Flexible Grooved Coupling
Flexible grooved coupling is a mechanical connector used to join two grooved-end pipes while allowing a certain degree of flexibility in the connection. It consists of a housing (usually made of ductile iron or steel), a rubber gasket for sealing, and bolts/nuts to secure the connection.
It is designed to provide a leak-proof, mechanical connection between two pipes.Unlike rigid couplings, flexible couplings allow for limited movement: axial displacement (expansion/contraction), angular deflection, and slight pipe misalignment.The internal gasket provides a seal, while the grooved housing grips the pipe ends to hold them together without welding or threading.
Flexible grooved coupling offers the benefits of easier installation, vibration absorption, and thermal movement accommodation. It is best used in systems where pipe movement is expected. In contrast, a rigid grooved coupling is used when a firm, immovable connection is needed, such as in vertical risers or load-bearing lines.

Judberd have 9 types flexible grooved coupling as below according to different working pressure systems.
Ductile Iron Flexible Coupling(Working Pressure 5 Mpa for small size, 3 Mpa for big size)
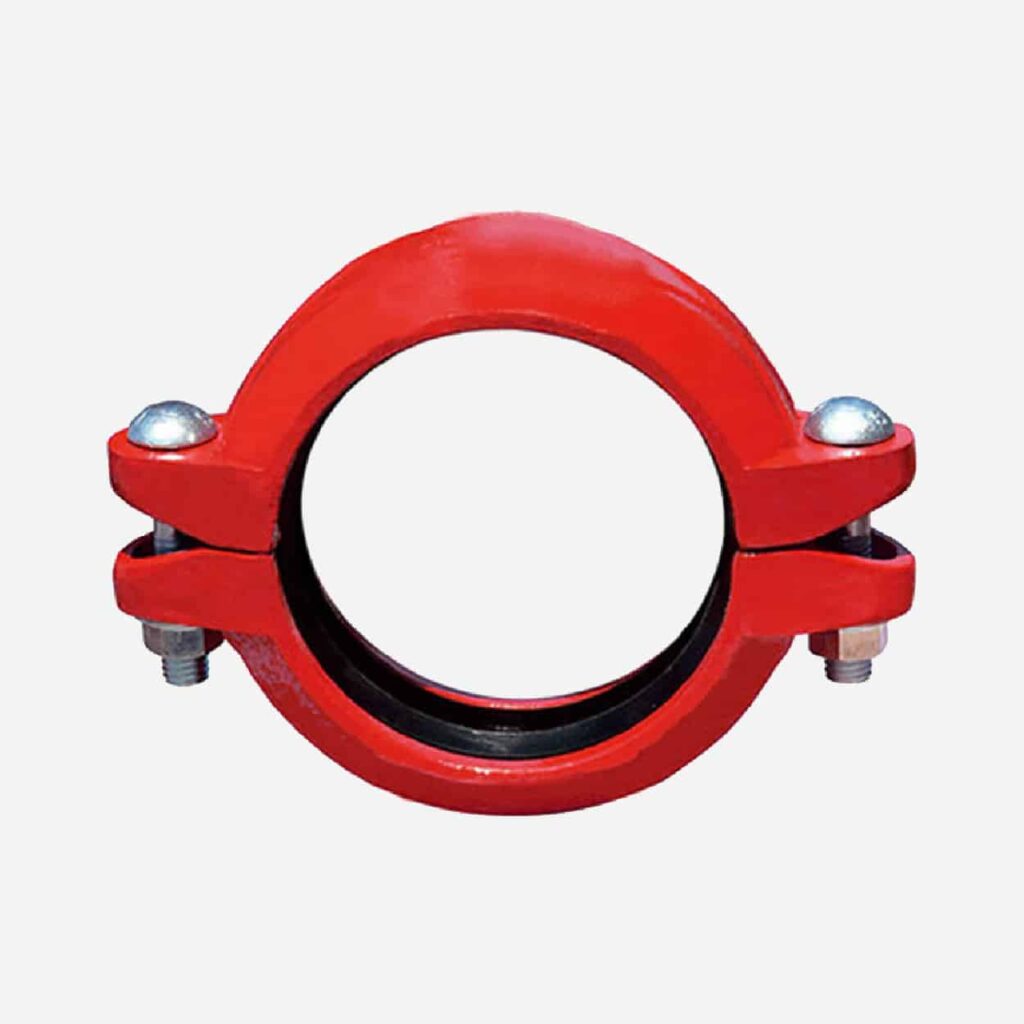
Ductile Iron Middle pressure flexible coupling(Working Pressure 7 Mpa for small size, 5 Mpa for big size)
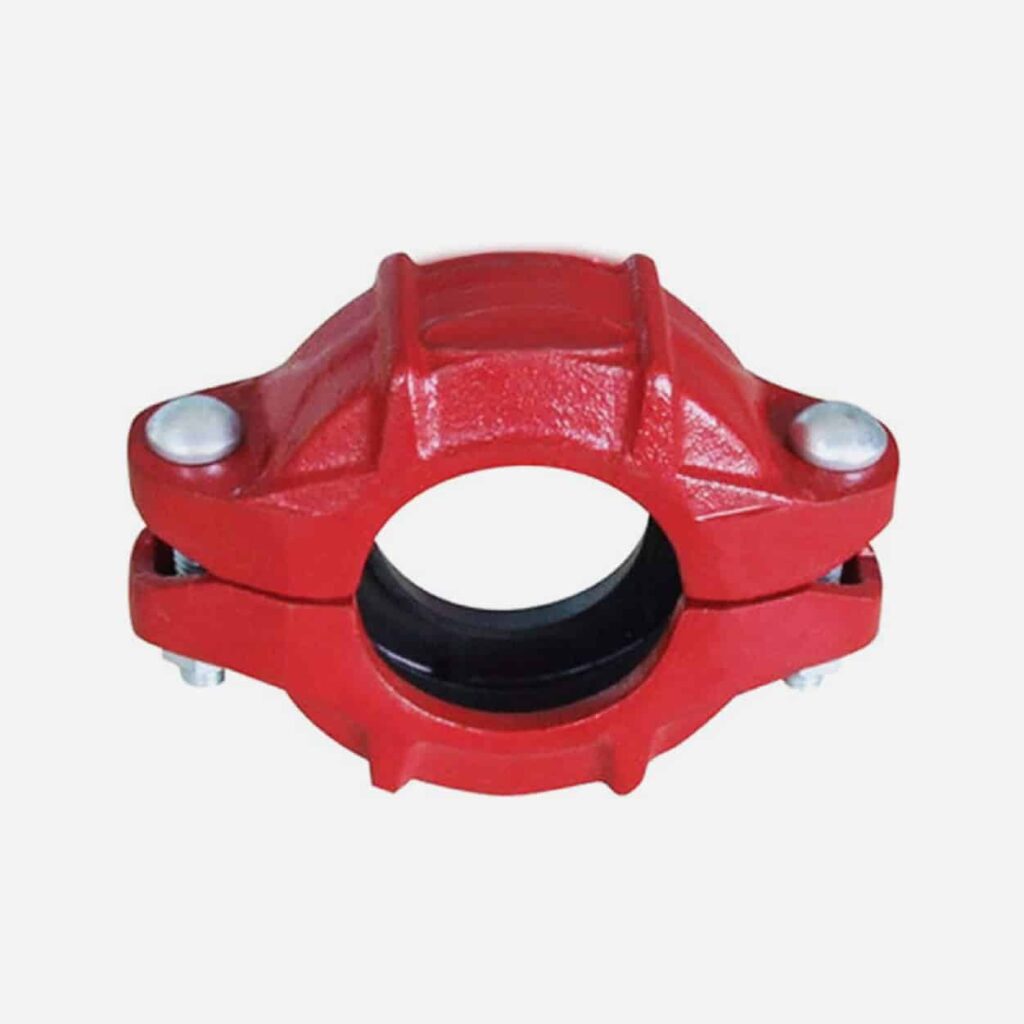
Ductile Iron High Pressure Flexible Coupling(Working Pressure 10 Mpa for small size, 8 Mpa for big size)
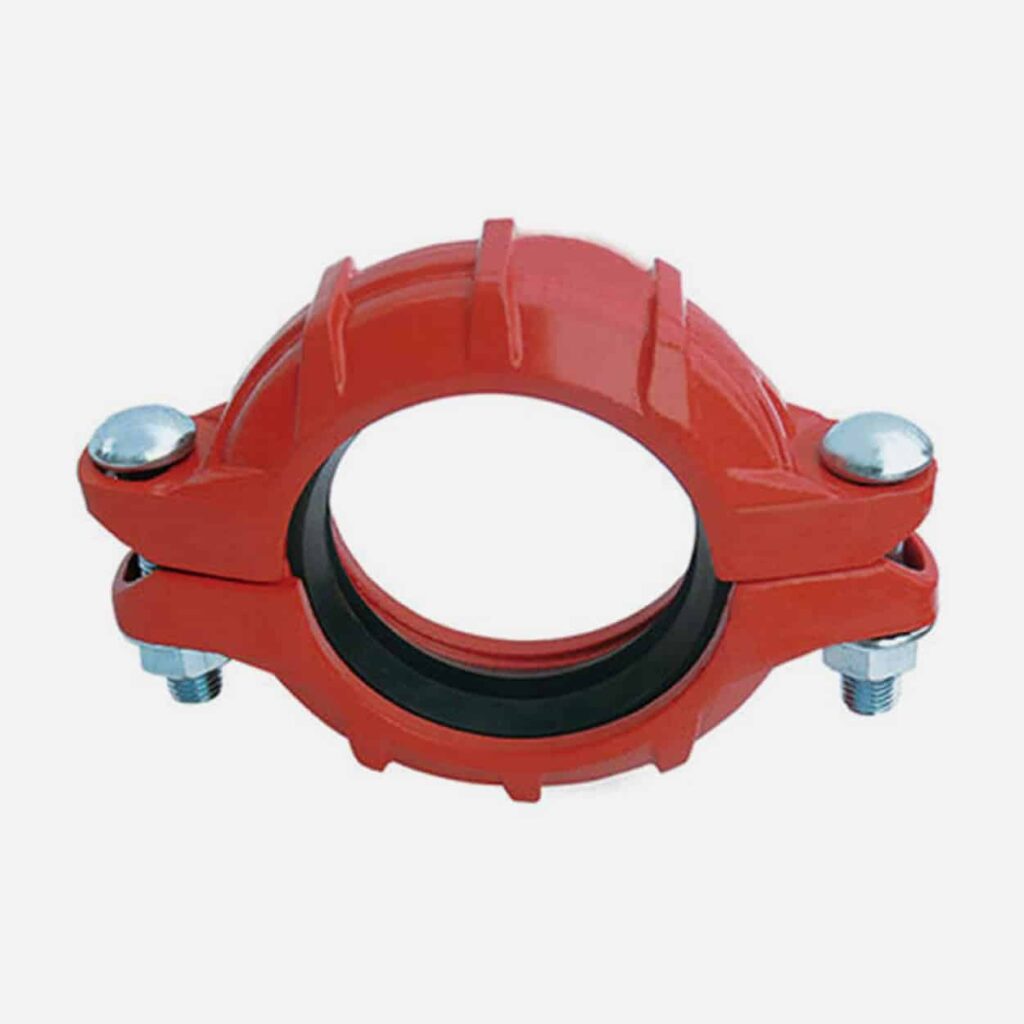
Ductile Iron Super high pressure flexible coupling(Working Pressure 15 Mpa for small size, 10.5 Mpa for big size)
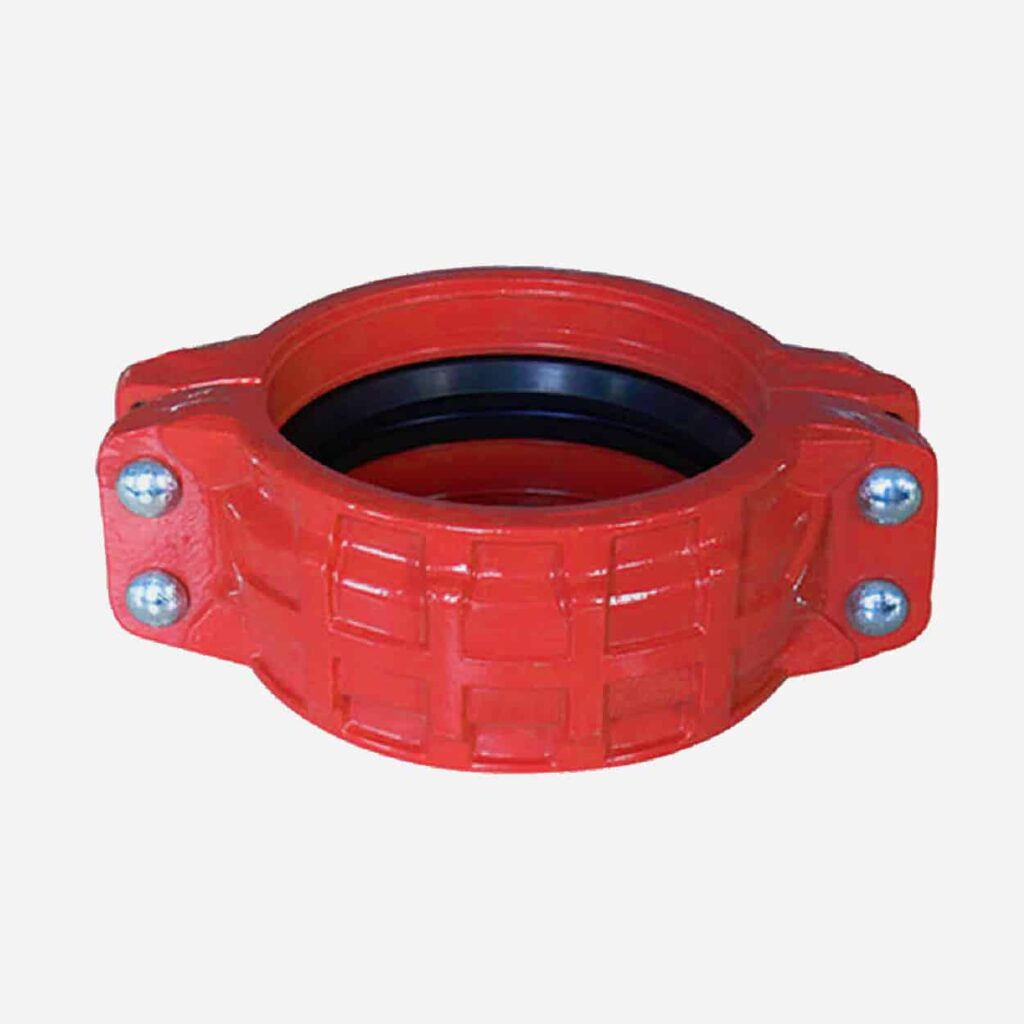
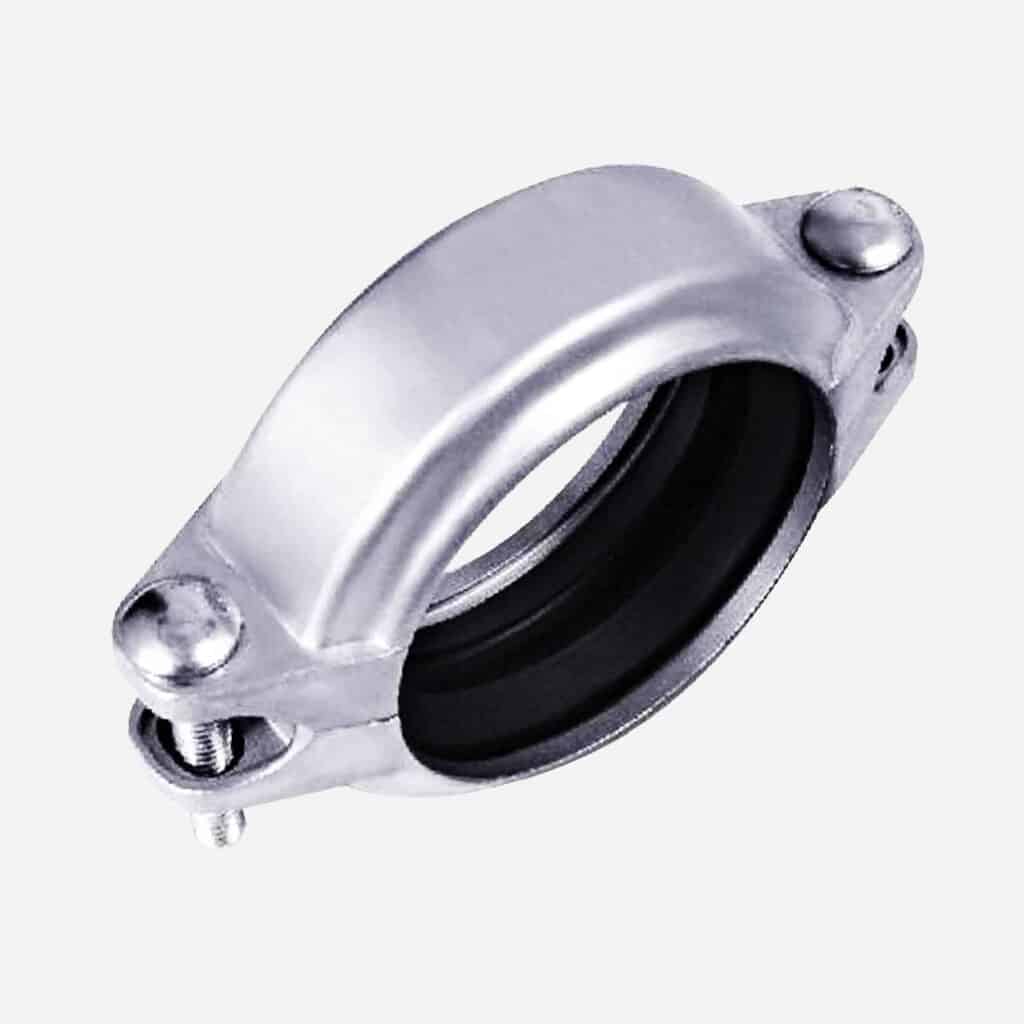
Stainless Steel Low-Pressure Flexible Groove Coupling with rated Working Pressure- 350 psi (25 bar)
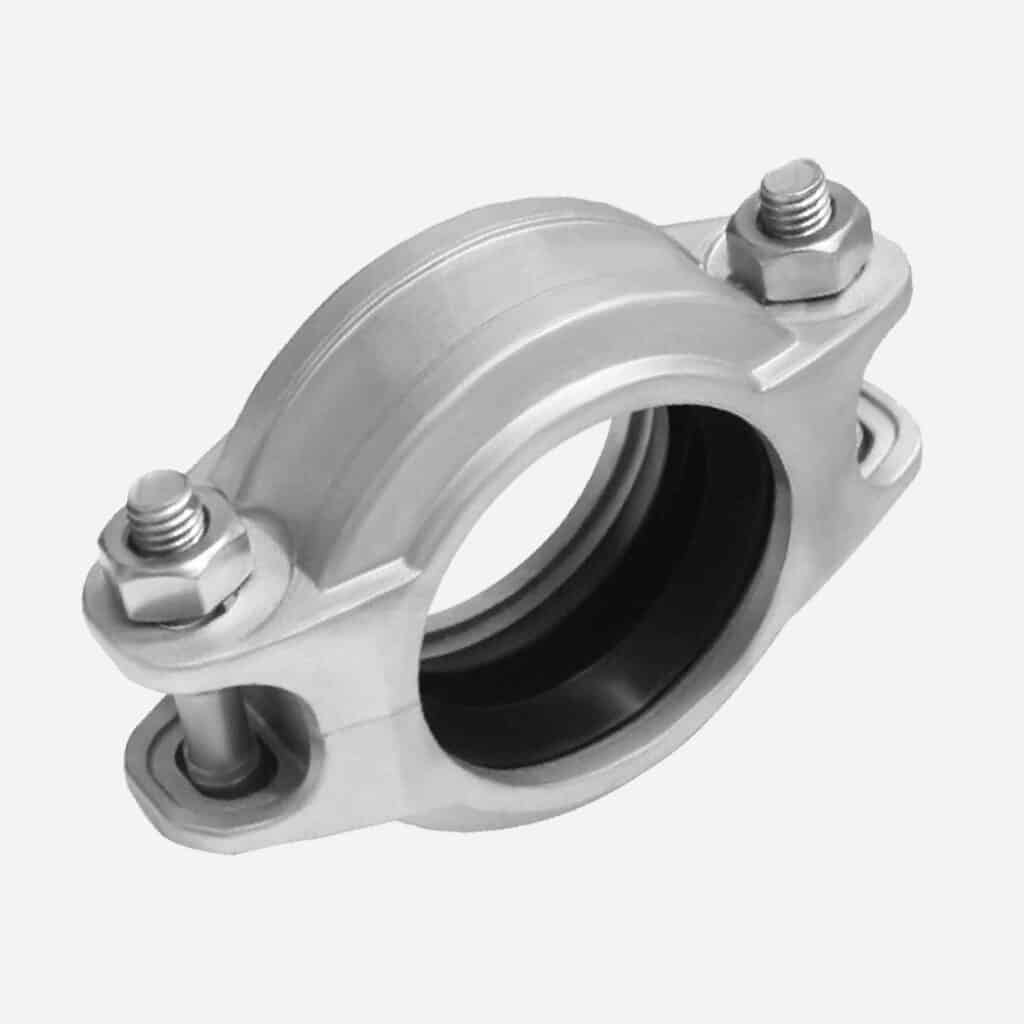
Stainless Steel Medium-Pressure Flexible Groove Coupling with Rated Working Pressure- 600 psi (42 bar)
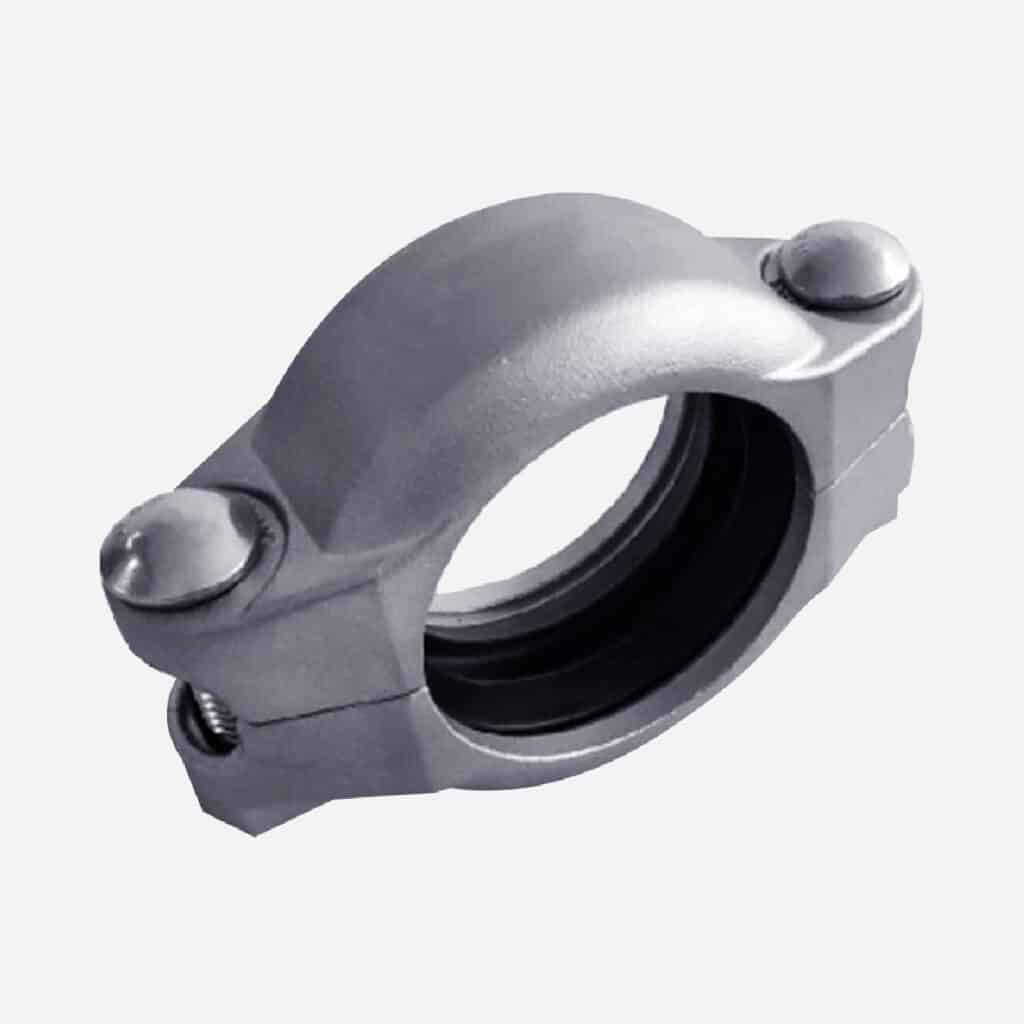
Stainless Steel High-Pressure Groove Flexible Coupling with rated Working Pressure- 1200 psi (83 bar)
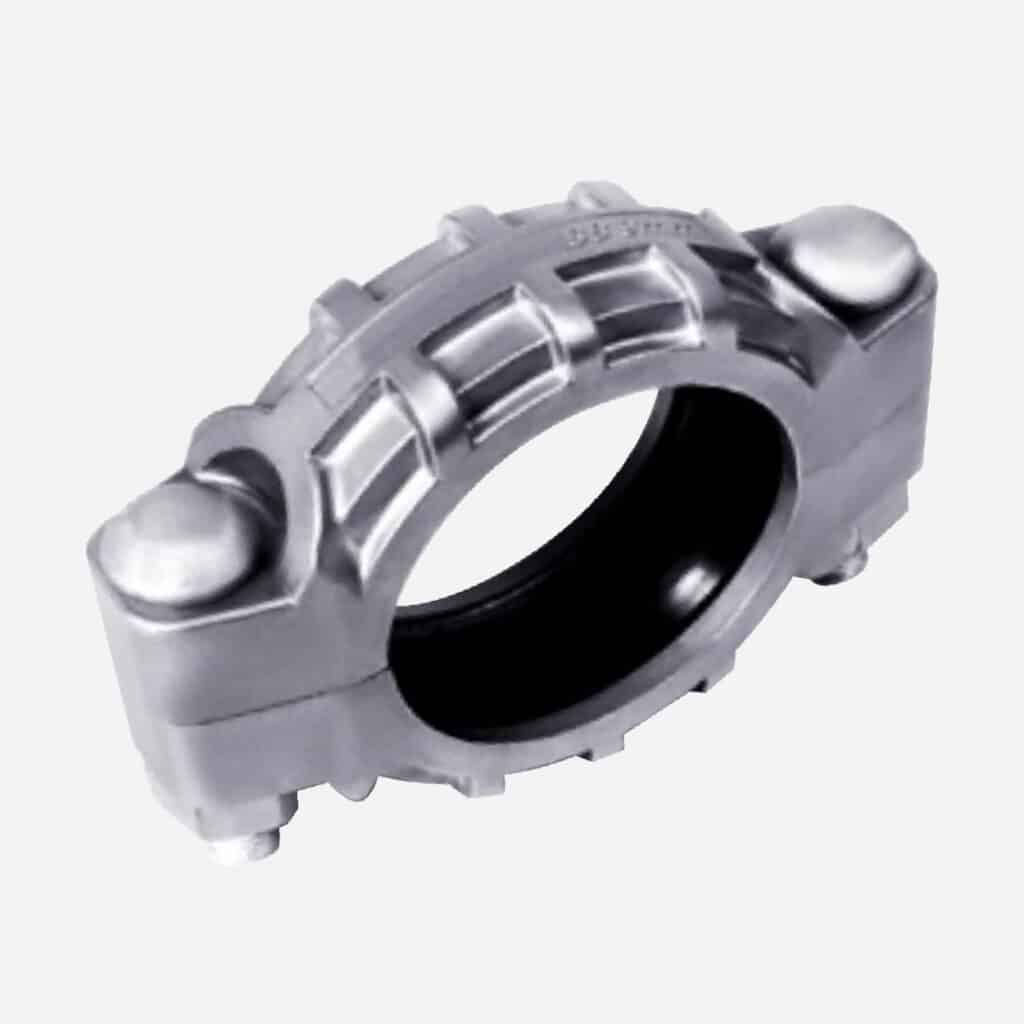
Stainless Steel High-Pressure Groove Flexible Coupling with rated Working Pressure- 1500 psi (100 bar)
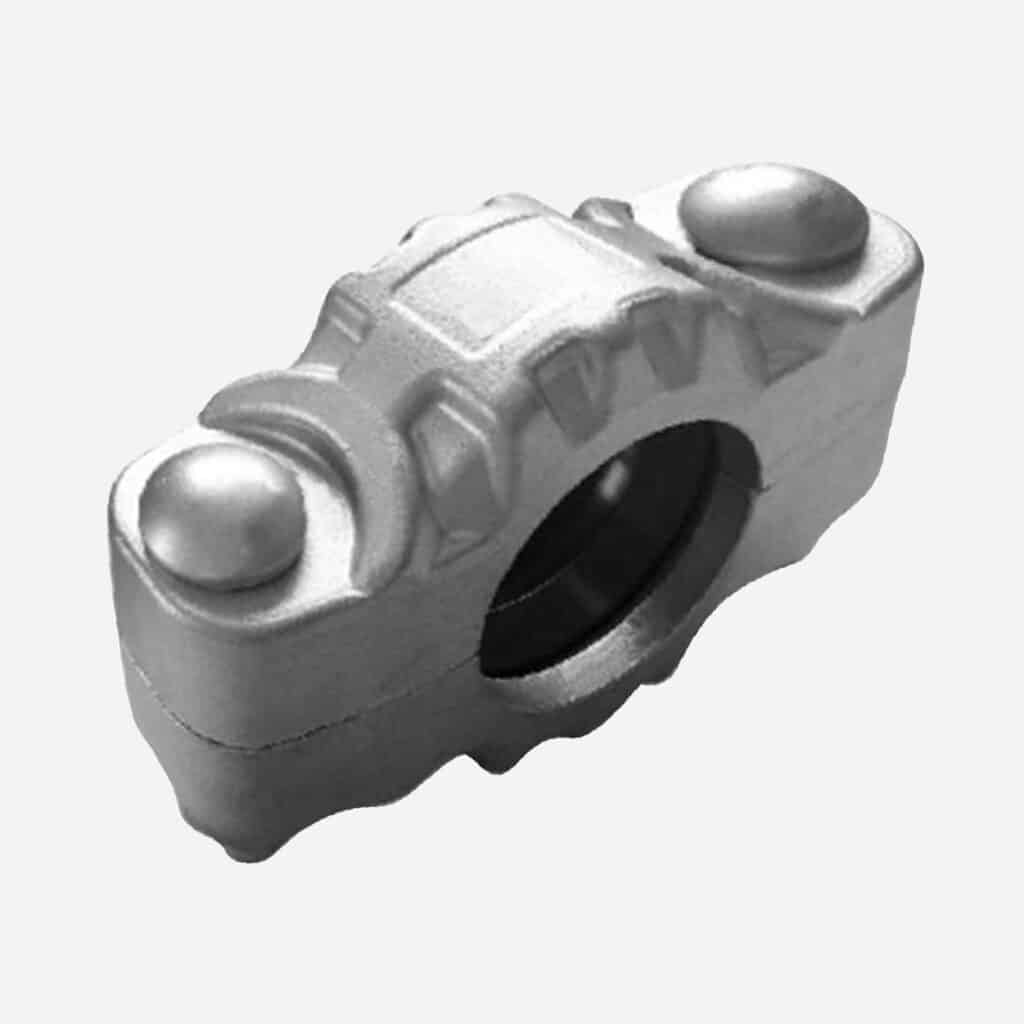
Stainless steel ultra high-pressure flexible groove coupling with rated working pressure- 2320 psi (160 bar)
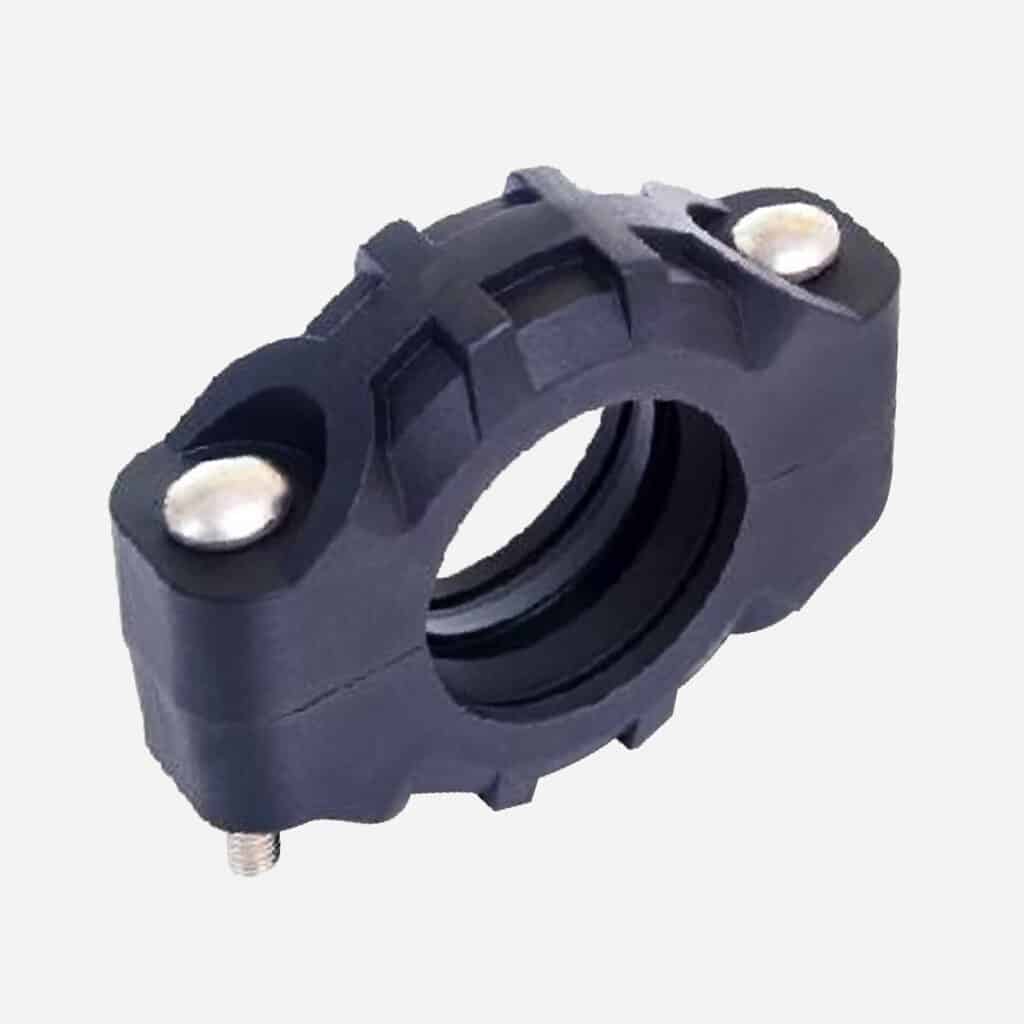
Corrosion-resistant flexible groove coupling with maximum working pressure is 300 psi (21 bar)
Function and Working Principle
Flexible grooved coupling is designed to connect two grooved-end pipes securely while allowing limited, controlled movement between them.
● It serves two main purposes:
Sealing the joint to prevent leaks and allowing flexibility to accommodate pipe system movement
How it works
Grooved Pipe Ends
_
Each pipe to be connected has a machined or rolled groove near its end.
Rubber Gasket
_
A C-shaped elastomer gasket is placed between the pipe ends. It wraps around the circumference and sits inside the grooves.
Coupling Housing
_
Two ductile iron (or other metal) coupling halves clamp over the gasket and pipe grooves. These halves are bolted together to provide compression.
Bolts and Nuts
_
The bolts tighten the housing, compressing the gasket. This creates a pressure-responsive seal that strengthens under internal pressure.
Flexibility Provided by the Coupling
Because of the internal design and slightly loose grip within the grooves, flexible couplings allow:
Axial Movement (Expansion/Contraction)
_
Typically allows up to ±1/8 inch (3.2 mm) to ±1/4 inch (6.4 mm), depending on the size and model.This is useful for thermal expansion or contraction of pipelines.
Angular Deflection
_
Usually up to 1° to 3° per coupling, allowing pipes to bend slightly or follow curves without additional fittings.
Lateral Movement (Offset)
_
Some models can tolerate minor pipe misalignment during installation.
How It Achieves Flexibility
Groove Engagement
_
The pipe grooves allow the coupling to grip the pipe ends without fully locking them in a rigid position, giving space for controlled movement.
Gasket Compression
_
The rubber gasket forms a tight seal even as the pipes shift slightly, maintaining leak protection while permitting movement.
Housing Design
_
The coupling housing is slightly wider than the groove, enabling movement within a safe range without compromising connection strength.
Benefits of This Design
_
Absorbs vibration and noise, allows for thermal expansion/contraction, compensates for minor pipe misalignment, reduces stress on piping systems
Application Scenarios for Flexible Grooved Couplings
Flexible grooved couplings are widely used in
HVAC (Heating, Ventilation, and Air Conditioning)
systems
_
To handle thermal expansion and vibrations caused by heating/cooling cycles
Fire sprinkler systems
_
allows fast installation and reliable sealing; supports seismic movement
Water supply and drainage systems
_
absorbs building settlement or ground movement; prevents stress on pipes
Oil and gas transportation pipelines
_
Manages pressure fluctuations and allows quick field repairs
Vibration-prone environments
_
Dampens vibration from pumps, motors, or seismic activity
Advantages and Disadvantages
Advantages of Flexible Grooved Couplings
Thermal Expansion Absorption
_
Flexible couplings allow axial movement, making them ideal for systems with temperature fluctuations (e.g., HVAC, long pipelines).
Vibration and Noise Damping
_
The rubber gasket and flexible connection help absorb vibration and reduce noise, which is beneficial in mechanical rooms and buildings.
Quick and Easy Installation
_
No welding or threading is required. The coupling is simply clamped over the grooved pipe ends and tightened with bolts, saving labor time and cost.
Allows Angular Deflection and Misalignment
_
Useful for accommodating slight misalignments during installation or pipe movement due to ground shifting or building settling.
Leak-Proof Sealing
_
The pressure-responsive gasket ensures a secure seal, even under fluctuating pressures.
Maintenance-Friendly
_
Components can be easily disassembled and reassembled for inspection, replacement, or re-routing.
Disadvantages of Flexible Grooved Couplings
Limited Pressure Rating
_
Compared to welded or flanged connections, flexible couplings may have lower pressure or load capacity, depending on the design and material.
Not Suitable for Rigid Support Requirements
_
In applications requiring zero movement or structural rigidity (e.g., risers or load-bearing systems), rigid couplings are preferred.
Higher Initial Component Cost
_
The material and gasket can be more expensive than traditional joint methods, though this is often offset by lower labor and installation costs.
Sizes, Standards & Material Selection for Flexible Grooved Couplings
Common Sizes & Pipe Compatibility
Flexible grooved couplings are manufactured to match international pipe standards such
as:ANSI / ASME B36.10 / B36.19 (for carbon steel and stainless steel pipes), ISO / DIN / JIS (for global applications)
Typical size range
DN25 (1″) to DN600 (24″), Some manufacturers offer sizes up to DN1200 (48″) for special industrial applications.
Compatible pipe types
Carbon steel pipes (schedule 10/40), Stainless steel pipes, Ductile iron pipes, PVC and HDPE pipes (with special adapters or rings)
Housing Materials: When to Use What?
Material | Use Case / Advantages |
---|---|
Ductile Iron | Most common choice. Strong, durable, cost-effective. Suitable for water, HVAC, fire systems. |
Carbon Steel | Used in industrial applications requiring higher strength or temperature resistance. |
Stainless Steel (304/316) | For corrosive environments (e.g., chemical plants, marine, food & beverage). More expensive. |
Aluminum | Lightweight applications or where corrosion is minimal. Less common. |
Gasket (Sealing Ring) Materials & Medium Compatibility
The gasket plays a crucial role in sealing the joint. It must be selected based on the fluid/gas being transported and the operating temperature.
Gasket Material | Recommended For | Temperature Range | Notes |
---|---|---|---|
EPDM | Cold/hot water, air, diluted acids | -30°C to +110°C | Not suitable for oil or hydrocarbons |
NBR (Nitrile) | Oil, fuel, gas, hydrocarbons | -20°C to +80°C | Not suitable for steam or strong acids |
Silicone | High-temp air, food-grade systems | -55°C to +180°C | Excellent heat resistance, FDA-approved types |
FKM (Viton) | Chemicals, aggressive fluids, high temperature | -10°C to +200°C | Expensive but very durable in harsh environments |
PTFE-lined | Highly corrosive chemicals, solvents | Varies (depends on structure) | For chemical plants, special applications |
Summary: Choosing the Right Materials
Water systems
Ductile iron body + EPDM gasket
Oil & fuel
Carbon steel or ductile iron + NBR gasket
Seawater or corrosive environment
Stainless steel + EPDM or FKM gasket
Food-grade or high temperature
Stainless steel or aluminum + silicone gasket
Chemical transport
Stainless steel + FKM or PTFE-lined gasket
RELATED PRODUCTS
Reducing Coupling
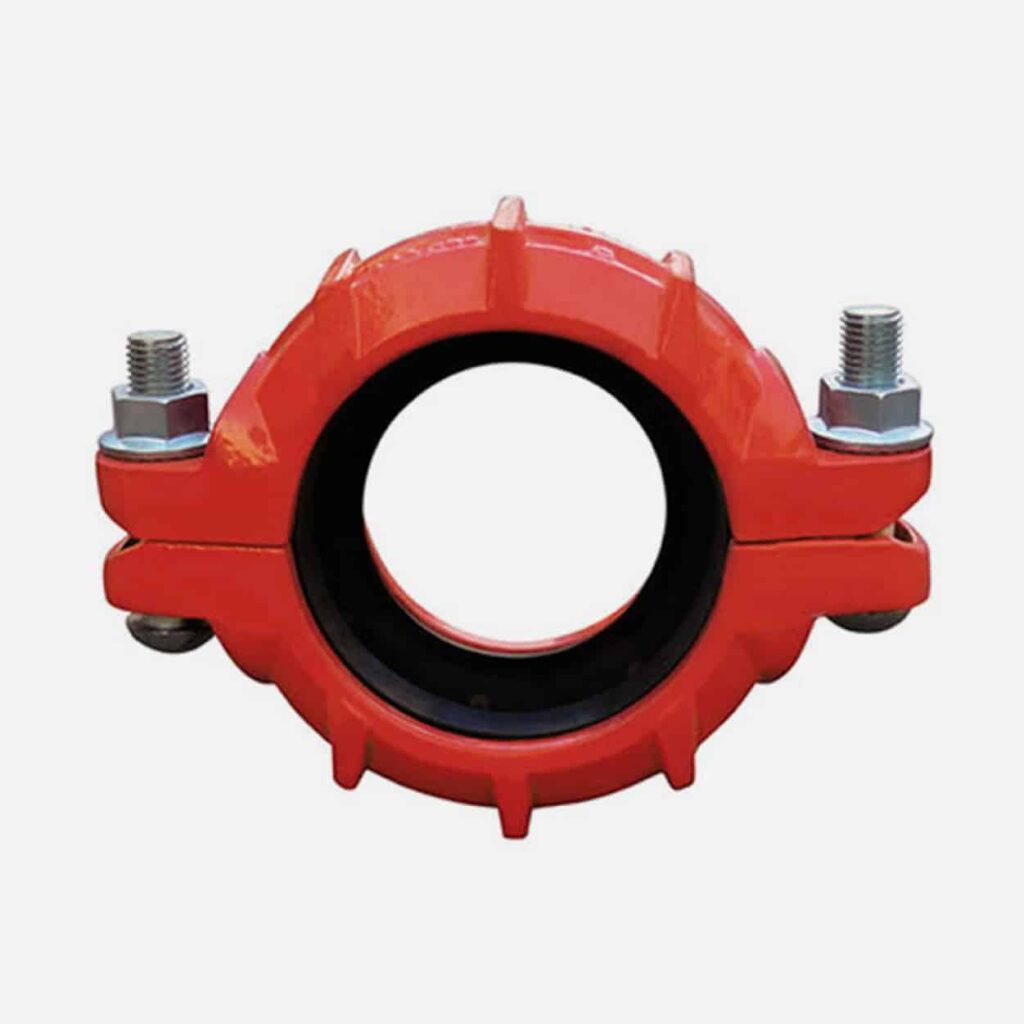
Shouldered Coupling
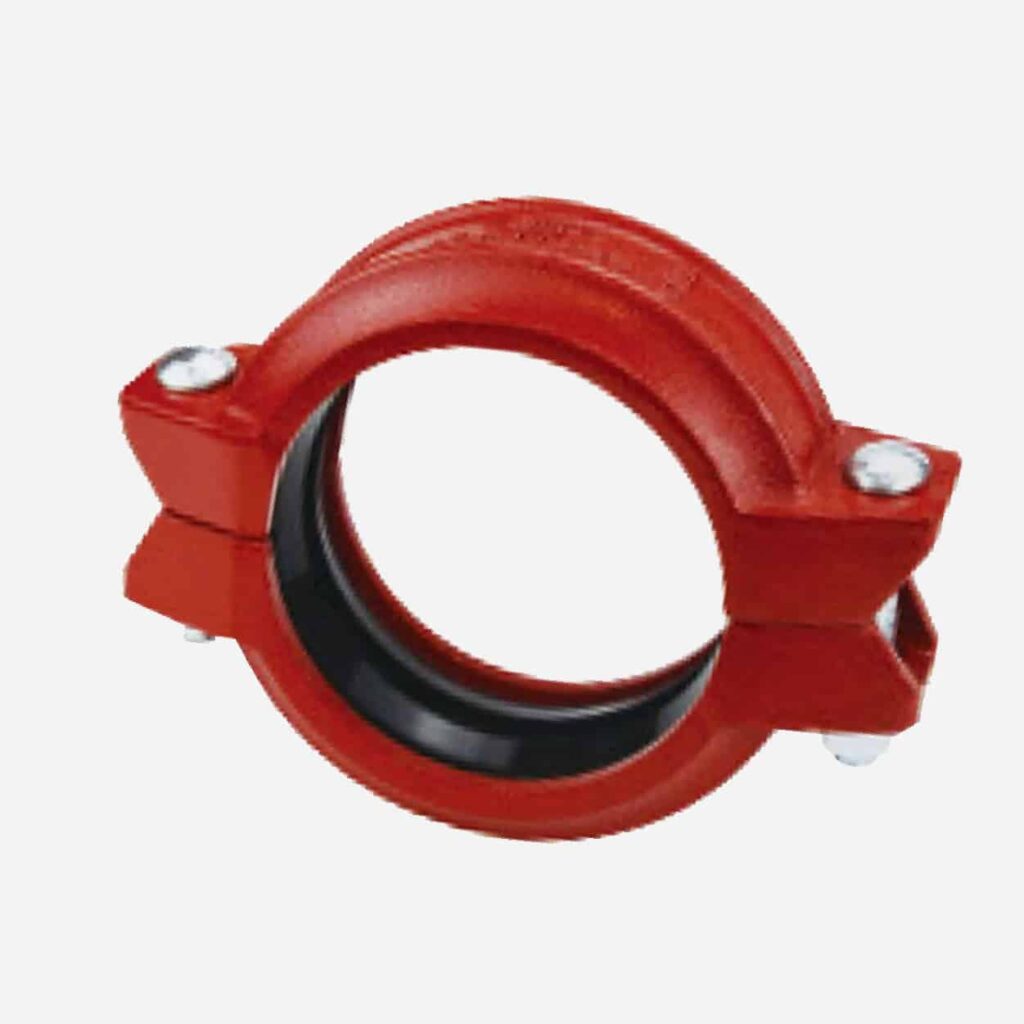
Ring Joint Coupling
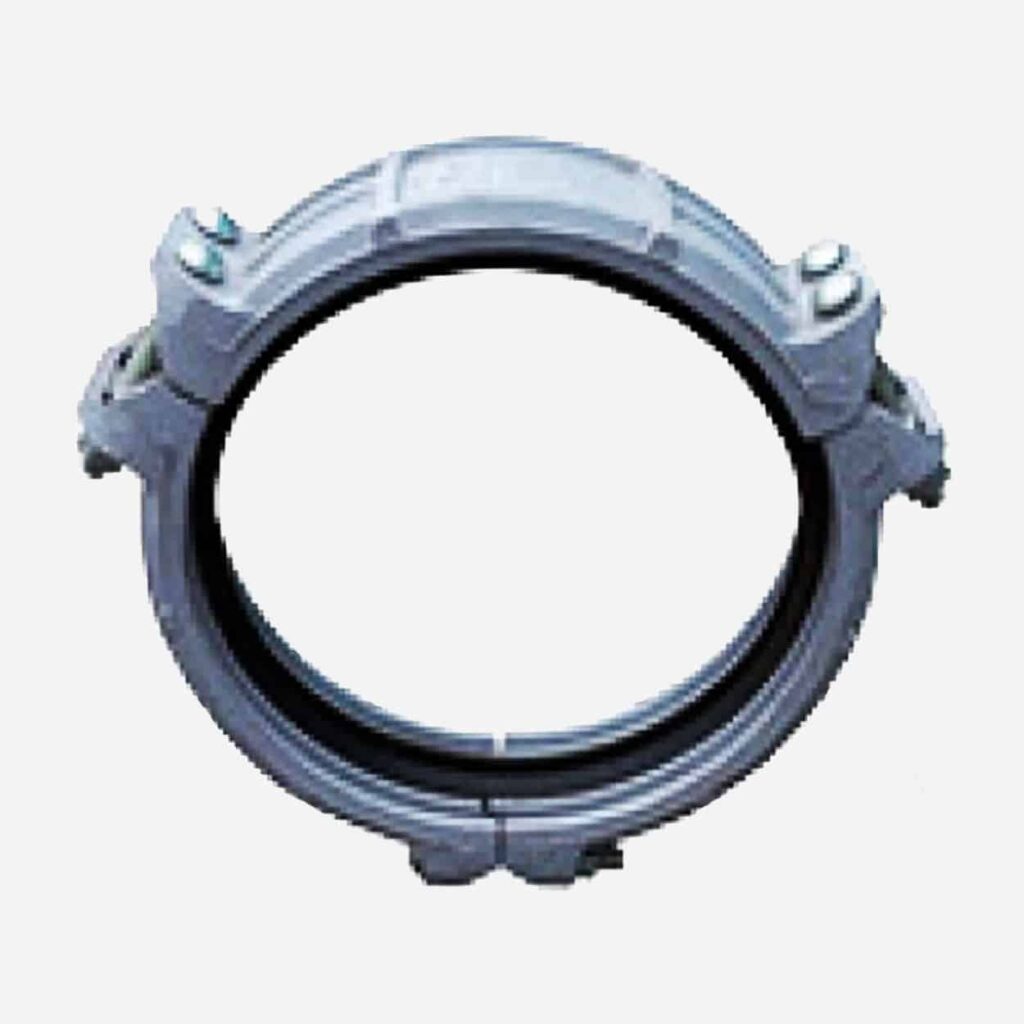
Coupling for HDPE Pipe
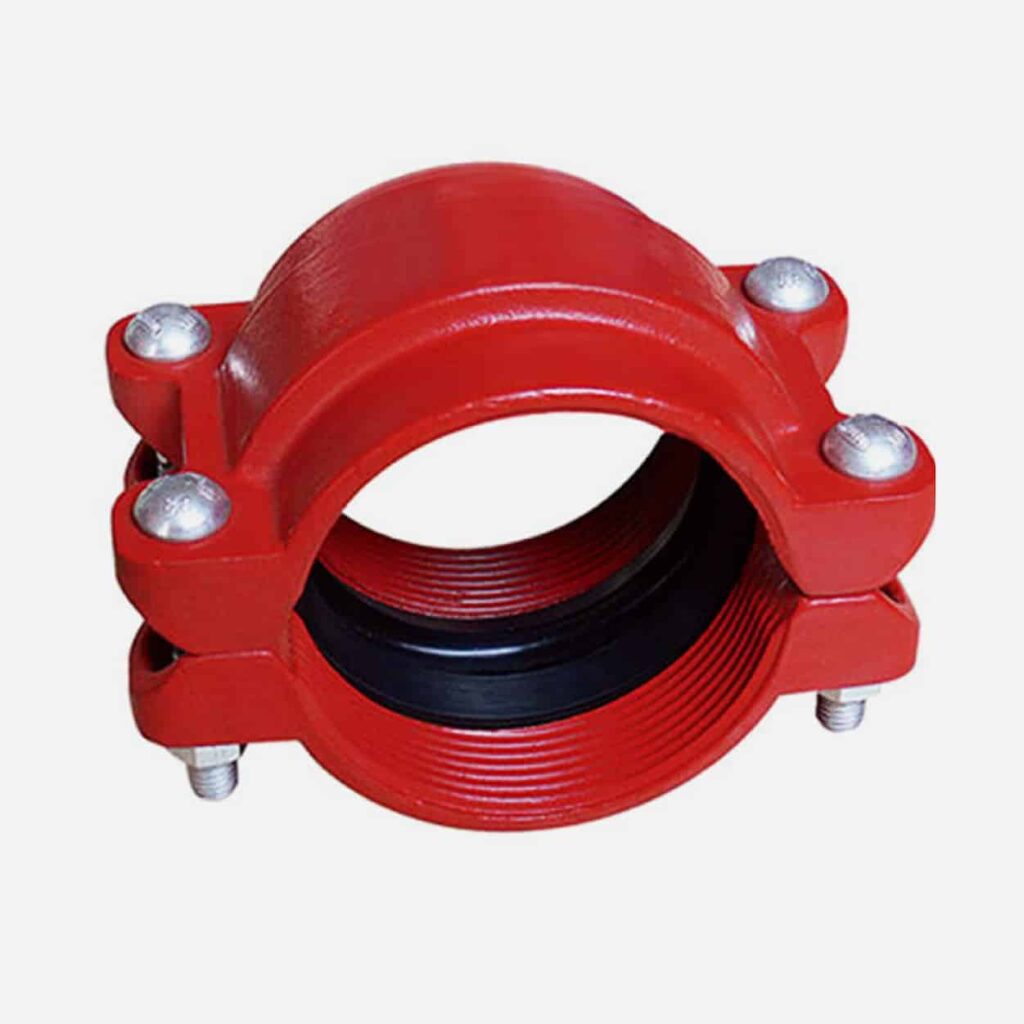
Transition coupling for HDPE pipe to Steel pipe
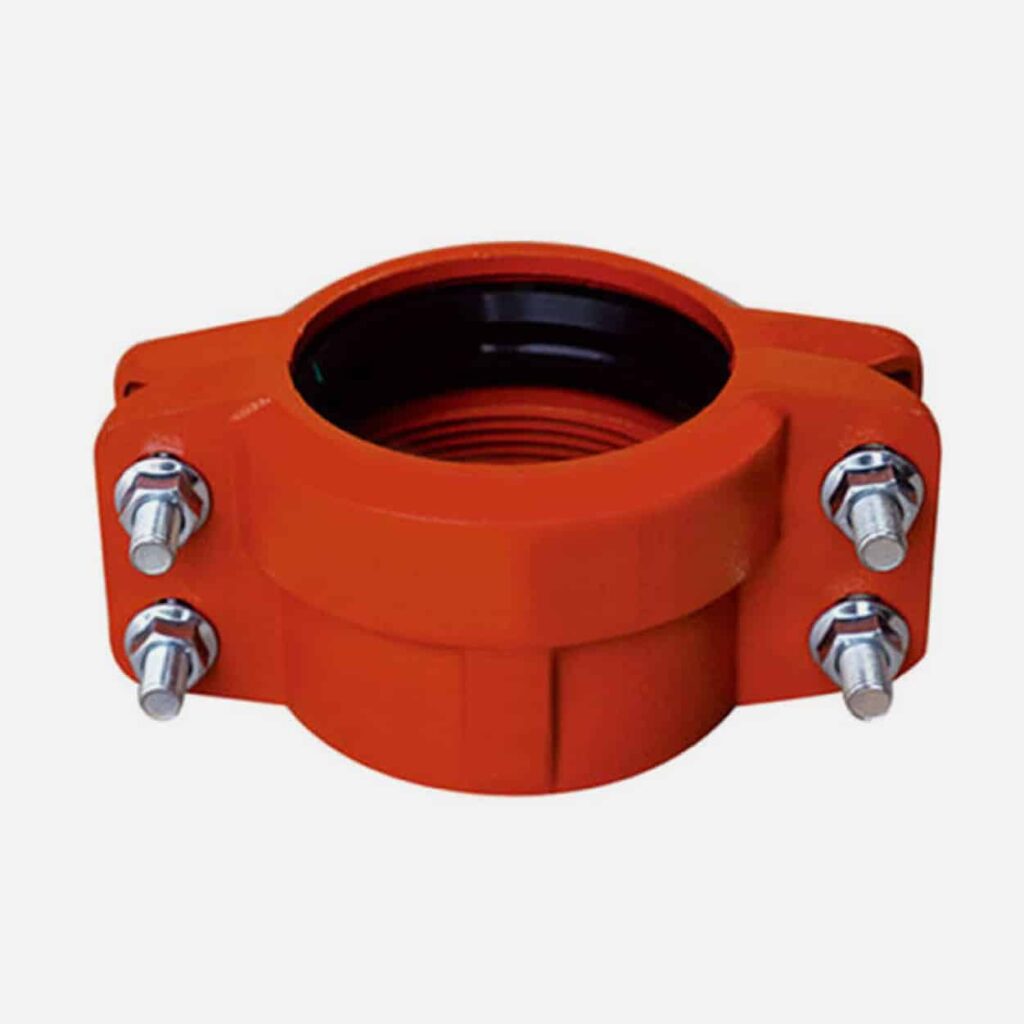