.
Improper sealing due to poor thread alignment.
Corrosion of threads.
Maintenance:
Apply thread sealant or tape to prevent leaks.
Inspect threads for wear and repair or replace as needed.
Keep threads clean and free from debris.
6. Lap Joint Flange (LJ)
Common Failures:
Misalignment of the flange and stub end.
Wear or deformation of the stub end.
Corrosion at the joint.
Maintenance:
Inspect the stub end and flange alignment regularly.
Replace the stub end if excessive wear is detected.
Clean and apply anti-corrosion treatments to the flange and stub end.
7. Orifice Flange
Common Failures:
Incorrect orientation of the orifice plate causing flow errors.
Leakage around the orifice plate or flange face.
Gasket wear or damage.
Maintenance:
Verify correct installation of the orifice plate.
Inspect and replace gaskets as needed.
Regularly clean the orifice plate to remove debris or buildup.
General Tips for Flange Maintenance
Perform regular inspections for all flange types, focusing on welds, seals, and corrosion.
Ensure proper installation techniques are followed to minimize failures.
Use appropriate materials and coatings for specific operating environments.
Conduct pressure and leak tests periodically to ensure system integrity.