Shoulder Coupling
Shoulder coupling is a type of pipe coupling where welded rings are attached to the ends of the pipes. During installation, the welded rings are first welded to the pipe ends, and then the coupling is installed in the same manner as a grooved pipe fitting. This connection method makes it suitable for pipes that cannot undergo traditional grooving processes, such as thin-walled or large-diameter pipes.
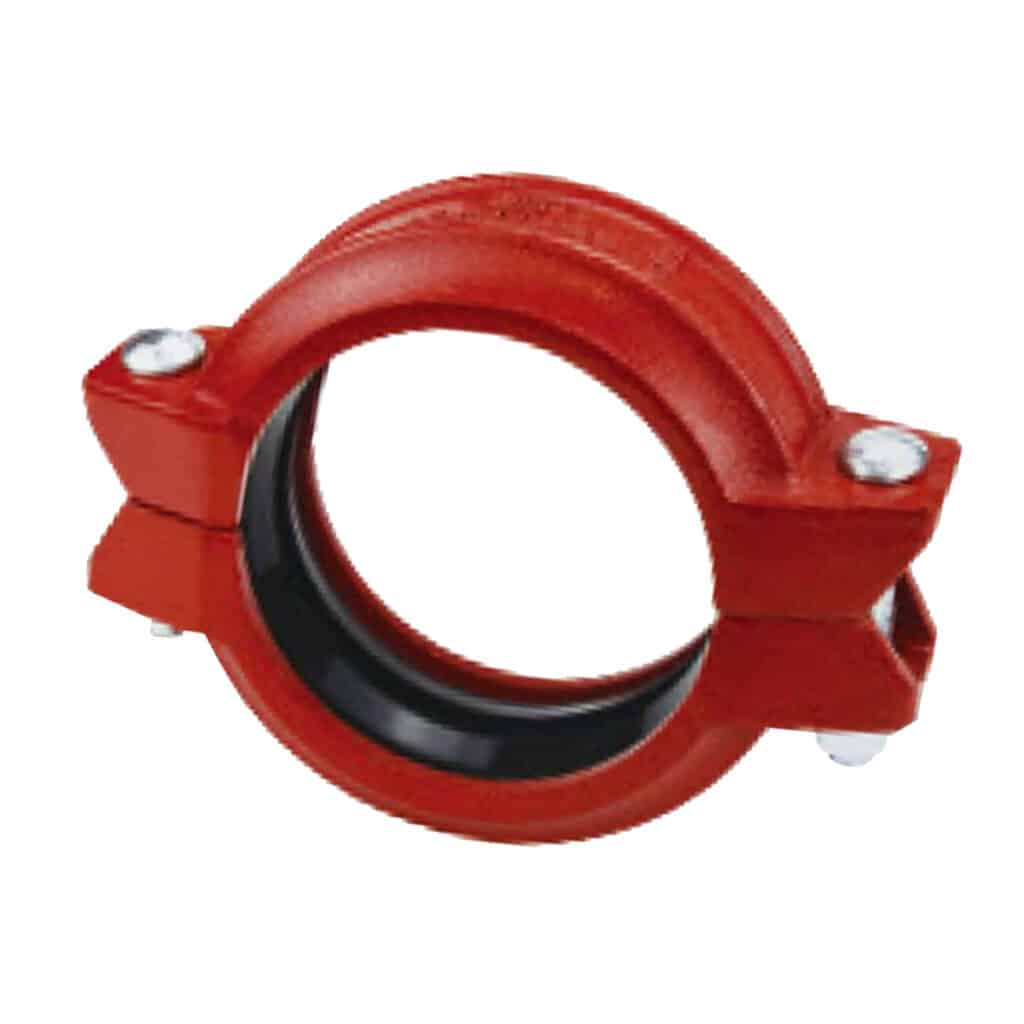
Drawing
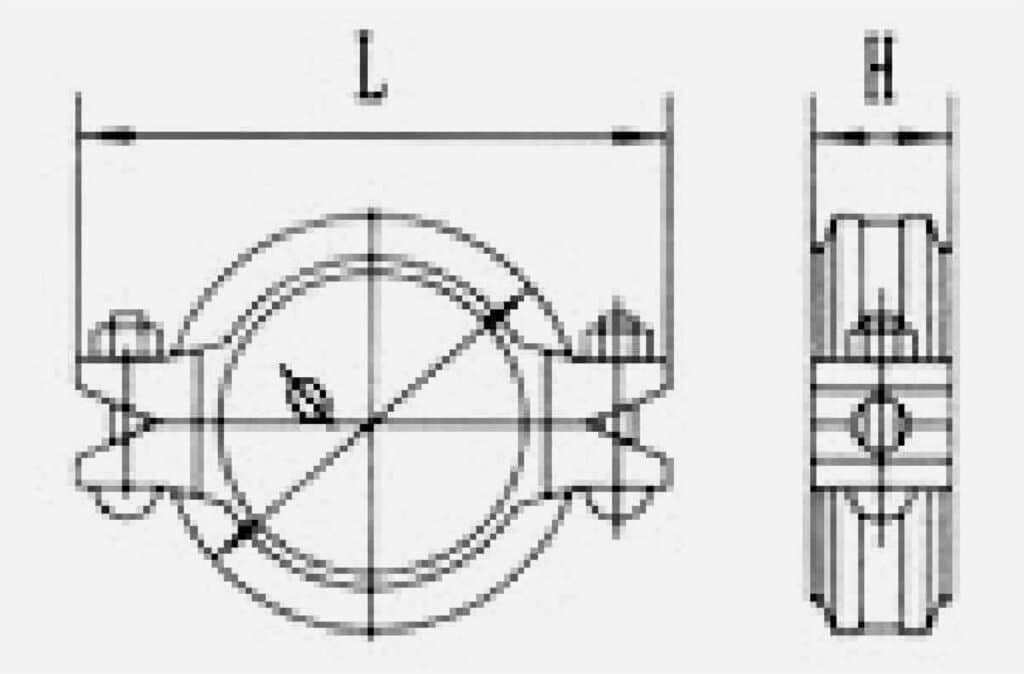
Dimension
Nominal Diameter(mm) | Pipe OUtside Diameter(mm) | Working Pressure(MPa/PSI) | Size of Bolts and Nuts | Ф | L | H |
---|---|---|---|---|---|---|
40 | 48.3 | 3.5 | 2-M10X55 | 81 | 117 | 47 |
50 | 60.3 | 3.5 | 2-M12X60 | 97 | 132 | 48 |
65 | 76.1 | 3.5 | 2-M12X65 | 108 | 153 | 46 |
80 | 88.9 | 3.5 | 2-M12X75 | 127 | 170 | 48 |
100 | 114.3 | 3.5 | 2-M12X75 | 156 | 206 | 52 |
125 | 139.7 | 3.5 | 2-M16X85 | 184 | 241 | 52 |
150 | 165.1 | 3.5 | 2-M16X85 | 212 | 273 | 52 |
200 | 219.1 | 3.5 | 2-M20X100 | 280 | 346 | 60 |
250 | 273 | 3.5 | 2-M22X130 | 342 | 416 | 64 |
300 | 323.9 | 3.5 | 2-M24x130 | 396 | 484 | 64 |
350 | 355.6 | 3.5 | 3-M22X100 | 75 |
Application
Shoulder couplings are suitable for certain types of pipes and applications where traditional grooved connections are difficult or impossible.
Below are some specific pipe types and application scenarios where shoulder couplings are particularly useful:
Thin-Walled Pipes
_
Thin-walled stainless steel pipes, thin-walled aluminum pipes, etc. These pipes have thin walls, making it difficult to perform traditional grooving because excessive machining could compromise the strength and sealing capability of the pipe. Shoulder couplings provide a solution by welding rings to the pipe ends, avoiding the need for grooving while still offering a strong seal and secure connection.
Large-Diameter Pipes
_
Large-diameter steel pipes etc. Grooving large-diameter pipes can be challenging, especially when the grooving equipment may not be suitable or precise enough for such sizes. Shoulder couplings provide an effective solution by connecting large pipes without the need for grooving, ensuring a stable and reliable connection.
Pipes That Cannot Be Grooved or Machined
_
Certain materials or pipes with special surface treatments, such as coated pipes or fiberglass pipes. These types of pipes often cannot be grooved due to their material properties. Shoulder couplings offer a reliable alternative, connecting these pipes without the need for grooves.
Old Pipeline Systems or Pipe Replacement
_
In older buildings or pipelines that need repairs, the original pipes may not be suitable for traditional grooving. Shoulder couplings are ideal for retrofitting or replacing parts of an old pipeline without damaging the existing infrastructure, providing a simple and effective way to create secure connections.
High-Pressure or High-Temperature Applications
_
Oil, gas, or steam pipelines. These applications require highly stable and leak-proof connections, and traditional grooved connections might not provide the necessary strength and sealing. Shoulder couplings, with their welded rings, ensure a strong, secure connection suitable for high-pressure or high-temperature environments.
Connecting Dissimilar Pipe Materials
_
Connecting pipes made from different materials, such as steel and PVC pipes, or aluminum and stainless steel pipes. Shoulder couplings provide a flexible and reliable connection between pipes of different materials, overcoming the challenges of sealing and strength that may arise when using traditional methods.
These situation demonstrate how shoulder couplings are particularly useful in situations where traditional grooved connections are not feasible,
offering a flexible and reliable solution for pipe connection needs while maintaining sealing and stability.
Working Principle and Advantage
Shoulder Coupling provides excellent sealing and flexibility, making it ideal for various pipeline connection needs.
Here’s a detailed explanation of how shoulder couplings work to ensure sealing and
how their flexible design allows them to adapt to slight misalignments or deformations during installation.
1. Sealing Performance Shoulder couplings
Are designed to provide a strong, reliable seal, even under challenging conditions. The sealing performance is achieved through several key features:
a. Welded Ring Connection
_
The shoulder coupling features a welded ring at each end of the pipe. These rings are welded directly to the pipe ends, ensuring a robust and secure connection. The welds provide a solid, leak-proof seal at the interface between the coupling and the pipe.
The welded rings also prevent the pipe ends from deforming or moving during installation, ensuring that the coupling maintains its position for a reliable seal.
b. Compression Seal
_
When the shoulder coupling is installed, the compression seal is formed between the pipe ends and the coupling. The bolts and nuts are tightened, which causes the coupling to compress against the pipe ends, further enhancing the sealing integrity.
The compression action presses the sealing surfaces of the coupling tightly against the welded rings, ensuring no gaps or leaks at the connection point.
c. Gasket and Material Selection
_
Shoulder couplings often use gaskets made from materials suited to the application (e.g., rubber, EPDM, NBR). These gaskets sit between the coupling and the pipe ends and play a vital role in sealing, preventing any leakage at the joint.
The gasket material is chosen based on the type of fluid being transported (e.g., water, oil, gas) to ensure compatibility and long-term durability under pressure or temperature changes.
2. Flexibility and Adaptation to Misalignment
One of the key advantages of shoulder couplings is their flexibility, which makes them suitable for installations where slight misalignments or deformations occur.
This flexibility is essential for ensuring the system’s reliability, even when there are minor installation imperfections.
a. Tolerance for Misalignment
_
Shoulder couplings are designed to tolerate slight axial and angular misalignments between the two connected pipes. During installation, if the pipes are not perfectly aligned (which can often happen in field installations), the flexible design of the shoulder coupling allows it to absorb these minor misalignments without affecting the integrity of the connection.
The flexibility ensures that the pipes are still securely connected, even if there is a slight deviation from perfect alignment. This is crucial in large or complex pipeline systems where exact alignment can be challenging.
b. Accommodating Pipe Deformation
_
In some cases, pipes may undergo slight deformation due to pressure, temperature changes, or installation stress. Shoulder couplings are designed to adapt to these minor deformations without compromising the connection. The flexible structure allows the coupling to remain tight and secure even if the pipe shapes slightly change.
For instance, if the pipes expand or contract due to thermal changes, the shoulder coupling can accommodate these shifts, maintaining a strong seal and reliable connection.
c. Vibration and Movement Tolerance
_
In environments where pipelines are subject to vibration (such as in industrial or transport applications), shoulder couplings offer additional flexibility by absorbing and dampening vibrations. This flexibility reduces the risk of connection failure due to pipe movement or external stresses.
3. How This Benefits Your Project
RELIABLE SEALING
Shoulder couplings are ideal for applications where sealing integrity is critical, such as in water, oil, or gas pipelines. The welded rings, gaskets, and compression mechanism work together to ensure that the connection remains leak-free.
ADAPTABILITY
The ability to absorb misalignment and deformation makes shoulder couplings perfect for installations where pipes may not align perfectly or where movement is expected. This feature reduces the risk of installation errors or long-term wear.
COST-EFFECTIVE
The flexibility of shoulder couplings means that they can be used in a wider range of applications without requiring precise pipe alignment or additional supports, which can lower installation costs and time.
Shoulder couplings provide excellent sealing performance and flexibility, making them suitable for a variety of challenging applications. Their ability to accommodate slight misalignments and deformations during installation ensures a reliable connection that remains leak-proof even under varying operational conditions. Whether you are dealing with large-diameter pipes, thin-walled pipes, or complex pipeline systems, shoulder couplings offer a cost-effective and durable solution.
If you’re working on a project that requires a strong, flexible, and leak-proof connection, shoulder couplings are a great choice to ensure the longevity and reliability of your pipeline system.
Installation
1, Preparation
_
● Tools and Equipment:
Welding equipment (e.g., welding machine, welding rods), Pipe cutting tools, Measuring tools (e.g., calipers, level), Tightening tools (e.g., wrench, bolts, nuts), Shoulder coupling and welded rings
● Check the Pipe:
Ensure both pipe ends are smooth, free of burrs, and undamaged. The pipe surfaces should be clean, free from oil, dirt, or other contaminants to ensure good welding quality.
2, Welding the Welded Rings
_
● Position the Welded Rings:
Align the welded rings to the ends of the pipe, ensuring the center of the ring is aligned with the pipe axis. Use measuring tools to verify that the position of the welded ring is correct.
● Weld the Rings:
Using the appropriate welding method based on the pipe material and welding requirements, weld the rings to the pipe ends. Ensure the welds are even, strong, and free from defects like porosity or cracks. The quality of the welds on the rings directly impacts the installation and sealing performance.
3, Installing the Shoulder Coupling
_
● Align the Pipes:
After welding and cooling, align the two pipe ends, ensuring they are in a straight line.
● Place the Shoulder Coupling:
Fit the shoulder coupling onto both pipe ends, ensuring the coupling is properly seated against the welded rings on both ends.
4, Tightening the Bolts and Nuts
_
● Install Bolts:
According to the design of the shoulder coupling, use the appropriate number of bolts and nuts to secure the coupling to the pipe ends. Ensure each bolt is installed tightly, and the nuts are torqued to the specified values.
● Check Alignment:
Before tightening, verify that the shoulder coupling is properly aligned with the welded rings, ensuring there is no misalignment or gap between the pipe ends and the coupling.
5, Inspection and Testing
_
● Seal Inspection:
After installation, check the sealing integrity at the connection points to ensure there are no loose bolts or any potential leak points.
● Pressure Test:
Perform any necessary pressure tests based on the pipeline’s operating environment to ensure the coupling connection can handle the system’s normal operating pressure.
● Check for Alignment:
Ensure the pipe ends are aligned properly and make sure the joint is tightly sealed to avoid leakage during operation.
6, Completion
_
● Clean the Area:
After installation, clean up all tools and equipment, ensuring no welding debris or other materials are left behind.
● Record Installation Information:
Document the installation date, personnel involved, materials used, etc., for future maintenance and inspection purposes.
By following these steps, you can ensure the proper installation of the shoulder coupling,
providing stable and reliable pipe connections. If any issues arise, make adjustments based on the pipe type and the operational environment.