Flow straightener is a device used in pipelines to reduce turbulence and make the flow of fluid more uniform. It improves the accuracy of flow measurements and enhances the overall efficiency of fluid transport by straightening the flow before it enters measurement or control devices.As a flow straightener manufacturer in china, we can manufacture flow straightener as below
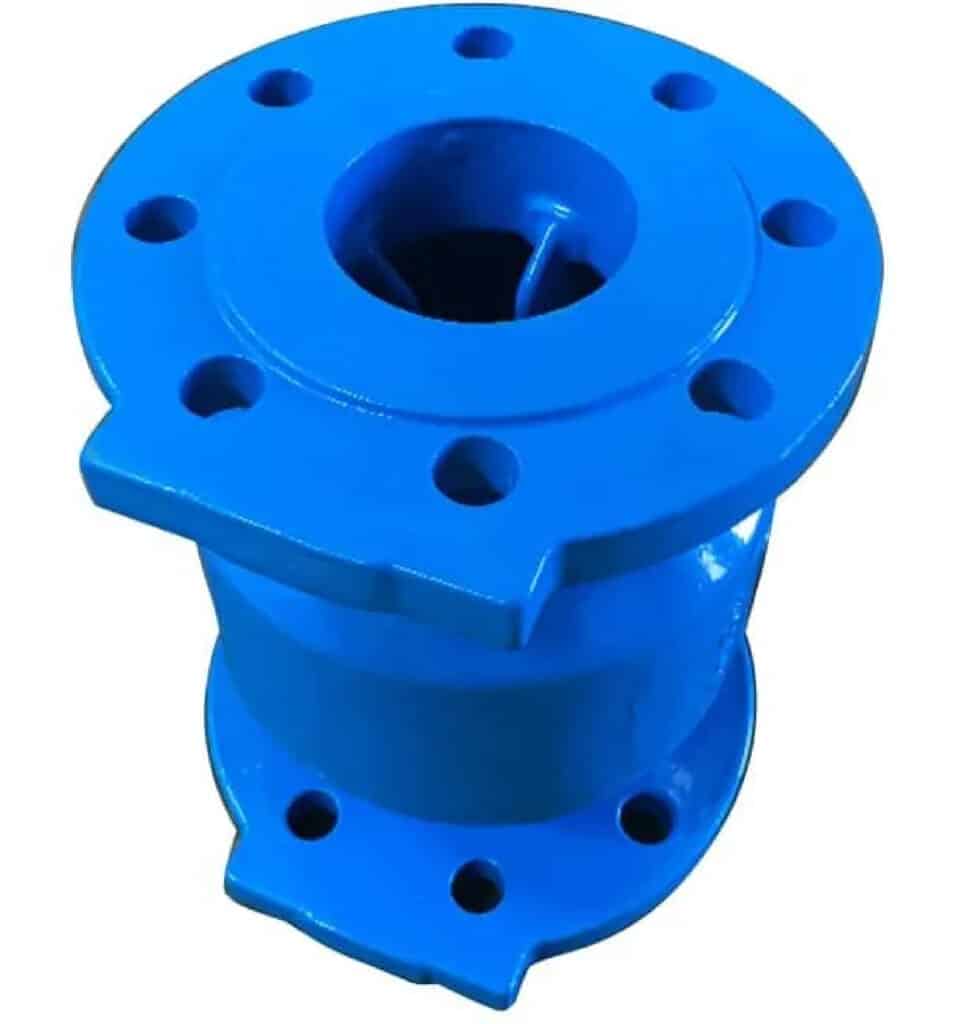
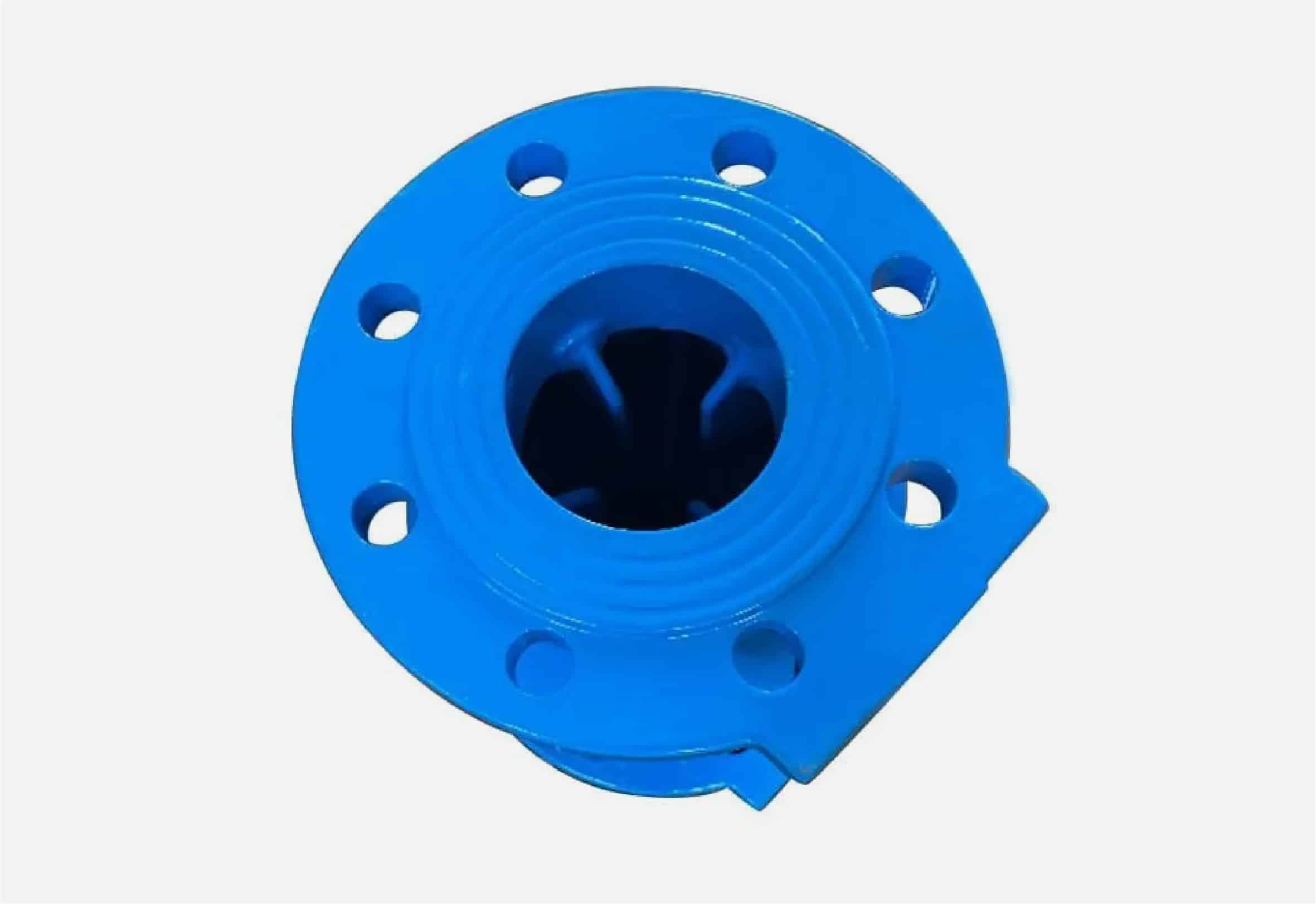
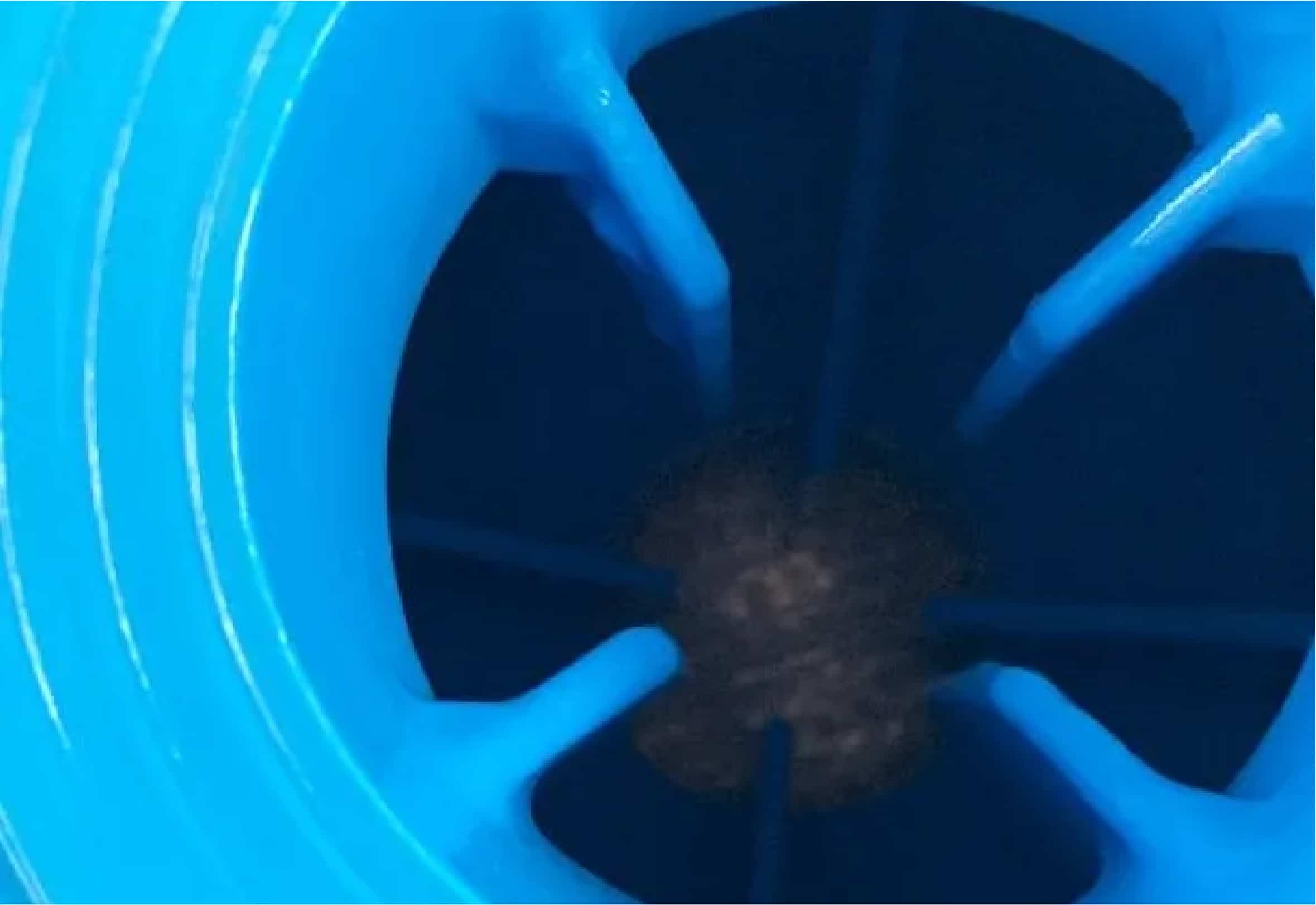
AS A WATER FLOW STRAIGHTENER MANUFACTURER, WHAT WE DO TO ASSURE THE GOOD QUALITY?
● Sand cast from material ductile iron ENGJS450-10,ENGJS500-7 etc
● Grind the casting surface to be very smooth
● Machine the flange hole and flange surface according to flange norm which is required by client
● Make the FBE coating according to EN14901
● Pay attention, inspection should be followed for above steps
● Do the pressure test (pressure test should be 1.5 times of working pressure
● Do the final inspection for dimension, visual, coating thickness ,coating adhesion, mark ,other inspection items according to client requirement.
● Packing the flow straightener according to client requirement
WORKING PRINCIPLE
Flow straighteners work by aligning the flow of fluid or gas to reduce turbulence.
They do this by using structures such as honeycomb cells, grids, or meshes that redirect and straighten the flow before it reaches sensitive equipment like flow meters or control valves.
By ensuring that the flow is more uniform and less turbulent, flow straighteners improve the accuracy and efficiency of systems.
PERFORMANCE ADVANTAGES
REDUCED ENERGY CONSUMPTION
_
By straightening the flow, flow straighteners help eliminate turbulence, which can create additional resistance in the pipeline. This reduced turbulence leads to lower friction and pressure losses, meaning the pump or compressor has to work less hard to maintain flow, thus saving energy.
IMPROVED MEASUREMENT ACCURACY
_
In systems that rely on flow meters or other measuring instruments, a consistent and uniform flow is critical for accurate measurements. Flow straighteners eliminate disturbances in the flow profile, ensuring that flow meters receive steady, smooth fluid. This leads to more accurate readings and better control over fluid systems.
EXTENDED EQUIPMENT LIFESPAN
_
When fluid flows are turbulent or uneven, equipment like pumps, valves, and flow meters are subjected to higher levels of wear and stress. By straightening the flow, flow straighteners reduce the strain on these components, helping to extend their operational life and reduce the frequency of repairs and replacements.
REDUCED VIBRATION AND NOISE
_
Turbulent flows often cause vibrations and noise, which can affect both equipment performance and operator comfort. Flow straighteners minimize these effects by smoothing the flow, leading to quieter, more stable operation.
OPTIMIZED SYSTEM EFFICIENCY
_
By improving flow conditions, flow straighteners optimize the overall system performance. More efficient fluid flow results in better fluid handling, enhanced thermal transfer in heat exchangers, and overall smoother operations, reducing the need for additional system adjustments or energy input.
Flow straighteners help reduce energy consumption, improve measurement accuracy, extend the lifespan of equipment, and optimize overall system efficiency by ensuring smooth, uniform flow. These benefits make them essential components in many fluid and gas handling systems, contributing to both cost savings and more reliable performance.
FLOW STRAIGHTENER TYPES AND USAGE
HONEYCOMB FLOW STRAIGHTENER
_
Made of a series of hexagonal cells, it helps to straighten the flow and is commonly used in gas and air systems. It’s effective for high-velocity flow and can be compact and efficient.
GRID FLOW STRAIGHTENER
_
Consists of a series of perpendicular bars that create a grid-like structure. It’s often used in both liquid and gas pipelines, providing good flow direction control with moderate pressure loss.
MESH FLOW STRAIGHTENER
_
Uses a mesh or wire net to straighten the flow. It’s suitable for applications where space is limited and is often used in low to medium velocity flows.
CHOOSING THE RIGHT TYPE
Honeycomb
_
Best for high-velocity flows or when space is tight.
Grid
_
Ideal for general-purpose use in both liquids and gases with moderate flow speeds.
Mesh
_
Suitable for low-velocity or confined spaces where flow needs to be straightened efficiently with minimal pressure drop.
Selecting the right type depends on factors like flow velocity, space availability, and the medium being transported.
INSTALLATION AND MAINTENANCE
INSTALLATION STEPS
POSITIONING
_
Ensure the flow straightener is installed in a straight section of the pipeline, ideally several pipe diameters away from any bends, valves, or other flow disturbances.
The flow direction marked on the flow straightener should match the direction of the fluid flow in the pipeline.
ALIGNMENT
_
Align the flow straightener properly with the pipeline to avoid any misalignment that could cause turbulence or uneven flow.
If using a honeycomb or mesh type, make sure it is securely held in place to prevent movement during operation.
SECURING
_
Install flanges or bolts (depending on the type of flow straightener) to secure the device in place. Ensure that all connections are tight and leak-proof.
Use appropriate sealing gaskets if necessary to prevent fluid leakage at the connection points.
TESTING
_
Once installed, perform a pressure test or flow test to verify that the flow straightener is functioning as expected and that there are no leaks.
MAINTENANCE TIPS
REGULAR INSPECTION
_
Inspect the flow straightener regularly for any signs of wear, corrosion, or blockage. This is especially important in systems handling particles or corrosive fluids.
Ensure that there are no build-ups of debris, dirt, or scaling that could affect flow performance.
CLEANING
_
Clean the flow straightener periodically, especially if it is used in liquid or gas systems where deposits are likely to form.
For mesh or grid types, use a soft brush or compressed air to clear any obstructions.
For honeycomb types, carefully remove any debris or residue that may have collected between the cells.
CHECK FOR DAMAGE
_
Inspect the device for any structural damage, such as cracks or deformations, that could compromise its effectiveness.
If the flow straightener is damaged, replace it promptly to ensure continued system efficiency.
CHECK ALIGNMENT
_
Over time, vibrations or external forces can cause misalignment. Ensure that the flow straightener remains aligned with the pipeline and has not shifted.
MONITOR PERFORMANCE
_
Continuously monitor system performance to ensure that the flow straightener is maintaining stable flow. If flow measurements or fluid behavior seem irregular, inspect the device for possible issues.
By following these installation and maintenance guidelines, you can ensure that your flow straightener operates efficiently and remains in good condition throughout its lifespan. Regular checks and timely maintenance will help prevent costly repairs and downtime.